Top 5 barriers to IIoT adoption and how to overcome them
December 16, 2016
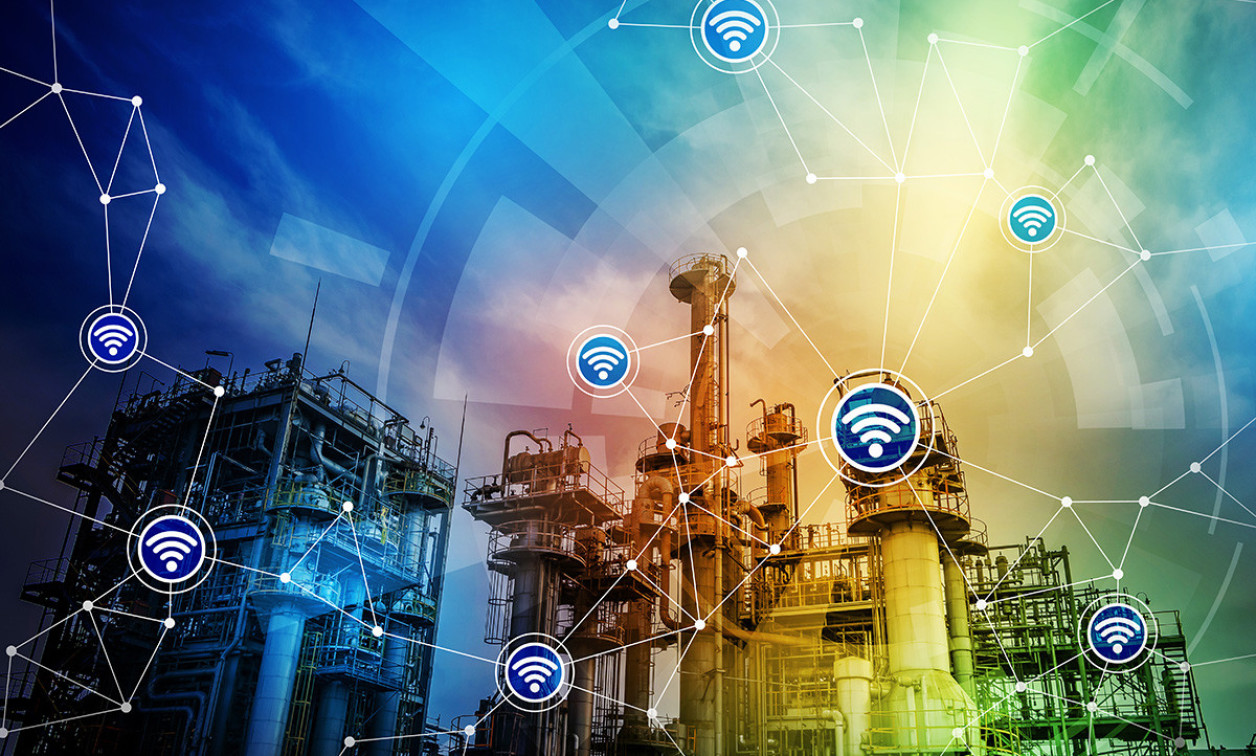
1. Too much media attention on the technology stack or informational technology (IT) Most vendors fit somewhere in the technology stack from things, c...
1. Too much media attention on the technology stack or informational technology (IT)
Most vendors fit somewhere in the technology stack from things, connectivity, platforms, applications, and analytics. For the mid-tier industrial world, it’s hard to decipher the big picture on how and where to start. The Internet of Things (IoT) industry can appear to be expensive and intimidating, and more focused on gadgets rather than creating relevant solutions for particular business verticals. One must understand the pieces and costs, focus on the desired outcome, and peel back the onion one layer at a time. The real value of the Industrial IoT (IIoT) lies not in a gadget, but with the collection of data that will produce actionable information, enabling, for example, predictive maintenance.
