Knowing when a power module is the right choice
December 10, 2014
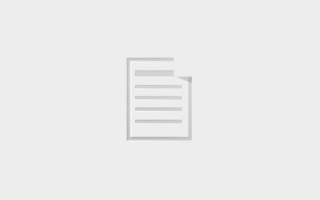
Discrete, power module, or combo? Well, it depends. If you're like me, you often find yourself faced with an incredibly tight project deadline. For ex...
Discrete, power module, or combo? Well, it depends.
If you’re like me, you often find yourself faced with an incredibly tight project deadline. For example, your manager has just tasked you with designing the power supply for a new telecom system. The design starts with a proof of concept implemented on an FPGA, and now a power supply must be created. An isolated power brick provides the 12 V source that’s powering an advanced ASIC, microcontroller, FPGA, and an assortment of other components. As always, these components consume practically all of the board’s real estate, and the laws of physics are challenged to provide adequate power, stability, thermals, low noise, and reliability. And you have been given only ONE week to create this power supply (sigh). Let the fun begin!
With the power hungry current requirements of the ASIC, MCU, and FPGA, you can either use a discrete-based power supply, a combination of discrete and integrated, or a module-based solution. The trade-offs between costs, design effort, and performance are the conditions that must be considered when your solution specs and form factor are fixed. However, when the FPGA and microcode options are still unknown and can change up until the last minute, time becomes the critical factor, and unforeseen development delays can be expected.
When you think about all of the items to consider when using discrete components to design your power supply, you quickly realize the value power modules can provide. With the discrete approach, picking the right combination of PWM controller, FETs, inductor, compensation scheme, and other support components quickly adds to your design cycle. And the time required to layout the board properly, along with the ongoing component procurement cost and time, are all critical reasons why power modules offer significant benefits for your power supply solution.
Due to system design requirements, lack of board space, and the conceptual nature of your design, you determine that the project lends itself to a module-based solution. Power modules provide a fully integrated DC/DC regulator in one package. This means that the controller, FETs, inductor, and compensation circuitry are all housed in one package. Modules can be analog, analog with a digital wrapper, or fully digital.
Say you decide to go with the ISL8270M digital DC/DC power supply module. The 25 A of continuous output current can be delivered without the need for airflow or a heat sink. The thermally enhanced high-density array (HDA) module can dissipate heat directly into the PCB. The module’s digital control responds to a transient load within a single switching cycle, and without needing compensation. It also minimizes output capacitance to increase the design’s density. This control keeps the design stable regardless of temperature, or output capacitance and loading.
Pin-strap modes allow the pre-programmed configurations to be quickly changed. With this power module, a design tool graphical user interface (GUI) called PowerNavigator is used to simplify setup and configuration. And the tool makes it easy to change features and functions of your digital power supply design without writing any code, ensuring the design gets completed before that one week deadline is up.
Proof of concept designs are always a challenge for power designers and not recommended for the faint of heart. Never-ending roadblocks arise when changes in the system power occur, such as voltage changes due to error and performance improvements, or current changes due to miscalculations and constant tweaking of the FPGA and microcontroller. To a power designer, these changes mean further density and thermal concerns but worst of all, it means the dreaded recalculation of the compensation network. The digital power module’s ChargeMode feature lets you get rid of your design sheets, slide-rule, fancy calculator, and forgo your smartphone’s quick dial to tech support.
Felix Martinez is an Applications Engineering Manager for Intersil Corp. He manages the Central Applications team responsible for responding to customer inquiries, as well as developing design tools and collateral. Felix received his BSEE from the University of Miami.