Qualifying Medical Lab Equipment without the Engineering Overhead
May 22, 2023
Blog
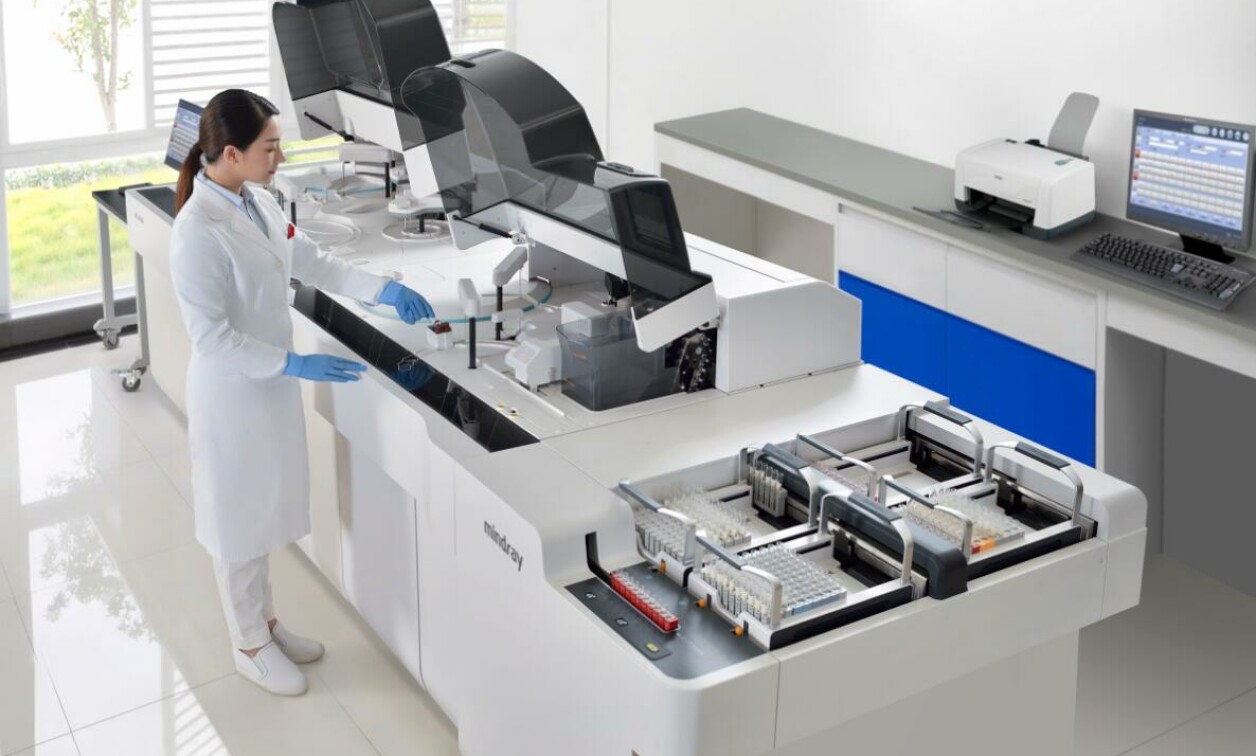
Today’s healthcare professionals depend on medical laboratories to validate diagnoses of patient conditions. Where precision is required, these labs use in-vitro diagnostics (IVD) to test biological samples for things like infectious and autoimmune diseases, genetic and metabolic disorders, allergies, and even cancer.
IVD equipment consists of analytical instruments like mass spectrometers, spectrophotometers, genetic sequencers, and polymerase chain reaction machines for testing samples; automation subsystems that calibrate the machine and manage control tasks like robotic sample handling, reagent dispensing, solution mixing, and internal quality control checks; and interfaces to documentation and other information systems where reports are generated and sent to healthcare providers for review.
These capabilities require a fair amount of electronic content in modern IVD machines, including microprocessors and digital signal processors, sensors, analog-to-digital converters (ADCs), wired and wireless communications interfaces, and graphical displays. Without these technologies, IVD equipment couldn’t analyze samples and output results with the precision, speed, and efficiency doctors need to develop corresponding patient treatment plans.
