Heavy Mobile Equipment: Transforming Industries
May 02, 2022
Story
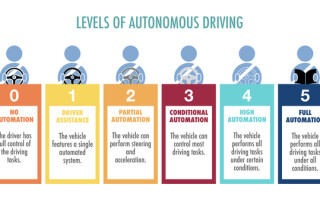
How construction, agriculture, and mining are leveraging AI, deep learning, and more for greater efficiency, safety, and overall performance.
Figure 1. Early telematics applications are characterized by disparate devices that do not communicate, require different power supplies, and operate to different levels of security. Today’s advanced telematics collect multiple types of data (video, time usage, maintenance alerts, and more) and use it to drive outcomes that are computed at the edge. Data analytics can then be applied to enhance equipment performance, safety and maintenance, or to gain more precise insights into operating environments.
Increasingly powerful and intelligent onboard computers are emerging to meet the need for smarter heavy mobile equipment (HME). Transforming the construction, agriculture, and mining industries with greater automation means that these next-generation connected vehicles can sense and analyze their current environment and operating conditions, then execute improvements in real-time.
Increased demands for agricultural production, construction, and raw materials mean that fleet owners and operators are seeking ways to increase productivity and yield without compromising on safety and cost. The arrival of new, customizable platform architecture addresses today’s challenges and future needs for deep learning, in-vehicle AI, and high-performance embedded computing. The latest secure, innovative compute platforms are powered by Intel® technology – and poised to allow fleet leaders to benefit from accelerated time-to-market, reduced total cost of ownership, and enhanced vehicle safety, device security, and performance. Operators and manufacturers can now weigh in on the requirements for next-gen smart, connected, and autonomous vehicles by examining the approach taken by heavy vehicle systems.
Where Necessity Meets Innovation
Ideally, end-users and fleet operators must think beyond the immediate benefits of driver-assisted and Level 4 or 5 self-driving vehicles. Application of automation can more safely run HME equipment, increase production, minimize waste, and organize workloads. In-vehicle compute systems harness the full potential of real-time actionable data, collecting sensor data to monitor video and usage time for preventive maintenance. Here, the critical difference between basic and advanced telematics is notable. Early telematics applications are characterized by disparate devices that do not communicate, require different power supplies, and operate to different levels of security. In contrast, today’s more advanced telematics collect multiple types of data (video, time usage, maintenance alerts, and more) and use it to drive outcomes that are computed at the edge. Data analytics can then be applied to enhance equipment performance, safety and maintenance, or to gain more precise insights into operating environments.
This more holistic approach to collecting and leveraging data is becoming an intrinsic part of automation. For the HME sector, it is foundational to digital transformation strategies.
Figure 2. Autonomous driving is defined by five levels, starting with level zero (no automation and a human driver in control) and increasing up to level five featuring fully autonomous performance. Level one offers only assistive tools such as cameras and adaptive cruise control, while level two partially automates steering and acceleration for driver comfort and safety. The HME sector capitalizes primarily on level three and up, ranging from conditional and high automation with a driver present to full automation with no human driver needed on board.
Comprehensive and efficient HME task automation is key to the pursuit of more accurate decision-making – by humans and machines. Heavy mobile equipment – from excavators, graders, diggers, dozers, and tractors to combine harvesters, backhoe loaders, and drilling rigs – is reaping the benefits of these advances in intelligent, connected, and data-driven autonomous operations.
Enabled by the latest communications and computing technologies, applications connect and automate heavy vehicles and equipment on farms, construction sites, and mine works. It’s a shift that aims to realize enhanced safety, productivity, and efficiencies while also reducing infrastructure needs. Onboard, edge computing capabilities empower heavy vehicle manufacturers, operators, and users to access the information they need when they need it, leading to better decision-making on the spot or in the future. The power of analytics is that the information can be used now or later for planning purposes, adding value by extending vehicle lifetimes and reducing operational costs.
It is also getting easier to adapt heavy mobile equipment to new tasks. The availability of "aftermarket" intelligent and connected solutions for existing machinery offers a low-risk approach to automation. For example, turnkey and plug-and-play kits now exist to convert standard trucks, excavators, and dozers into semi- and even wholly-automated vehicles. This is an industry-wide win, because the cost, natural life, and variation inherent to HME fleets mean owners can invest in systems that can be used for many years and later re-installed in other vehicles.
Figure 3. An optimized system can be illustrated by Kontron’s EvoTRAC™ – a validated, application-ready platform with built-in capabilities for in-vehicle AI, deep learning, and high performance embedded computing (HPEC). Deployable as a rugged, ready-made solution for applications onboard heavy-duty mobile machinery, the platform features an Intel® Xeon® D processor, Intel® Dual 10GbE network adapter card, and multiple GPU options for machine learning and AI workloads.
