How 10BASE-T1S Ethernet Simplifies Zonal Architectures in Automotive Applications
January 10, 2025
Blog
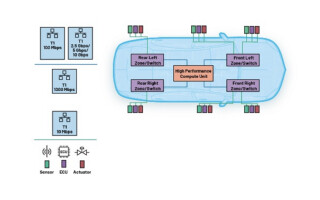
With modern cars aiming to provide home-like comfort and entertainment, the demand for electronic control units (ECUs) has grown exponentially. However, older bus technologies and electrical/electronic (E/E) architectures are struggling to keep up. This article explores how Ethernet technology transformed cars into fully connected experiences.
Introduction
The use of electronic control units (ECUs), which control each component of a vehicle’s operation, in automobiles has grown rapidly since their first installation by Volkswagen in 1968. More and more features are added to modern cars to offer the driver and passengers the same level of experience as at home or work in terms of comfort and entertainment. As a result, most bus technologies and electrical/electronic (E/E) architectures—some of which were established decades ago—are unable to keep up with the growing demand for ECUs to interact and process large amounts of data.
Moving Toward an Improved Network Architecture
Current vehicle ECUs are divided into almost isolated, functional domains such as powertrain, chassis, infotainment, or comfort. Sensors and actuators are dispersed throughout the vehicle and wires flow throughout the vehicle to link to its functional domain ECUs as illustrated in Figure 1, increasing the vehicle’s complexity, cost, and weight. Cables are the third heaviest part of the car and have a huge impact on the vehicle’s range.
Legacy bus technologies like controller area network (CAN), FlexRay, and local interconnect network (LIN) were introduced decades ago to facilitate communication between various ECUs and simple sensors or actuators. In contrast, high speed Ethernet is utilized for communication between different domains. To facilitate data transfer between different bus technologies, expensive dedicated gateways are employed within the ECUs.
Figure 1. Domain architecture example.
The complexity of the architecture expands as the number of features increases. Extending existing features or introducing new ones necessitates significant development, implementation, and testing. The goal of original equipment manufacturers (OEMs) is not only to accelerate innovation while reducing costs, but also to generate post revenue sales. Compared to other consumer products such as mobile communication devices, a vehicle architecture has significantly longer development cycles. Breaking up the link between hardware and software toward a software-defined vehicle is a target set by many OEMs.
Two major challenges prevent realizing this vision:
- The static functional domain architecture
- Wiring complexity
The ideal architecture identified is a zonal-based view of the vehicle (see Figure 2). Local ECUs serve all functions regardless of the domain. These ECUs are then connected to zonal controller devices, which concentrate processing power in a small number of units across the vehicle. The communication between zonal ECUs and the high performance compute unit takes place via high-speed point-to-point links. According to CARIAD (a subsidiary of Volkswagen Group), this will replace over two dozen ECUs and wiring harnesses longer than a kilometer.1
With cutting-edge technology transforming vehicle design and performance, the automotive industry is going through a significant vehicle network architectural transition. Implementation of technologies such as vehicle-to-vehicle communications, augmented reality dashboards, and self-driving adds complexity, cost, and the need for more electronics. By 2030, it is estimated that these technologies will increase automotive electronics by up to 45%.2
With the introduction of zonal architecture, numerous electrical components and control systems are consolidated and centralized into predetermined zones within the vehicle. Now nodes are dependent on their location and not on their functional ECUs. The network is made simpler, which results in less weight and an increase in fuel efficiency. Additionally, this architecture makes scaling simpler because new features and systems may be added without requiring extensive modifications. Over-the-air software upgrades may now be made more efficient by delivering through the vehicle’s central computer unit.3 OEMs may now remotely enhance features by offering customization to the customer and adopting post-sales strategies such as advanced driver-assistance system (ADAS), autonomous driving or comfort, and infotainment features.
Bridging the Challenges
Legacy bus technologies lack the performance capabilities, such as throughput and quality of service, required in this new architecture. Now, another well-established technology has made its way into the automotive industry: Ethernet.
For decades, Ethernet technologies have evolved with the demand for higher data rates by developing new physical layers (PHYs), thereby keeping the higher (protocol) layers identical or at least compatible. Some speed grades even work on identical harnesses. Network features are serviced by higher protocol layers, mainly in software.
Initially, Ethernet was not specifically tailored for automotive environments, lacking features like electromagnetic compatibility (EMC) and power efficiency. Also, using shielded cables with two or four pairs of wires is contrary to the goal of saving weight. The automotive industry standardized a single twisted pair cable solution, prompting the need for the development of new PHY technologies that meet all the demands of an automotive communication link.
This led to the development of the xBASE-T1 automotive Ethernet standards (T1 stands for a single twisted pair cable). Different data rates are supported for ECU interconnects. In addition, the crossing between different speed grades is handled by much simpler devices: switches. This allows the number of expensive gateways to be reduced.
