LEMs and OEMs: Different Set-ups, different scopes
December 26, 2023
Blog
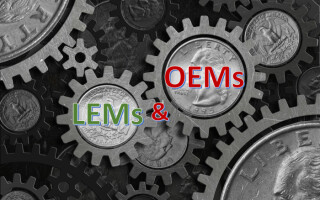
A look at the difference between OEMs and LEMs–and why LEMs are so important for OEMs
Original Equipment Manufacturer (OEM) and Legacy Equipment Manufacturer (LEM) are two very similar terms for similar types of companies that perform vastly different roles in supply chain and manufacturing. A common problem that we see among embedded computing OEMs is that they attempt to perform the sustainment services that LEMs offer, but eventually end up draining valuable resources that could have been better used to develop new products. This is always out of a commitment to customers, attempting to support equipment and boards with long lifecycles. LEMs and OEMs, while having similar departments, are not set up to perform the same job. Both types of companies work in very different niches of manufacturing.
LEMs saw the need for sustainment, which is why they centered their companies around supporting OEM products, so that the OEM could focus on making new products and supporting technological developments. Sustainment is a complex and convoluted undertaking that does not fit into the OEM standardized process. An LEM is a specialized manufacturer of embedded boards that supports and services the products of embedded computing OEMs after the OEMs decide to issue EOL notices.
Because LEMs have strong manufacturing, engineering, and procurement capabilities, it’s not uncommon for them to be confused with other types of electronics companies, from contract manufacturers, to engineering services providers, and even distributors. But those types of companies are as different from LEMs as they are from each other.
OEMs vs. LEMs–different setups, different scopes
While OEMs and LEMs do perform similar operations – both are equipment manufacturers, outfitted with engineering, manufacturing, and production departments – these two types of businesses are set up very differently.
OEMs are started and built on the foundation of making profits on new and active products. That means that their resources and processes are catered towards supporting new product development and current product support.
LEMs are set up to profit by manufacturing and supporting legacy products, equipment that has been EOL’d, or has a long lifecycle to sustain that goes beyond what the OEM prefers to provide. Both types of companies have the same departments with relatively similar scopes, but the products on which they focus have very different needs.
Consider the difference between OEMs’ and LEMs’ engineering departments. While they both function similarly within their respective companies, they must solve very different types of engineering problems.
An OEM engineering team’s purpose is to quickly bring to market board-level features and functions that capture the “prime cut” of the value in the marketplace. Success is measured by both design-wins for multi-year programs, as well as the high-rate follow-on manufacturing.
To be successful, OEM engineers must be current in leading edge embedded computing design theory and interoperability, contemporary components, tools, standards, and manufacturability techniques.
An LEM engineering team’s purpose is to sustain the product with minimal changes so that it remains form-fit-functionally identical to its original design and be reliably manufactured for as long as they are needed. Success is measured by quickly resolving and preventing electronics obsolescence issues - throughout the remaining years of low-rate manufacturing that occurs later in a product’s lifecycle.
To be successful, LEM engineers must not only be well versed in leading edge sustainment techniques, but also in legacy electronics architectures, standards, tools, and parts from when the designs were originally introduced, typically 10 or more years ago.
Unsurprisingly, the ‘prime cut” of the marketplace value that OEMs target means there is a much greater availability of design engineering capacity - making it more difficult to maintain a suitably sized sustaining engineering capability.
Increased overhead from process exceptions
Sustainment projects are messy. This has always been the case.
Sustainment activities don’t fit into typical, standardized processes and almost always require a great deal of time and effort to successfully execute.
OEMs are set up for process–new product development to volume production to sales; sustaining production until the next project begins, then slowly phasing the old products out of their process to make room for new, improved technologies. To remain competitive, OEMs need clear and standardized processes that allow them to remain efficient and productive.
When OEMs try to provide the services that an LEM offers, one of the first major issues they run into is what they’re trying to do doesn’t match with their process.
Nearly everything to do with legacy sustainment creates exceptions to the OEM’s standard procedures and process and can’t be automatically handled within the department. These exceptions require special oversight by the management in the department. The moment that management stops overseeing sustainment activities that can’t be automatically handled, the work typically gets snagged until they can get back to it.
LEMs, on the other hand, are organized to flexibly respond to the needs of Sustainment projects. Their process accounts for changing situations, new information, and other unique circumstances. Sustainment of legacy electronics always presents some new, unique challenge that requires very specific needs. LEMs have the flexibility, capabilities, and the dedicated management to handle these challenges.
There is no way to standardize sustainment. Sustainment requires collaboration, flexibility, and dedication in an ever-changing environment.
The opportunity cost of time
Many OEM leadership teams view engineering capacity as infinite, because salaried engineering payroll is largely fixed. At the same time, OEM leadership teams are engaged in a chronic struggle to hold and accelerate new-product-introduction (NPI) timelines. Legacy work undermines OEMs’ objective to develop new products, whether or not an OEM is set up to measure it.
The best way to view the legacy drain on resources is through time, mainly, and what these OEM personnel are not doing while they’re attempting to sort through a sustainment project. Although it is hard to calculate how much longer it took people to finish more strategic activities related to core high-rate products, everyone agrees they want high-ROI work done faster.
While the OEM may indeed be able to eventually provide sustainment for a product, this will ultimately take resources away from their usual business: materials, labor, time, and costs. This leads to longer lead times on profitable products, delays, and other issues that ultimately make the OEM less competitive.
The more products that the OEM tries to simultaneously sustain, the more these problems accumulate and grow. That’s why LEMs are so important– they work with OEMs to provide the sustainment for legacy equipment that OEMs want to give their customers...without the distraction. This partnership releases more resources for more predictable NPI.
LEMs allow OEMs to provide their customers with legacy sustainment solutions without having to set aside valuable resources that are necessary for new product development and other strategic priorities.