The Business Case for IoT in Manufacturing
August 29, 2019
Story
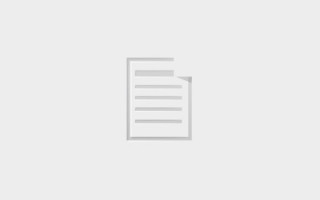
This article describes the value of IoT for manufacturing and defines an ROI model for building a business case and tracking results related to IoT initiatives.
Manufacturers today are under tremendous pressure from management and customers to deliver high quality products and services at low costs in a minimum amount of time. Today's market leaders rightly believe that their return on investment (ROI) is multidimensional, determined by not just costs, but also measures of customer satisfaction and more. Companies are turning to the Internet of Things (IoT) to collect accurate data and convert it into actionable information to help add this extra dimensionality to ROI calculations.
IoT is creating new opportunities for companies to enhance their services, gain insights from accurate and timely data, improve business processes and differentiate their offerings. This article describes the value of IoT for manufacturing and defines an ROI model for building a business case and tracking results related to IoT initiatives.
INDUSTRY 4.0
IoT has the potential to change the face of the manufacturing sector, so much so that it has been called the fourth industrial revolution. If the pace of advancement in technology is anything to go by, intelligent factories will soon become the norm, rather than the exception. The four main factors of a smart factory are IoT, data, automation and precision:
- The Internet of Things: IoT is the torchbearer of the smart factory. More than just sensors and other “things,” it is the connection of the things to each other in order to facilitate the collection and transfer of data. Multiple types of sensors with the ability to connect to the cloud are installed in the factory to gather data, which helps to optimize the factory.
- Data: Data plays an important role in a smart factory, making it possible for managers to gain insights for streamlining manufacturing processes, increasing ROI, and more. IoT can also contribute to an enterprise’s big data initiatives, with the ability to collect and transfer massive amounts of structured and unstructured data to save in a centralized location for real-time or future analysis.
- Automation: The IoT system in a factory setting can work autonomously to drive and monitor production with minimal human intervention. And equipment longevity is improved by IoT-enabled predictive maintenance, where IoT sensors can detect faults on the basis of the data collected and independently make decisions to stop faulty equipment before it fails.
- Precision: IoT sensors and other equipment are designed to sense and measure to an incredible level of precision, making them appropriate for almost any factory application, no matter the size and no matter how exacting.
INDUSTRIAL AUTOMATION
IoT is ideal for increasing the level of automation in today's factories. For manufacturing companies that have already installed sensors, actuators and other low-level devices in their existing industrial automation systems, upgrading and retrofitting IoT-enabled devices is an easy step.
These companies can take advantage of the increase in network speeds and memory size delivered by today's commercial off-the-shelf sensors and other hardware along with well-established cloud platforms. The technology today is robust enough to not hamper the design of the systems as was the case in the past. This will give plant managers new levels of control and insights regarding the production floor.
It’s not enough to just collect data. The key to the success of industrial automation is making use of the data that are gathered. The IoT-enabled industrial automation networks collect data and then transfer it to the cloud or to an internal datacenter. There, Hadoop (an open source framework) and other technologies are implemented to apply data science techniques and predictive models to analyze the data into useful information.
Another reason for manufacturers to adopt IoT in their factories is to delay or prevent obsolescence. Many industrial automation systems in factories today will outlive vendor support. By upgrading to IoT systems, plant operators can extend both the functionality and the lifespan of these systems. And as the cost of internet bandwidth and storage has been steadily decreasing, companies can now store terabytes of data very inexpensively compared to even a few years ago.
IoT takes industrial automation even further by interfacing with robust machine-to-machine (M2M) systems. This covers a broad range of technologies used to enable networked devices to exchange data with each other and perform actions without human assistance. M2M technology has applications in almost every area of manufacturing including ensuring plant and personnel safety.
