How Coil Specialist Future-Proofed Their Business with a Connected Workforce Solution
June 08, 2023
Blog
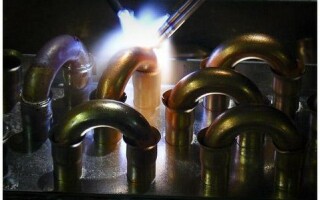
Coil Specialist Inc., a family-owned business based in Texas, specializes in manufacturing heat transfer, tube, and fin coils for the HVAC, refrigeration, and pool industries. To expand its operations, the company aimed to improve operational visibility and engage its workforce in improving processes.
For years, the company relied on its operators to manually track all production data, which left workers without any real-time visibility into what was happening on the shop floor. In addition, competition for area workers was also tight in Gilmer, TX. To attract and retain younger and skilled workers, Coil Specialist knew it needed to digitize its key operational processes to provide a better work experience.
The manufacturing operation needed a solution to help create a culture of continuous improvement where frontline workers could suggest and drive operational changes, while also providing transparency into the business and improving performance. They considered reviewing connected workforce solutions as the answer.
Operations Manager Brian Pasquier discovered QAD Redzone Connected Workforce Solution from a trusted customer and started researching the solution. He valued the fact that the solution allowed them to look inside their business, something they were desperately looking for. It was going to help create a culture Coil Specialists was looking for and to be able to become a more nimble and adaptive industry player by digitizing key operational processes.
By implementing a connected workforce solution, Coil Specialists was able to create a visual factory, coaching production staff and supervisors to adopt Lean production techniques, improving overall operations, achieving cost savings, and sustain all goals – all within the first 90 days of implementation.
Integration started with Coin Specialist’s HVAC refrigeration line. The solution, a cloud-based platform that collects real-time data from connected devices, including production status, product quality, and material waste, allowed employees to view the shop floor data available to the teams via overhead TVs, iPads, and smartphones. Teams could then use the solution on their phones to closely monitor production conditions and share strategies for solving problems.
QAD Redzone coaches worked directly with teams, one-on-one and in groups, to help them adopt the new processes, practice key scenarios, and strategize how to overcome any obstacles.
The implementation of QAD Redzone allowed Coil Specialists to move in the direction they wanted to go in and solve a lot of issues they saw on the horizon. By investing in technology now, they could eliminate the stress of keeping up with their numbers and continue to grow and develop leaders to help with other aspects of their business. The solution also enabled them to work smarter, not harder.
Coil Specialist workers were able to share strategies for solving problems, and team members were pushed out of their comfort zone by being encouraged to speak up in daily huddles about issues they were facing, challenges and/or solutions. Although many were hesitant at first, they realized this was their opportunity to share their ideas to improve operations.
The implementation of a connected workforce solution helped the company attract and retain staff by providing an overall better work experience. The company was able to develop leaders for generations to come. It created positive staff engagement and competition around improving overall processes.
Results show that in 90 days Coil Specialists was about to:
- Identify and close 150 action items
- Achieve a 37% increase in productivity
- Improving overall equipment effectiveness (OEE) by at least 12 points
- Achieve cost savings of $500K for smaller factories and $1M+ for larger factories
The implementation of QAD Redzone Connected Workforce Solution has helped Coil Specialist to future-proof its business with digital processes. The solution has enabled the company to improve operations in so many ways from operational visibility, engaging its workforce in improving processes, and becoming a more nimble and adaptive industry player.