Let the Autonomous Robot Do the Agriculture Work
February 24, 2023
Sponsored Blog
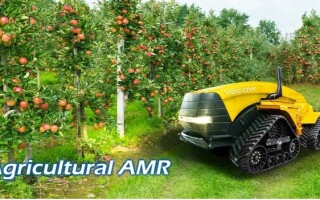
Smart agriculture combines traditional farming with the Internet of Things (IoT), as well as some of the latest technologies including artificial intelligence, robotics, and autonomous drive. That combination has not only provided solutions to often time-consuming and tedious tasks, but is totally changing the way we think about agriculture.
According to a recent United Nations report, the earth’s population is expected to reach 9.7 billion people by the year 2050. Hence, there will be a considerably increased demand for food, which will be transferred to the global farming community. Without innovations like smart agriculture that increase productivity and efficiency, it will be difficult or impossible to meet that demand.
Aside from population growth, we also face a host of issues like soil deterioration, climate change, an advancing carbon footprint, and reduced resources.
AMRs can be a boon to the field of agriculture, handling tasks far more efficiently than humans.
The Components of Smart Agriculture
Smart agriculture equipment takes inputs from various sensors, looking at things like soil composition, the weather, and the condition/position of the people and animals present. These autonomous machines will also perform various tasks related to crop maintenance, including weeding, seeding, applying pesticides and herbicides, harvesting fruits and vegetables, thinning plants, and tilling soil.
Smart robots typically consider the data derived from all the sensors, with the ability to track, monitor, automate, and analyze the farm’s complete operations. This is all managed via software that can be either local to the farm or on a Cloud-based server.
Lots of these technologies will be driven by agriculture autonomous mobile robots (AMRs). In many cases, the agriculture AMR is a lightweight, solar-electric powered robot that uses intelligent perception from an array of sensors to handle a plethora of duties, which could include detection and classification of plants and their characteristics. The system can also contain a robotic arm for autonomous weed cutting.
Agriculture AMRs are constructed with no open or live contacts, connectors, or cables to ensure that moisture, dust, and dirt won’t affect the device in any way. Hence, the agriculture AMR can be exposed to pesticides, fertilizers, and other chemicals that can be harmful to humans.
Agriculture AMRs and Vision
Most farms are laid out in a grid-like structure, so the vision systems deployed by the agriculture AMRs are key to maximizing their AI capabilities. In other words, seeds, fertilizer, chemicals, etc., will be placed exactly where they belong to maximize efficiency and minimize waste.
It’s abundantly important that the agriculture AMRs do not present any danger to humans that may be active on the farm. That’s another area where the sensors come into play.
Agriculture AMRs can also provide a solution to address the workforce shortages taking place in several countries, and while there is a relatively larger up-front deployment cost, it’s generally a one-time investment, with the bulk of the resources going to the agriculture AMRs themselves.
In addition to that (mostly) one-time up-front cost, the agriculture AMRs will require regular maintenance. In most cases, that maintenance would be routine, but there’s always the chance for something irregular to occur. Agriculture AMRs can generally send a signal to the operator when maintenance is needed, including exactly what type of maintenance it is and how it should be performed, thanks to the integrated preventive maintenance routines.
With features like object recognition, ARMs can operate safely in the field, even when humans and/or other objects are present.
Operating Safely and Securely
The agriculture AMRs must communicate with each other and with an operator. The down side to those communications is that there’s always the possibility of a security breach. The agriculture AMRs must be designed with the proper security features in place while maintaining a high level of safety.
One solution that works well makes use of Gigabit multimedia serial link (GMSL) cameras, which are common for this application. The cameras are used for object recognition — for example, to distinguish weeds from grapes, or a fence post and a human.
One example platform is based on the Vecow EAC-2100, which is designed around NVIDIA’s Jetson Xavier NX processor module. The agriculture AMR is built to the IP65 standard, meaning that it is “dust tight" and protected against water projected from a nozzle. It operates in a fanless configuration in temperatures ranging from -20°C to +70°C.
Another key feature is the small size of the EAC-2100. It measures just 150.0 x 106.2 x 62.0 mm. The Vecow platform is designed to withstand shock and vibration that meet U.S. military equipment inspection standard, MIL-STD-810G.
Other features of a Vecow EAC-2100-based agriculture AMR that’s already deployed in the field include four Fakra-Z connectors to link up to the GSML cameras, four GigE LAN connectors, dual CAN interfaces, one DIO port, and a Micro SD socket. It’s accepted input voltage ranges from 9 to 50 VDC.
Smart agriculture is here today and improving and expanding rapidly thanks to advancements from vendors like Vecow.
The Experienced Agriculture AMR Vendor
Vecow now has extensive experience in smart agriculture applications. The company has been working with customers on the latest demands in this space, many of which can be fulfilled by Vecow’s EAC-3000 or newer platforms.
Vecow employs modularized computer boards and I/O that allow for quicker design turn-around times, allowing customers to quickly develop and improve products and ultimately win more opportunities. Finally, Vecow operates with a dedicated and experienced project team that provides trusted support in all technical phases, even after the robot has been deployed.