Long Distance Bus: The Industry Requirements Driving this Technology
June 08, 2021
Blog
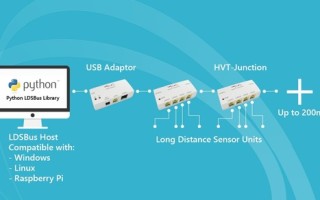
The global IoT market is projected to grow from $235 billion in 2017 to $520 billion in 2021 (according to Bloomberg), representing a 22% compound annual growth rate.
Such high levels of growth are expected to continue throughout this decade, as Industry 4.0 and Logistics 4.0 implementations are rolled out - with increases in productivity, enhanced process efficiencies, shortened equipment downtime, and reduced labor all being realized as a result. The falling costs of sensors and transducers, increased data storage capacity, and greater network access are further factors that are helping to accelerate IoT deployment activity.
Any IoT system will be comprised of three parts. These are a network of sensors and actuators connected to a gateway, which is subsequently connected to the cloud. Data that is acquired by the sensors will be collated in the gateways and relayed to the cloud, where it can then be processed and analyzed. Control messages flow from the cloud to the gateway, which effectively acts as a relay between the cloud and the sensor/actuator devices at the network edge. Some gateways incorporate processing capabilities. This helps to reduce the data transfer required, so that there is no risk of excessive congestion. It also means that real-time response can be benefitted from, thereby preventing the delays of data having to go all the way back to cloud-based systems and then for a response message to be returned. Such gateways are known as edge processors. Cloud-based processing and storage resources enable data to be scrutinized or displayed on dashboards. It also processes alerts - which can be sent as SMS, emails, or push notifications to relevant devices, so actions can be taken.
Deploying an IoT system of sensors and actuators is not without its challenges. Some of the challenges that engineers face relate to the distance of sensors/actuators from their assigned gateway or the density of sensors/actuators in a given area. The speed, security, and operational reliability of the communication infrastructure can pose other challenges. Finally, there is the powering of the network to consider. Range is mainly solved by deploying wireless sensors, however, in industrial settings, this is not possible always because of concrete and steel building structures that obstruct and reduce signal strength. Transmitting at higher power levels will mean that batteries are drained too quickly (thus increasing the associated maintenance costs, as batteries need to be replaced more frequently). Furthermore, EMI noise from other equipment can impact the effectiveness of wireless communication, and such transmissions are relatively easy for third parties to snoop on. It is often therefore more appropriate in industrial settings to employ a wireline solution.
Figure 1: Schematic showing an LDSBus implementation
To address the issues just outlined, Bridgetek has developed the Long Distance Sensor Bus (LDSBus). This is a powered and differential serial bus that can operate over distances of up to 200m. A head unit distributes power over the bus to all the peripheral sensor/actuator units attached to the bus. The bus is powered at 24V and a single head unit manages and supervises slave units, known as LDSBus Units (LDSUs). Sensors and actuators may be attached to the bus and controlled by the head unit. The bus operates at 230kbps data rates and provides sufficient bandwidth to control up to 127 LDSUs on the bus.
The LDSBus architecture allows an LDSU to incorporate as many as 10 sensors and/or actuators. Bridgetek has developed its LDSU sensors and actuators for customer implementation. These are:
- 4-in-1 sensors that incorporate temperature, humidity, ambient light, and motion-sensing capabilities, with all of this functionality being housed in a compact form factor.
- Indoor Air Quality (IAQ) sensors that measure and monitor air quality levels inside buildings, workspaces, and industrial sites.
- Thermocouple based temperature sensors that are capable of extreme temperature monitoring (up to 1372°C).
- CO2 gas sensors for photosynthesis process monitoring (in a smart farming context) or for monitoring employee wellbeing (within the daily working environment).
- Pressure sensing sensors to detect pressure changes.
- Soil moisture, pH level, and electrical conductivity measurement sensors for monitoring precise nutrient levels for optimum crop yield (again, being of relevance in smart farming).
Bridgetek has also developed other forms of hardware that can be used with LDSBus. These items include:
- Trailing-edge LED dimmers for the controlling/dimming of lighting.
- On/off relays for pump and motor control purposes.
- IR controllers for controlling infrared devices.
LDSUs attachment points into the backbone of the bus are created by inserting high-voltage T-junctions into bus segments. Each of these junctions consists of an upstream and downstream RJ-45 connector, which is used to extend the 24V backbone. This backbone is built out of Cat5E cabling. An array of 4 RJ11/RJ12 connectors enables the attachment of up to 4 LDSUs. The high-voltage T-junction converts the 24V power supply to a 5V supply suitable for the LDSUs. The last LDSU on the bus (the one furthest away from the head unit) has to enable its bus termination to maintain stable communication.
The Bridgetek LDSBus’ powered backbone removes the need for batteries and associated labor that must be assigned to battery replacement. The differential nature of transmission ensures high common-mode noise rejection (which mitigates EMI problems), while the wired nature of the bus means that ‘man-in-the-middle’ wireless snooping is no longer a concern. Three buses (each with a 200m radial reach) can cover the area of 12 football fields. LDSBus can incorporate up to 381 LDSUs (or 3810 sensors and actuators) so that high node densities can be achieved.
To support the hardware involved, Bridgetek provides a software utility called the LDSU Programming Utility. This can program the LDSU address, name, and termination. Sample Python scripts and the Bridgetek LDSBus Library demonstrate how to implement an LDSBus head unit (master) on Windows, Linux, or Raspberry Pi.