Transforming Semiconductor and Display Manufacturing with Additive Manufacturing and Electrostatic Printing Technology
July 25, 2022
Blog
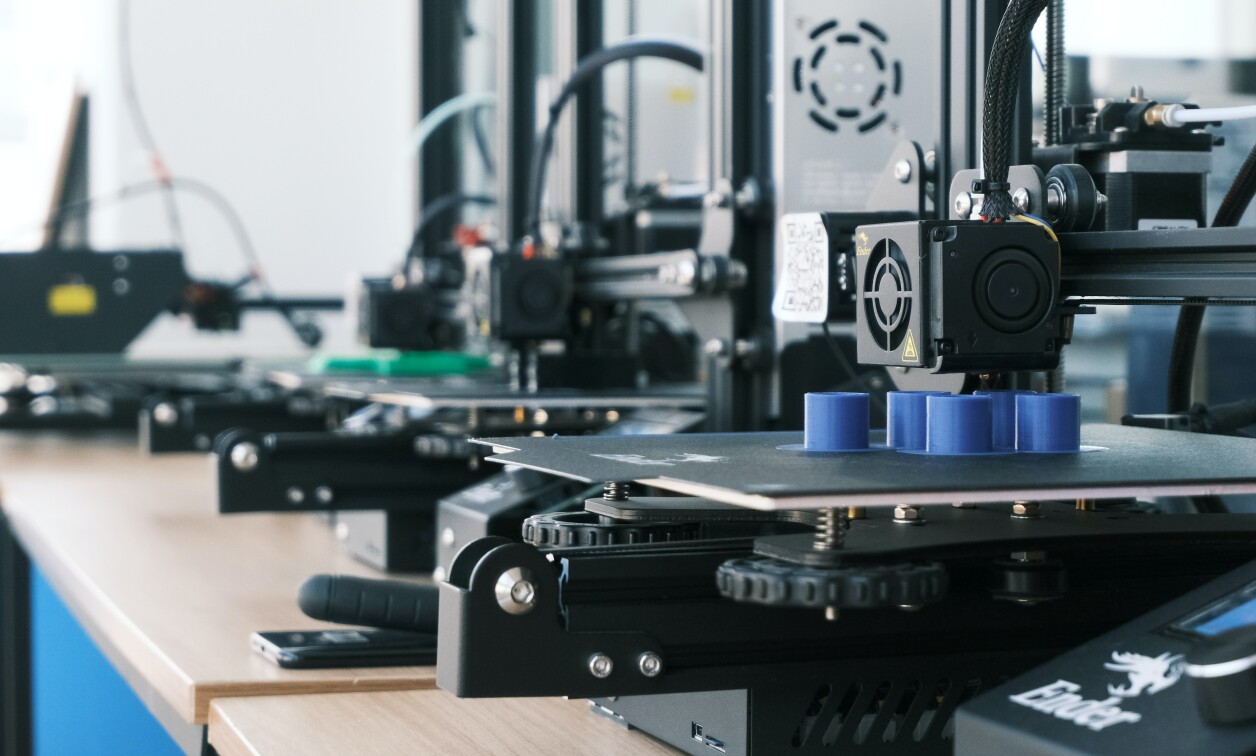
Digital printing technologies have advanced significantly in the last decade and we have seen its use cases successfully expand from graphical into 3D printing of geometrical objects. However, the area these solutions have not been able to address is the functional printing of microelectronic products.
The reason is that these applications require ultra-high resolution and placement accuracy in order to be effective and affordable. Existing technologies such as traditional inkjet printing have not been able to achieve this….until now.
This article will describe the inherent limitations of traditional inkjet printing and discuss how recent advancements in additive manufacturing and electrostatic printing principals are aiming to reinvent micromanufacturing for mass production and speed product invention in an economical and eco-friendly way.
Electrostatic Inkjet Printing Vs Conventional Piezo
Electrostatic inkjet printing is much more powerful than conventional piezo or bubble jet based technology because of the simple physics behind “push and pull.” In electrostatic printing, droplets are not pushed from the inside of fine nozzle channels, but instead are pulled by an electric force from the outside. In contrast, when a conventional printhead creates pushing mechanical force inside the nozzle, most energy is lost due to the viscous flow resistance of the liquid. This not only limits smallest possible nozzle sizes, but also restricts droplets to be of the same size as the nozzle.
