Time of Flight System for Distance Measurement and Object Detection
April 26, 2021
Story
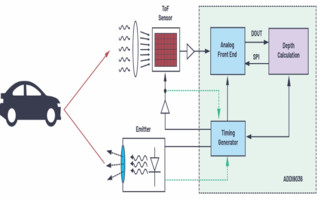
Distance measurement and object detection play significant roles in numerous areas, whether it be in factory automation, robotics applications, or logistics.
Especially in the context of safety, detection and response to objects or people at specific distances are required. For example, a robot arm may need to stop immediately once a worker enters its danger zone.
Time of flight (ToF) is becoming increasingly important for this purpose. With ToF technology, light is emitted from a modulated source, such as a laser, and the light beams reflected off one or more objects are then captured by a sensor or camera. The distance can thereby be determined by means of the time delay ∆t between when the light is emitted and when the reflected light is received. The time delay is proportional to twice the distance between the camera and the object (round trip). Therefore, the distance can be estimated as the depth d = (c × Δt)/2, where c is the speed of light. A ToF camera thus outputs 2D data as well as the required depth information.
ToF allows the entire image to be recorded at once. There is no need for line-by-line scanning or for relative motion between the sensor and the observed objects. ToF is often classified as LIDAR (light detection and ranging), but it is a flash LIDAR-based approach, rather than a scanning LIDAR.
There are basically two different ways to measure the time of flight of the light pulse with ToF: pulsed operation, which is based on charge coupled device (CCD) technology, and continuous wave (CW) operation.
Whereas the elapsed time between emission and reception of the light pulse is measured in pulsed mode, the phase shift between the emitted and received modulated light pulses is determined in CW mode. Both modes of operation have advantages and disadvantages. Pulsed mode is more robust to ambient light, and therefore more conductive to outdoor applications because this technology often relies on high energy light pulses emitted in very short bursts during a short integration window. Whereas CW mode may be easier to implement because the light source does not have to be extremely short, with fast rising/falling edges. However, if precision requirements become more stringent, higher frequency modulation signals will become necessary and may be difficult to implement.
The existing pixel sizes result in high chip resolutions, which enable not just distance measurements but also object and gesture recognition. The distances to be measured range from a few cm (<10 cm) to several meters (<15 m).
Unfortunately, not all objects can be detected to the same degree. The condition, the reflectance, and the speed of the object affect the measurement result.
Figure 1. Time of flight measurement principle.
Figure 2. Block diagram of a ToF system.
The measurement result can also be falsified by environmental factors such as fog or strong sunlight. Ambient light suppression helps with the latter.
Semiconductor manufacturers such as Analog Devices, Inc. (ADI) offer complete 3D ToF systems to support the rapid implementation of 3D ToF solutions. They integrate, among other things, data processing, laser driver, power management, and software/ firmware into one unit for the control electronics. Additional components are an emitter that emits the frequency-modulated optical signal and a detector that registers the reflected signal. A block diagram is shown in Figure 2.
Components such as an analog front end (AFE) with integrated depth calculation are a great help to anyone who wants to build such a system. Among others, the ADDI9036 provides this function. It is a complete CCD ToF signal processor with an integrated laser diode driver, a 12-bit ADC, and a high precision clock generator that generates the timing for both the CCD and the laser. The ADDI9036 is responsible for processing the raw image data from a VGA CCD sensor to yield depth/pixel data.
ADI also works with design partners, with whom we can jointly offer finished modules and development platforms. These evaluation systems can be used for developing customer-specific algorithms. The finished modules and platforms help accelerate development, which is especially important in time-critical business areas as are found in industry and automotive engineering.
References
3D Imaging with ADI Time of Flight Technology. Analog Devices, Inc., 2020.