Although zonal architecture provides a wide platform for all network technologies, issues remain with adaptation to homogenous network architecture, boot time, achieving latency, and throughput. With about 90% of network nodes running at rates of up to 10 Mbps, many automotive network technologies that were formerly sufficient are now incapable of achieving the required throughput.4 These constraints impede the smooth integration of advanced in-vehicle systems. As a result, there is an increasing demand for creative solutions to assure quick response times and improve overall performance.
Effective Implementation of 10BASE-T1S
By extending Ethernet to the edge node, the system has a robust network and packet movement is simplified. 10BASE-T1S is an integrated part of the IEEE 802.3-2022 collection of Ethernet specifications and OEMs have begun to implement this Ethernet PHY technology, with plans to have it on the road by 2025. The OPEN (One-Pair Ether-Net) Alliance, a working group, built its specifications to augment the IEEE standard, aiming to encourage the widespread adoption of Ethernet in automotive industries. Like other automotive link technologies, 10BASE-T1S can operate in multidrop mode configurations. 10BASE-T1S employs a new bus access technique called physical layer collision avoidance (PLCA) on top of carrier-sense multiple access with collision detection (CSMA/CD) to avoid bus collisions. PLCA ensures that latency remains within predictable bounds while maximizing throughput and network efficiency.
Figure 2. Zonal architecture example.
The use of 10BASE-T1S in some common, system-critical applications reduces system complexity, allowing for faster and efficient data transfer within vehicles. These extended system benefits include cost reduction, enhanced security, a unified communication mechanism without the need for complex gateways, and the option of power over data lines, ensuring a smooth integration into the forthcoming generation of software-defined vehicles.
Analog Devices AD330x 10BASE-T1S devices are IEEE 802.3-2022 compliant products. AD330x 10BASE-T1S Ethernet to Edge Bus (E2B) remote control protocol (RCP) devices are designed to work in remote node mode without the need for a local microcontroller, providing a complete hardware solution. This allows for the removal of software from edge nodes. The Ethernet-based E2B protocol, combined with the integrated hardware accelerator for low complexity Ethernet (LCE), provides an efficient means of communication between a central ECU and sensors or actuators. This advanced solution empowers OEMs with full software control by centralizing it in a zonal controller or at a central control unit. This leads to reduced testing and development time, ultimately resulting in lower system costs. ADI E2B transceivers support features such as IEEE 802.1AS, OPEN Alliance TC10/TC14 10BASE-T1S sleep/wake-up, topology discovery to provide intelligent solution with time synchronization throughout the vehicle, power saving modes, and ease of diagnostic process.
Conclusion
The transition from existing automotive domain-based design to zonal architecture marks a significant advancement in the automobile industry. Zonal architecture offers greater flexibility and scalability. It enables centralization of software, minimizes wiring, enhances fuel efficiency by decreasing weight, and maintains cost-effectiveness. Implementing Ethernet consistently throughout the vehicle simplifies network complexity compared to using a combination of technologies. The inclusion of 10BASE-T1S, automotive Ethernet extends automotive Ethernet to the vehicle’s edge, reducing the need for expensive gateways.
E2B technology enables a hardware-only node to reduce the bill of materials (BOM) cost even further. This drastically cuts down on the amount of time needed for testing and development. Decision-makers must be aware of the benefits involved, potential cost savings, and contribution to sustainability in production setting. The E/E architecture with 10BASE-T1S at zones will offer a scalable software platform approach with more advancement in the future generation vehicular network.
References:
1CARIAD LinkedIn post. 2021.
2Rob Margeit. “Opinion: There’s Too Much Technology in Today’s New Cars.” Drive, November 2023.
3“Automotive Ethernet: An Overview.” Ixia, May 2014.
4Eunmin Choi, Hoseung Song, Suwon Kanh, Ji-Woong Choi. “High-Speed, Low-Latency In-Vehicle Network Based on the Bus Topology for Autonomous Vehicles: Automotive Networking and Applications.” IEEE Vehicular Technology Magazine, Vol. 17, No. 1, March 2022.
Andreas Pellkofer graduated from Technical University of Munich in electronic and information technology. He joined Analog Devices in 2006 as an applications engineer working with the Blackfin® processor family. Later he mainly dealt with automotive customers for DSP. In 2013 he moved into a system engineer role in the Digital Video Products Group, focusing on video transport and camera systems for automotive. In 2018 he became part of the Emerging Systems and Technologies Group working on in-cabin vital sign monitoring and hands-on detection solutions. Since 2020, he works on 10BASE-T1S products as part of the Automotive Cabin Experience Business Group.
Madhura Deyanda Poonacha graduated from the University of Galway with a postgraduate degree in marketing management in 2022. She joined Analog Devices in January 2023 as a product marketing specialist for ADI Ethernet to Edge Bus (E2B) 10BASE-T1S products in the Automotive Cabin Experience Business Group.