Embedded form factors: Shrink to fit
April 01, 2011
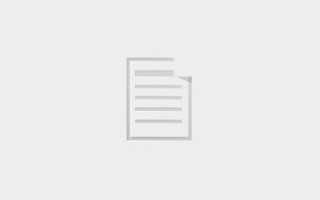
Warren introduces the emergence of smaller form factors in the embedded industry and gives a brief overview of the latest installment of Embedded Comp...
As the embedded industry adjusts to soaring data rates and the latest highly integrated silicon, designers are devising techniques to pack it all into smaller form factor devices that emphasize performance and reliability while reducing power and cooling requirements. Smaller form factors are now achievable because of fundamental changes in the architecture and design of embedded devices and systems. The latest silicon technology is capable of integrating multiple processors, graphics elements, and I/O interfaces onto a single-chip device thereby reducing component count and saving enormous board area. High-speed data rates have also encouraged designers to transition from parallel bus structures to serial switched fabric technology with the added benefit of reduced real estate. Product developers have also found new techniques for power delivery, cooling, and packaging that minimize the overall system size.
In this issue of Embedded Computing Design, we cover the latest technologies that designers can employ to create smaller physical designs along with hardware and software techniques that will be helpful in a tight package environment. One technology area getting a lot of attention lately is the new generation of multicore processors that are now available for long life cycle embedded projects. In the “Embedded moves to multicore” article in the Silicon section of this issue, I outline the performance improvements and power savings these new devices offer. By combining an integral graphics processor, one or more CPU cores, dedicated signal processing elements, and extended instructions onto a single die, silicon manufacturers offer the tools to make dramatic reductions in embedded system size. These new processors also offer new techniques to trade power savings for performance by dynamically adjusting the CPU clock frequencies for short periods to handle heavy workloads.
As these new small form factor devices propagate into multiple industries, the communications load will most likely be shared with the available cellular network. Jeff Sharpe of RadiSys takes a look ahead to the security issues facing mobile users and operators as they transition to high speed, all-IP networks such as Long Term Evolution (LTE). In “Securing the transition to LTE,” Jeff reveals potential security threats and off-the-shelf defenses such as gateways that mobile operators can employ to ensure safe communications in all-IP networks.
24/7 patient monitoring
Although small-sized embedded systems are appearing in many applications, the healthcare industry is a prime market as designers create portable versions of measurement devices that can be taken home to monitor vital parameters on a 24-hour basis. This diversity in deployment sparked Stephen Olsen of Mentor Graphics to take a look at the potential risks and patient safety associated with embedded software installed on multiple devices. In “Minimizing risk: embedded software and today’s medical devices,” Stephen leads designers through the embedded operating system selection process and outlines the software options available with multicore processors.
As designers pack more and more capabilities into embedded system software, customers are understandably asking for devices with reduced or variable functionality to reduce costs. The same hardware may serve multiple functions by managing software privileges on a device basis. In this issue’s Software section, Vikram Koka of Flexera Software describes a case study where Flexera customers were able to selectively enable and simultaneously protect intellectual property in remote embedded devices – an approach that reduced consumer costs and the need to manufacture multiple variations of the same product.
A safe and speedy approach to implementing a small form factor embedded system is to incorporate a Commercial-Off-The-Shelf (COTS) module that has been pre-engineered to take advantage of the latest performance-boosting and power-saving technologies. In his article on Error Checking and Correcting (ECC) support for safety-critical systems, Franz Fischer of congatec demonstrates the advantages of the Computer-On-Module (COM) form factor for embedded designs in server, medical, and aeronautic systems. You can also explore a wide range of small form factor modules in our sister publication PC/104 and Small Form Factors.
As embedded designers move to the next generation of higher-performance processors and extreme data rates, local data links are extremely important for communications with plug-in peripherals. The most popular emerging standard data link is the USB 3.0 specification, which features a SuperSpeed data transfer rate of nearly 5 GBps, yet it must be backward compatible to much lower speed predecessors. Alexander Glas of Infineon Technologies investigates the layout considerations and ESD protection challenges that USB 3.0 hardware developers must face to meet the rigorous technical specifications of this ultra fast data link.
Your thinking on shrinking (and other matters)
The industry’s continued pressure to reduce the size of industrial, medical, consumer, and other space-critical applications has sparked this new wave of extremely small embedded computing platforms. Although they may be small in size, these tiny embedded devices create the same if not larger design challenges. Our task will be to track these shrinking systems to keep you up to date with components and techniques that you can use in your next small form factor design. You can help keep us on track by giving your feedback on the articles that we deliver and offering your suggestions for improvement. If you have an idea for a technical article that would be of interest to our community, please do not hesitate to send me a short article abstract.
Warren Webb, Editorial Director wwebb@opensystemsmedia.com