College engineers build the cars of the future
August 30, 2016
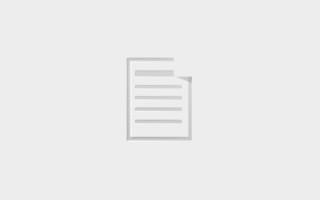
It's not yet 11 a.m. on a Saturday and the shop floor is already humming with activity. Several engineers are hard at work under the hood of a Chevrol...
It’s not yet 11 a.m. on a Saturday and the shop floor is already humming with activity. Several engineers are hard at work under the hood of a Chevrolet Camaro, which they are fitting with a belted alternator starter in the place of a standard alternator. Other team members double-check the components against a simulated vehicle they’ve designed on computers with the help of an engineering software platform. Still others check schedules and equipment orders to keep the team on track. Their goal is to make the Camaro leaner and greener (by installing a plug-in hybrid powertrain) without losing its classic muscle (they’re shooting for 0 to 60 in 5.6 seconds).
Believe it or not, this team is not working at a top automotive manufacturer, although many of them will end up there down the road. The busy shop floor is located at the Center for Automotive Research at Ohio State University (OSU), and the engineers are students and members of the OSU EcoCAR 3 team. After spending long hours in the shop, they’ll go to classes, hang out with friends, and participate in other extracurricular activities.
“Our team is unique in that we have a high percentage of students who are involved on a purely extra-curricular basis,” said Shawn Midlam-Mohler, Assistant Professor of Mechanical and Aerospace Engineering at OSU, and lead advisor to the EcoCAR 3 team. “They’re not getting course credits; they’re showing up because they have passion for this activity.”
While the team won’t be given grades or credit for their work on the Camaro, this exercise in project-based learning will give them the chance to hone in on leadership and practical engineering skills. The hands-on experience of working on a Camaro better prepares students for their future careers by offering the opportunity of using industry-standard tools like MATLAB and Simulink.
A new kind of engineer
It’s no secret that the U.S. needs more college graduates passionate about working in science, technology, engineering, and mathematics (STEM). The U.S. Bureau of Labor Statistics estimates that 15 of the 20 fastest growing fields in the next 10 years will require significant math and science preparation. This need is felt strongly within the automotive industry where engineers must develop vehicles that meet emission protocols and harness sustainable energy, while still attaining consumer expectations for safety and functionality.
EcoCAR 3 is the latest iteration of the U.S. Department of Energy’s Advanced Vehicle Technology Competitions (AVTCs), a series of student competitions launched in 1988 to inspire and challenge the next generation of automotive engineers. Managed by Argonne National Laboratory, the competitions are a collaborative effort between academia, eager to train the engineers that will build solutions for a more sustainable future, and automotive companies, seeking next-generation engineering talent. Industry partners provide the teams with access to the industry-standard hardware and software as well as the technical support needed to build truly innovative vehicles.
In 28 years of competition, the premise of the AVTCs has remained consistent: teams of undergraduate and graduate students work together to re-engineer a donated vehicle to improve energy efficiency and to meet emissions standards, while maintaining the features that make it attractive to the customer. Students get hands-on experience solving complex engineering challenges while learning project management skills. What has changed, however, is the technology available to the teams. In EcoCAR 3, which kicked off in 2014 and will wrap up in 2018, teams from 16 North American universities are overhauling a Chevrolet Camaro.
Rising to the occasion
The teams didn’t receive their Camaros until Year Two of the challenge. Just as in the automotive industry, significant time is spent designing and testing the many options for the car’s architecture until the combination is found that optimizes efficiency, safety, and the team’s performance goals. Year One is where engineering software like MATLAB and Simulink comes in especially handy for teams faced with weeding through thousands of design options for their vehicles. Once a design is approved by competition officials, the OSU team harnesses Simulink’s modelling environment to zoom in on each component and system within the vehicle to tweak performance with greater precision.
When the stock Camaros finally arrived on campus, OSU’s team of 40 students had just three months to integrate their design and be ready to perform in the Year Two competition this past May. As the team’s Hardware-in-the-Loop Lead, Arjun Khanna, a Master’s student in Mechanical Engineering, managed the project of developing a new controls system for the vehicle. Khanna explained that since the team replaced the Camaro’s entire powertrain with components from different manufacturers, one of the biggest challenges was designing a system to line up the many inputs and outputs so the components could “talk to one another.”
“We model everything on the computer, and then convert the controller software into code so we can test it before we try it out in the vehicle,” said Khanna. “MATLAB provides a good backbone interface with other types of simulation tools to help us run tests on the controls system.” MATLAB and Simulink are also used in the building process to test components and their control systems as they are added to the vehicle. The software allows the team to rapidly simulate changes to their initial design and respond to any equipment challenges. By leveraging model-based design, the team doesn’t waste any time or resources making changes to their Camaro.
“The MathWorks model that we’re using is really the glue that’s holding a lot of our design decisions together,” said Midlam-Mohler. The glue must have stuck, as OSU placed first overall at the Year Two competition in Yuma, Arizona, and San Diego, California. Despite stiff competition from the 15 other teams, Midlam-Mohler said that what separates OSU from the pack is “utilizing that expanded set of tools that plug into MathWorks’ core software. MATLAB is the framework holding together all these other tools we use. Our team has exceptional harmony between the engineering tools and the whole design process.”
The road ahead
Since the program launched, more than 16,500 students from 93 educational institutions in North America have tackled revamping a vehicle through AVTCs. The competition not only helps students develop into creative, project-oriented engineers, but serves as a pipeline to move them into jobs at top automotive companies. Through his involvement with EcoCAR 3, Khanna was recruited by General Motors and has accepted a full-time position for the fall as a power and control integration engineer. He is not the first to be actively sought out by a top company. In fact, members of AVTC teams at OSU have 75 percent better placement in the automotive industry than their peers. For team leads or project managers like Khanna, the figure jumps to almost 100 percent.
Midlam-Mohler was a member of the OSU team in FutureTruck, one of the earlier versions of the competition which ran from 1999-2004, and has seen major changes in the AVTC space. The teams in EcoCAR 3 are much more cross-disciplinary, with computer science majors working alongside mechanical engineers and communications majors, and increased partnership between industry and academia has led to more sponsorship and more technical resources for innovation in the competition vehicles.
The role of AVTC sponsorship has also shifted from the simple donation of hardware or software to long-term mentorship programs between companies and AVTC students. In late September, for example, MathWorks will host the Year Three Fall Workshop, inviting teams to Natick, Mass. for a chance to interact directly with competition sponsors, refresh themselves on the competition rules, and have in-depth training on software tools.
For all that the AVTCs have changed over the course of nearly three decades, and all of the different vehicles that have taken a lap around the test track, the goals of the competition have remained the same: foster the next generation of engineers and give them the tools to build the cars of the future.