For example, the company's safety engineers can establish safety limits for each piece of equipment. If IoT sensors detect a rise in equipment temperature that brings it to that safety limit, the system will record this fact and it will trigger an immediate shutdown of the affected equipment. Or if the company does not want to implement an automated shutdown system, it can set up the sensors to transmit data to key personnel with remote monitoring ability on their desktops, tablets or other devices. These employees can then send instructions to the machine to shut down, reduce its production rate or carry out any other function in order to take care of the safety issue.
THE IOT VALUE PROPOSITION
IoT also delivers value in areas other than on the factory floor, including remote monitoring, remote service, usage analysis, ERP/CRM integration and much more. Core business processes like billing, field service, product registration, compliance, consumable management, recalls and warranty management can all be improved with connected product data.
On the other side of the IoT market, the selling and marketing of connected products can deliver a competitive advantage and drive revenue growth. Following are examples of demonstrating the value that can be derived from enabling IoT in your company.
THE IOT-ENABLED SMART FACTORY
A smart factory leveraging IoT will install multiple sensors to detect temperature, humidity, noise, light, vibrations and volatile organic compounds in its factory. The factory also has specialized sensors to track the working of all of its machines and equipment, to identify the location of vehicles that carry raw materials and finished goods as well as to manage the supply chain.
The data collected by all these sensors are transmitted to a cloud-based storage system. There, principles of data science are applied in order to get meaningful information and gain insights that are presented in the form of interactive reports and charts. Managers and other authorized employees access these data visualizations from the cloud to supervise and manage the working of their respective departments.
This information is used to maintain the right temperature, humidity, light and noise levels in the manufacturing unit, along with ensuring compliance with safety standards. The IoT and data science ensure that any defects are detected in the early stages and downtime can be prevented, and the machinery is easily monitored and maintained if faults are detected.
Vehicles are monitored in real-time to ensure that the finished goods are delivered to distributors and retailers on time. Employees are made aware of the arrival of raw materials well in advance and are prepared to start production right away in order to avoid wasting time. New or alternative routes are suggested to drivers in order to ensure that they reach their destination without wasting time and fuel.
Managing the inventory is easy for the manufacturer, as they know exactly when to order required raw materials just in time, avoiding costs for storing goods any longer than necessary. Low stock will trigger order reminders to avoid delays in the production of goods. IoT also connects the factory to warehouses, distribution centers, retailers, suppliers and customers to facilitate supply chain management by allowing real-time information sharing.
The smart factory successfully lowers costs by avoiding fuel and power wastage. Downtime is decreased to a great extent, allowing uninterrupted production in the manufacturing unit. Moreover, sensors installed on the finished goods help identify faults in products, so that they can be rectified as soon as they are detected to decrease losses and offer quality products and services to consumers. The factory also saves on warranty management.
CONCLUSION
IoT is a driving force for manufacturers today. With advancement in smart sensors and cloud technologies, companies can enjoy more intelligent services at a lower cost. The time is now to make your company smarter and more efficient than before.
ESSENTIAL COMPONENTS FOR IoT IN MANUFACTURING
- SENSORS: Sensors are the driving force behind the IoT ecosystem in manufacturing. They collect and consolidate data in real time and have the ability to integrate with direct database systems, legacy ERP systems or data warehouses.
- NETWORK CONNECTIVITY: Internet connectivity has become more reliable and affordable, allowing manufacturers to deploy it in their units.
- IoT PLATFORM: The most important part of a smart factory is the IoT platform. Before implementing an IoT integration plan, it is very important to ensure that you have a compatible open architecture in place and that any M2M applications you consider meet your digital business requirements.
- DATA ANALYTICS & VISUALIZATION: Data analytics is the science of analyzing large amounts of data to uncover patterns and other insights that may be overlooked by humans. With interactive data visualizations you can conceptualize future business strategies by drilling down into charts.
To read more, check out:
Actian Releases Actian Zen for Mobile and IoT, Improving Data Management at the Edge
Enterprise Containers and the IoT – Foundations for Embedded Developers
The TALQ Consortium Presents an Integrated Ecosystem for Smart Cities