World's longest multilayer flexible printed circuit spans 26m metre (85 feet) wings of unmanned aerial vehicle
March 26, 2019
Press Release
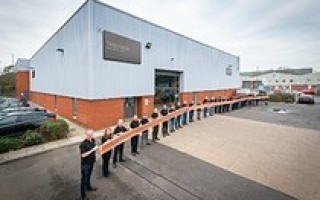
FPCs deliver critical 60% weight saving over wire harness for power and control
Tewkesbury, UK: Trackwise has shipped a 26-metre long multilayer, flexible printed circuit (FPC), believed to be world’s longest ever produced, for distributing power and control signals across the wings of a solar-powered, unmanned aerial vehicle (UAV). The circuit is one of over fifty supplied by Trackwise into this vehicle.
The entire interconnect system (power and signal) of the vehicle is made of FPCs representing an estimated total systems weight saving of 60% over traditional wire harness. This will enable the UAV, which is being manufactured in the US, to achieve higher payload and/or improved speed and range. The FPCs are manufactured using Improved Harness Technology™ (IHT), a patented, reel-to-reel manufacturing technique. Conventional FPCs are rarely more than two metres in length, primarily due to limitations of manufacturing processes. IHT overcomes these limitations, enabling FPCs of unlimited length to be produced.
The UAV’s flexible circuit is based on a polyimide substrate. The planar structure of the circuit dissipates heat better than conventional wiring, enabling higher current carrying capacity for a given weight of copper conductor. Printed manufacturing ensures circuit consistency, fewer connection points are needed so reliability is enhanced, and the FPC is easier to install than wire harnesses, reducing a vehicle’s assembly time and cost.
Trackwise CEO, Philip Johnston, said: “There are many new applications emerging for long, lightweight FPCs but aerospace is a natural fit: weight savings, high reliability and cost effectiveness are critical. We’re also seeing growing interest from a variety of sectors including medical and automotive. For the latter, manufacturers are challenged to reduce vehicle weight to improve fuel efficiency at a time when there’s an ever-growing array of electrical and electronic circuits in their vehicles. In particular, electric vehicles are accelerating this trend.”
+++ ends +++
For further information and reader enquiries:
Neil Bartlett, Trackwise Limited
Phone: +44 1684 856033
Email: [email protected]
Agency contact:
Rachel Sandeman, Publitek Limited
Phone: +44 7738 682833
E-mail: [email protected]
About Trackwise
Trackwise manufactures to customer specification, specialist products using printed circuit technology.
Its radio frequency (RF) division is primarily focused on the manufacture of printed antennas for communications infrastructure and other high-precision printed circuit products. Here, Trackwise’s materials expertise, particularly in RF and microwave laminates, enables it to optimise the performance of its customers’ products.
The Trackwise flexible printed circuit (FPC) division employs patented Improved Harness Technology™ (IHT) to create flexible, multilayer circuits of unlimited length. IHT overcomes the previous length constraints of conventional FPCs manufacture (typically 610mm) and facilitates the replacement of conventional wire harnesses in a diverse range of applications, particularly in the aerospace and automotive sectors.
FPC benefits over traditional wiring harnesses include substantial reductions in weight, size and installation time. In addition, the consistency, reliability and performance of system interconnect are improved. Their planar nature also makes them entirely suited to embedding into composites.
Trackwise serves customers in Australia, Asia, Europe, and North America from its headquarters in Tewkesbury, UK. More information can be found at: trackwise.co.uk.