AI, autonomous, and edge-based HME systems unlock the true potential of the edge, but in order to work seamlessly, they must possess some key capabilities. Due to space limitations, they must be highly compact. They require ruggedization to withstand rough handling, dust and water ingress, vibration, and often extreme operating temperatures. Data security and user safety features are necessary. Total cost of ownership, long-term product availability, and the utilization of industry-standard components are also important considerations in addressing ROI and the specific requirements of different machines across the same fleet. Finally, the ability to take advantage of future technological advancements like upgraded processors and accelerators is possible.
Heavy Duty Applications; Heavy Duty Requirements
For system developers, it’s a new and evolving landscape where smart, rugged designs provide a competitive edge and keep HME poised for what’s next. And what’s next is big… According to IMARC Group, the value of the global Automated Construction Market is expected to reach USD 186.6 billion by 2024, registering a CAGR of 15.5% from 2019-2024. This is indicative of the enormous value autonomous machines have in accelerating construction projects such as digging, grading, pushing, compacting, trenching, truck loading, and demolition. Automation allows humans to be readily available to undertake more complex tasks – a significant advantage given the mounting shortages in skilled and available labor.
This has led to increased demand for incorporating robotics and AI technology into heavy machines to make them more efficient in reducing waste and making sure the right vehicle is assigned to the right job. For example, a vehicle’s control systems should ideally govern traction based on data captured and processed in real-time from multiple onboard sensors. Geofencing solutions prevent machines from straying beyond specific boundaries on the construction site or even onboard LiDAR and cameras can identify obstacles to avoid potential collisions.
In agriculture, robotics and AI are helping farmers control costs while improving output. Artificial intelligence in the agriculture market is projected to rise from an estimated 1.0 billion USD in 2020 to 4.0 billion USD by 2026, with a CAGR of 25.5% between 2020 and 2026. This growth is being driven by the increasing implementation of data generated through sensors and aerial images. Farmers are boosting crop productivity thanks to deep-learning technology and government support for the adoption of modern agricultural techniques.
Autonomous tractors equipped with GPS and sensors can safely operate non-stop in any condition – fog, dust, and extreme temperatures. Performing tasks such as plowing and spraying while collecting data on soil conditions offers major advantages to properly maintaining planted crops. Some self-driving tractors also provide guidance on fertilizer application, maneuvering around and away from growing plants.
Applications that administer pesticides, fertilizer, and fungicides can help farmers reduce weed infestations among their crops, but it is AI and on-premise ruggedized in-vehicle computing that is essential to effectiveness. AI combined with 5G will be a huge step forward in quickly determining which plants are weeds versus those that are not, along with focused and measured application of pesticides to minimize environmental concerns.
Mining companies have been ahead of the curve in terms of deploying intelligent, connected equipment – with early recognition of its capacity to mitigate and avoid industry hazards. This is supported by Mordor market report which expects the automated mining equipment market to register a CAGR of 35.38% over the 2021 to 2026 forecast period.
The demand for certain ores used in batteries (for devices and vehicles) requires mining vehicles to reach depths too dangerous for humans. Autonomous mine vehicles allow the safe extraction of ores that would otherwise be inaccessible, raising yields and avoiding dangerous attempts by a human workforce. Connected vehicles and drill rigs can work 24/7, improving not only worker safety but also overall productivity and yield levels. Automated fleet tracking powers the proximity detection and remote machine operation that optimize haulage truck movement throughout the mine – as well as the ability to receive instructions from remote-based operators, safely above ground. Intelligent longhole drill rigs with onboard sensors are also frequently deployed as they enable more precise location, depth, and angle at the drill point. With better accuracy, mining operations can recognize a significantly improved blasting outcome.
Big Data + Big Equipment = Big Demands
IoT devices, sensors, and camera/video produce enormous amounts of data from driver operated and fully autonomous vehicles, requiring hundreds of signals to be processed in fractions of a second. Many of these scenarios occur close to where the data originates, onboard heavy mobile equipment in the field.
To address these challenges, embedded solutions must offer connectivity and configurability along with high compute processing, graphics, storage, and bandwidth. The rapid adoption of in-vehicle / on-premise AI-enabled machine learning and deep learning applications has played a role in setting designer expectations. The arrival of high bandwidth 5G mobile communications is sure to increase those expectations.
Highly accurate and actionable information allows operators, equipment manufacturers, and fleet providers unprecedented access to ‘live’ machine performance data for predictive maintenance programs. The ability to perform condition monitoring, diagnostics, and some repairs remotely using real-time data aids in pre-empting or minimizing potential faults and performing critical repairs or scheduling non-critical ones. Fleet operators can see if an idling vehicle is merely on a break or has actually broken down. Service hours and machine productivity can be tracked, measured, and recorded. This translates not only into fewer time-consuming on-site service visits (and therefore cost savings), but it also ensures increased customer satisfaction for service organizations through enhanced machine reliability and reduced overall TCO.
Industries reliant on HME are driving global advancements in automation. New intelligent and autonomous solutions are paving the way, allowing humans and machines to work in tandem to improve operational efficiency and productivity.