But all these electronic components also add the complexity of technology lifecycle management for the medical labs who own and operate IVD systems.
Off-the-Shelf In-Vitro Diagnostics
To simplify technology infrastructure management, medical laboratories are adopting system architectures that decouple advanced IVD instrumentation from the data processing and automation electronics mentioned previously. Increasingly, this is achieved by connecting IVD test and analysis hardware to commercial-grade workstations over standard interfaces like USB, serial, Ethernet, and/or wireless.
Compared to more integrated deployments, this approach comes with advantages. It allows the processor subsystem, display, automation, or other functions to be upgraded or replaced without disturbing sensitive instruments by simply swapping out the workstation. It also reduces the bill of materials for much of the electronic content to a single SKU – the workstation itself. Finally, it can minimize cost, as off-the-shelf workstations benefit from economies of scale.
But there are also drawbacks of this approach, and for highly specialized and regulated equipment like IVD machines these are often presented in the form of qualification challenges. Consider that IVD machines are typically classified as long-lifecycle systems that require 5-7 years of support, but to keep pace with the latest CPU and chipset technology, many mainstream workstation vendors release new versions every 12-18 months. Support for legacy products usually declines shortly thereafter.
This may not seem like much of an issue on the surface but switching to a similar workstation platform with just a few component revisions can have serious implications in terms of reintegration and qualification work. The reason is that the workstation is typically designed in to control the primary user interface, and many of the peripherals that comprise an IVD machine (like instrumentation for genetic sequencers and mass spectrometers) are uncommon.
As a result, every PC must have its own custom image, drivers, and libraries to control each different piece of equipment, and every piece of hardware and the software package that goes with it must be qualified.
“A lot of these customers are using their own proprietary software or are hooking it into their own systems. Their engineers have to make sure that the workstation works with their own infrastructure,” says Jason Waldman, Business Development Manager at Advantech.
“We had one customer tell us it takes between 15 and 20 engineers six-to-eight weeks to qualify new workstation PCs because they're working with their own unique software and their own peripherals that they have to make sure work perfectly with the workstation when it comes in, no matter what hardware changes have been made.”
Any savings of an off-the-shelf workstation to power IVD systems are likely neutralized by the large non-recurring engineer (NRE) investment required to requalify the system to a new PC if replacements or upgrades are required. But the alternatives – like opting for a completely custom workstation build that locks you into a specific design – aren’t much better.
How Customization Reels in Revision Control for Advanced In-Vitro Diagnostics
A middle ground that comes with the cost benefits of off-the-shelf workstations and the design assurance of working with a trusted integration partner would be the ideal middle ground for IVD OEMs and their users. Advantech is threading that needle with the Valor series of U.S.-designed and assembled workstations, which can be customized from one of three base form factors, standard I/O options, and a selection of Intel® Core-i™ processors to meet the needs of virtually any edge computing use case. Advantech can also provide custom badging and imaging, as well as BIOS modifications to fit any need.
Best of all for IVD stakeholders, Valor series platforms like the Valor Mini (pictured below) are supported by Advantech for up to 7 years. This ensures product longevity, consistency, and shifts the responsibility for revision control from the IVD customer to a trusted technology partner.
One of three Advantech Valor product offerings, the Valor Mini workstation features 6x USB, 2x Ethernet, and 2x HDMI interfaces as standard but can be configured to support optional storage, serial ports, or additional USB interfaces as well. The 2.2” x 7.9” x 7.9” mini PC is designed around 35 W 10th generation Intel® Core™ i processor technology and up to 64 GB of DDR4 SDRAM, offering an optimum balance of performance and power consumption for IVD functions like GUI management, automation control, etc.
“We view not having to qualify new SKUs as saving dollars for the customer and saving their engineering team time that they can use to do other stuff,” says Matt Wieborg, Solution Architect Supervisor and FDA Manager at Advantech. “So rather than have to worry, “Is this PC the same one that I’ve been getting?", it's consistent. It’s going to be the same thing. It's going to last them for up to seven years.
“It's really about helping increase the efficiency of our customer base, as well as just providing them a great custom PC.”
To learn more about ways the Advantech Valor series is helping healthcare, automation, and retail customers streamline their technology infrastructure, visit advantech-e.com/valor.