Manufacturers Must Make Data-Driven Decisions: 6 Reasons Why
August 04, 2022
Blog
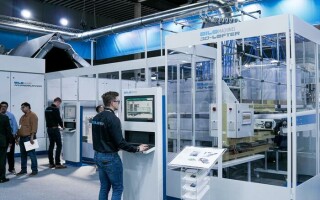
The major difference between a thriving business and a declining business is usually the quality of the decisions its management makes. To understand how sensible decisions are made, we need to comprehend how decisions go awry.
In today’s fast-paced manufacturing industry business leaders have to constantly make decisions, and invariably some of them go wrong - that is to be expected. There are common elements that can be identified in wrong decisions. Some of the key reasons why decisions go wrong are:
- Constant distraction: When plant managers and team leaders are constantly distracted by operational challenges, they do not have the space to think through problems. Lack of cognitive power can eventually lead to wrong decisions.
- Human error: All humans have biases and other faults that affect our decision-making ability. This has been the cause of many poor decisions throughout history, and continues to this day. Some part of the current semiconductor shortage can be attributed to human error.
- Multitasking: Decision-makers at manufacturing plants have to focus on multiple things. According to scientific studies, making decisions while multitasking reduces the effectiveness of decisions by up to 40%.
- Lack of data: Information is key to sound decisions. When decisions are made with faulty or incomplete data, they often turn out to be wrong. If you expect sensible outcomes from the decision-making process, it is critical to have the right data at the right time
Data for better decisions
Data-driven decision making relies on robust data and the discipline to commit to decisions that may not at first glance make intuitive sense. The decisions made in this fashion are easily verifiable as they are based on solid data and tied to hypotheses on the outcomes they will create. There is no doubt that decisions with more data inputs will fare better than decisions that relied on less data. Yet, many times managers have had to make decisions with imperfect information.
Today, the situation has changed dramatically as there is often more data available than ever before. Manufacturers that have adopted the Industry 4.0 paradigm have internet-enabled sensors connected to key pieces of equipment providing them with a continuous stream of real-time data on plant operations. This allows them to develop data driven insights, form hypotheses of scenarios of business outcomes they can change, and proceed from there.
Data-driven decisions: Why?
Data improves decision making across different dimensions of plant operations. Some of the key reasons why you should adopt data-driven decisions are detailed in the following sections.
Automation
Many routine and mundane decisions for smooth plant operations have to be made on a continuous basis. More often than not, such decisions can be automated with the availability of the right kind of data and automation technology. This frees up mental space for employees to focus and helps them make better decisions where human input is absolutely necessary. A smart factory becomes smarter by automating more and more processes, relying on better data.
Forecasting
One of the benefits of having a large amount of data is the ability to analyze it. Analysis can also be done to project future data. With sufficient data, machine learning algorithms can reliably predict future demand, the raw materials required to meet the demand, the working capital required, etc. Reliable predictions of the future also help in making better decisions.
Efficiency
Data-driven decisions place significant importance on cold, hard numbers. This data contains information on the operational characteristics of various machines in the plant. Deep analysis of this information reveals various avenues of improving processes and other operational factors. Thus, decisions reliant on data can vastly improve efficiency.
The major caveat is the kind of data used - not every kind is sufficient to drive efficiency improvements. The right kind of data, which has undergone rigorous processing, fetches positive results. Also, tools to visualize data help to make better sense of it. This in turn helps to identify inefficiencies precisely. Mending those identified faults gives you avenues for quickly improving ROI.
Visibility
Complete real-time data from all parts of the plant helps to have a bird’s eye view of plant operations from a central location. This visibility can be enhanced by the appropriate use of data visualization tools. The overall visibility helps you identify how different operational elements interact with each other. This, in turn, reveals opportunities for operational improvement which can be implemented, monitored, and fine tuned with ongoing use of data to determine if the outcomes are matching expectations.
Agility
Many variables that impact the success of any business change quite rapidly. Manufacturers have to be agile to remain competitive and relevant in fast-changing business environments. The above-mentioned factor of forecasting plays a huge role in manufacturer agility. Better-quality data and better-visualized data can help organizations quickly maneuver dynamic business conditions. It is way better than flying without a map or radar.
Cost
Continuous, real-time data on plant operations gives great insight into plant operations. It also helps to magnify where the manufacturer goes wrong. As we have seen in previous sections, data-driven decisions help to improve efficiency, increase automation, improve agility, and also enhance visibility. All these factors help to cull waste in the plant and its operations. This means data-driven decisions help reduce the cost of plant operations significantly.
Data is not the end-all
Data-driven decisions have many advantages and must be embraced with open arms. But, data alone should not be the arbitrator of plant operations. Human intuition and judgment also play a significant role in better decisions. It is best exemplified by the disaster of the space shuttle Challenger in 1986. NASA discounted human intuition and relied solely on data, ending up with a catastrophe. While embracing data-driven decisions, you should not completely drive out common sense and intuition.
For over 30 years, Eric Whitley has been a noteworthy leader in the Manufacturing space. In addition to the many publications and articles Eric has written on various manufacturing topics, you may know him from his efforts leading the Total Productive Maintenance effort at Autoliv ASP or from his involvement in the Management Certification programs at The Ohio State University, where he served as an adjunct faculty member.
After an extensive career as a reliability and business improvement consultant, Eric joined L2L, where he currently serves as the Director of Smart Manufacturing. His role in this position is to help clients learn and implement L2L’s pragmatic and simple approach to corporate digital transformation.
Eric lives with his wife of 35 years in Northern Utah. When Eric is not working, he can usually be found on the water with a fishing rod in his hands.