Medical Innovation and the Custom Optical Sensor
April 23, 2020
Story
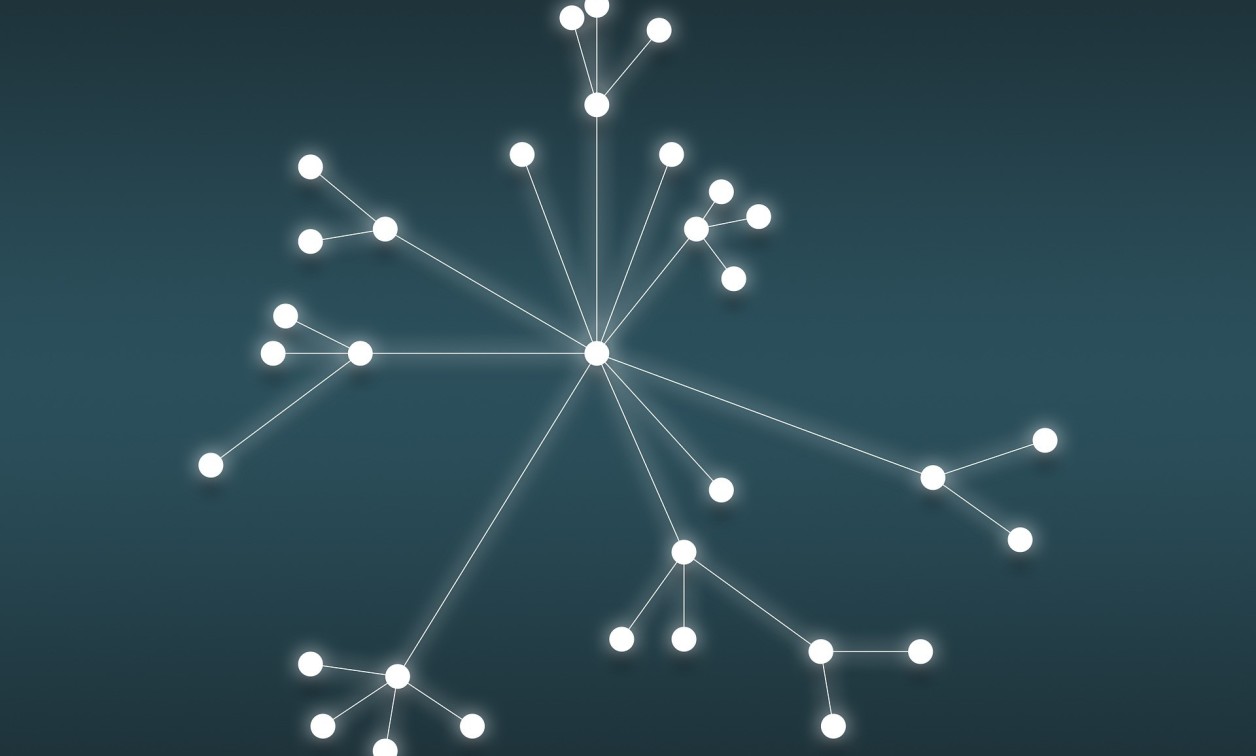
The Internet of Things (IoT), combined with the medical industry?s stringent semiconductor standards, continues to fuel the optical sensor?s significance as the baseline building block to a solution.
The Internet of Things (IoT), combined with the medical industry’s stringent semiconductor standards, continues to fuel the optical sensor’s significance as the baseline building block to a comprehensive solution. At the component level, medical devices and solutions must deliver higher performance and reliability than many other highly engineered systems in other sectors. Already complex and mission-critical, medical applications also face a diverse range of performance scenarios, whether it be a patient’s home, on an emergency vehicle, in a surgical theater, in remote or rugged geographic regions, or perhaps nonstop at a hectic metropolitan hospital.
Since each application is unique, integrating commercial off-the-shelf (COTS) sensor components does not often produce the desired outcome resulting in false readings or inconsistent results. Unacceptable in patient diagnosis and care. Designing the optimum sensor solution with the proper sensitivity range, opto-electrical performance and footprint becomes vital to ensuring precise, steady, and reliable performance. Fine-tuned with compatible LEDs, sensors, and housings, these custom optical sensor solutions offer factory matched testing and configuration to produce an efficient turn-key solution. Adding cables, connectors, passive circuit components, and custom PCBs complements and enhances the flexibility and reliability of the solution. Meeting all these technical challenges, while keeping application performance top of mind, is no easy feat.
Think of Optical Sensors as Building Blocks
Options for creating an optimized sensor solution are quite broad. They range from simply procuring paired discrete COTS emitter and sensor components to higher-level, custom assemblies.
Discrete Components, Diverse Options
The discrete sensor is the most basic element of the sensor solution. Even so, thoughtful consideration of accompanying components is imperative. Ultimately, sensor selection depends on specific application needs, as well as performance requirements such as wavelength, sensitivity, device footprint, and more. A discrete emitter is also typically part of the design. Emitter and sensor pairing is impacted by wavelength, power levels, and sensitivity to mechanical alignment.
Housing Influences Overall Performance
The sensor solution housing (or packaging) is the next phase in the design process, with application requirements driving a range of optical and mechanical housing options. Designers must be mindful of the mechanical stack-up tolerances inherent in each design, along with considerations such as spacing between the sensor and emitter, aperture size which defines the sensor resolution, through-hole vs. surface mount, and mounting bracket. Development of the customized optical sensor solution design must accommodate a spectrum of design choices and performance demands, ranging from variability in mounting location and detection distance, to types of media detected and environmental conditions.
Adding Value with Pre-Attached Wiring and Connectors
Optical sensors are often mounted remotely from the system’s primary printed circuit board (PCB) or microcontroller, so proper connectivity is critical for input power and communications. In these instances, wire length and connector types are important considerations. Procuring custom assemblies with pre-attached wiring and connectors advances plug-and-play compatibility. This simplifies the final product assembly process, reducing costs through improved manufacturing efficiencies and accelerating time-to-market.
Applications May Require Higher-Level Assemblies
Medical applications may have optical sensor requirements that go beyond simple detector and emitter design methods. Multiple sensors and/or emitters, other passive and active components (such as a voltage regulator), or even other mechanical components may involve placement on a common PCB. Supplementary wiring and connectors, or perhaps a common substrate with multiple discrete die components, would be necessary. Higher-level assemblies can take on many different forms, influenced by application requirements for functionality, performance, and size.
With an estimated 30 billion IoT connected devices installed worldwide, finding an off-the-shelf solution for a specific optical sensor application is beyond challenging. It requires optical, electrical, and mechanical engineering expertise to design a solution that performs consistently and reliably over time and across myriad operating conditions. In this landscape, the need for customized optoelectronic sensor solutions is not only a reality, but a necessity due to the complexities of integrating compatible light emitters and sensors, managing the trade-offs of optical power and sensitivity, and balancing stack-up tolerances and overall costs. Reliable, customized performance—even in low-volume, high-mix applications—adds competitive value and ROI in a market characterized by growth and a global appetite for innovation in connected health applications.
About the Author
Authored by Walter Brooks, Global Product Manager-Optoelectronics, TT Electronics
Connect with Walter at [email protected] or LinkedIn.