2. Conservative technology culture or too much focus on operational technology (OT)
A second major barrier has to do with the expertise and culture of industrial organizations, which focus heavily on operations or OT. Industrial organizations as OT companies are at direct odds philosophically with IT organizations. Whereas IT is defined by constant change and innovation, OT is change- and risk-averse. That’s why it’s not unusual to see industrial automation systems in service for decades at a time with little or no change. In a world where any downtime of production systems can have a devastating impact on revenue, stability is the top priority.
The real value will be the fine balance of domain expertise (OT) with data science (IT) to yield positive outcomes for the organization. While stability and the way things were done in the past served well as experience, organizations must adapt to this digital industrial revolution dubbed Industry 4.0. We are all too familiar with stories of Kodak being a market leader until digital disruption eclipsed the instant photograph with digital photos. Some referred to those who didn’t innovate during those rapidly changing times as being “Kodaked”. One has to jump in and commit through a series of small experiments to learn from these organizational changes. You can mitigate risk by having reasonable expectations in small, coordinated digital test beds to determine the value and ROI.
3. Lack of industrial technologists to lead the IIoT program
While one can commit in theory to responding to the digital world merging with the industrial world, there is the question of who in the company can lead that charge. There needs to be a person or team that can bridge the gap between the IT and OT cultures and ensure competing priorities are met. The program needs a combined IT/OT perspective for the organization, all within the confines of achieving IIoT goals with increasing operational complexity.
There are several certifications in data science, online courses, and conferences nationwide to introduce middle management to these concepts. While new, start building the competency by making learning and education a KPI of the management team. Look to team up with universities and vendors that can help assist with this function and educational need. The quest for knowledge must be an ongoing mandate of the executive team.
4. Viewing ROI through the wrong lens
Industrial technology investments are highly ROI-driven. IIoT should be seen as a process improvement over time that yields significant savings and efficiencies – not as a typical 12-month payback cycle type of investment.
Data should be considered an asset not only for SCADA or monitoring, but as condition monitoring that leads to predictive and preventative maintenance. Sensors that monitor vibration, temperature, and humidity can provide a wealth of new insights on rotating machines and pumps. Measuring and seeing trends from various sensors can help predict failures before they occur, minimizing unplanned and costly downtime. This also improves maintenance schedules as, over time, this becomes more customized your factory setting than maintenance schedules recommended in manual guides. ROI must be looked at holistically, with the bottom line, cost savings, and efficiency improvement considered together.
5. Security concerns
With all the news regarding cyber security, it is easy to worry about potential hacks and problems that occur. One has to systemically address these security issues one by one and realize there are safeguards for sensitive industrial information. Data can be verified and encrypted with a myriad of one-way communications depending on the level of sensitivity. SCADA systems do not need to integrate sensor data and act upon it – they can be separated digitally. In addition, the cloud infrastructure could be networked internally as a private or corporate cloud with no access to outside world. When these security challenges are overcome, the benefits of adopting IIoT technology outweigh the risks.
How to begin
A straightforward and practical approach should be used when embarking on an IIoT project. This should not be viewed as a massive, company-changing effort, but rather a series of small projects or digital test beds that have the potential to increase revenue, improve the bottom line, or boost customer retention. While we all recognize the opportunity for success, realize that not all IoT initiatives will succeed – some say that about half will fail. If you have that in mind, then company expectations about success are reasonable.
A reasonable approach is to pick a few products and services to which adding connected sensors could result in substantial improvement to the organization’s bottom line. Then, identify three more products and services that could possibly lead to additional sources of revenue. Research has shown from a portfolio of six projects, one will be a big success, two will be average hits, and three will fail.
This approach is manageable, and if the pilots are successful, they can be part of the company’s offerings. If they don’t succeed, they can be considered useful learning experiments. This process should be repeated. In addition, one should consider the organizational culture when implementing, ensure buy-in from the top management team, identify digital directors, transform company culture, etc. Even with all necessary systems and processes in place, a strategy can be crushed by old visions of what the company is or aspires to be.