The energy required for electrostatic droplet ejection is based on the physical principle of electrohydrodynamics, the fact that basically any liquid is electrically conductive and can be set in motion when exposed to electric fields. This means that the force to create a droplet is generated directly in the liquid. Due to the dynamic equilibrium between liquid movement and electrical force, a liquid meniscus is formed, which concentrates almost all the energy on its tip. Only from this tip droplets are ejected, which are much smaller than the nozzle itself.
Leveraging electrostatic ejection principles, it is possible to achieve simultaneous printing from a large nozzle array, with the following advantages compared to conventional inkjet:
- Ultra-high-resolution printing - 100x higher resolution
- High-speed printing - 10x higher ejection frequency
- Smaller droplets not only for higher precision but also for fast drying
- 3D printing. Aspect ratios >10:1 possible, nanometer layer thickness control
- MEMS printhead customization, dynamically and fully programmable
- Prevention of nozzle clogging by integrated Environmental Control System (ECS)
Broad Material Bandwidth vs.Thin Fluid
Besides enabling up to 100x higher printing resolution, the benefits of electrostatic ejection support a massively increased ink compatibility. With electrostatic printing, the fact that the liquid is both actuator and respondent, allows a dynamic process adjustment to almost any ink. And, since ejection takes place in a volume that is not confined by the nozzle walls, highly viscous inks can be printed more than 100X higher than with conventional printheads.
This ability to print with many types of fluid expands use cases besides typical nanoparticle metal inks into a wide range of materials, such as
- Molecules and salt solutions
- Microparticles and proteins
- Melts, waxes, and epoxies
Through this new process, the expensive treatments of inks to make their rheology compatible with conventional inkjet printheads can be drastically reduced or even become obsolete. While one single nozzle already demonstrates unseen performance for microfabrication, an economic usage only becomes viable by replicating these nozzles 1,000X times in a single chip using a microfabricated MEMS technology. This enables the digital microfabrication of functional elements printed from multiple materials in a resolution invisible to the naked eye. It allows the development of products we have only envisioned. One example is an invisible touchscreen that could be printed as fast and economical as printing an image on a typical office printer today.
Implications for Semiconductor Manufacturing
Transistor and chip-scaling are gradually reaching their economical limit. The next phase of semiconductor innovation to increase device performance and energy efficiency will strongly rely on novel IC packaging techniques, a trend which has become known as “More than Moore”. The opportunities of additive electrostatic printing in this field are very wide, ranging from wafer/chip marking, bumping, via filling, or direct patterning of redistribution layers.
The ability to print on any material, at scale, can improve the speed, accuracy and cost of producing innovative products. The semiconductor industry is an ideal target for additive manufacturing to reduce their complexity, high-cost as well as high-water and energy usage while delivering the high resolution needed.
As the below graphics depicts, electrostatic printing could reduce manufacturing steps of certain semiconductor back-end components 10-fold, while also significantly reducing material, energy, and water usage. With multiple steps – over 20 required for one single layer on a semiconductor device – fabrication can take up to 15 weeks, with 11–13 weeks being the industry average. In addition, a semiconductor fab may use between 2 to 4 million gallons of UPW (ultra-pure water) every day, which is approximately equivalent to the water use of 40 thousand households.
In addition to semiconductor market, there are many other applications for this type of technology.
- Displays - Electrostatic printing is able to solve ongoing issues in the realization of next-generation microLED displays and at the same time is able to greatly simplify the production of current OLED or LCD display technology. For example, the resolution and layer thickness control of this technology allows the printing of quantum dots color filters for high-brightness, full-color micro LED displays in augmented reality glasses for gaming and metaverse applications.
- 3D printing is another area that is quickly gaining ground in many markets due to its flexibility, customizability, and potential towards manufacturing very complex parts. Through the combination of high throughput, sub-micrometer resolution, and very precise layer thickness control down to the single nanometer, electrostatic printing opens new possibilities in micro-optics, where precisely controlled and smooth 3D surfaces are critical. Additionally, multi-material printing enables the fabrication of gradient-index elements with enhanced optical performance.
- And more. As a platform technology, electrostatic MEMS printheads can transform manufacturing in many additional areas such as security printing, diagnostics and life science, and photovoltaics.
The Future of Electrostatic Printing
Leveraging principals of electrostatic printing can enable the production of completely new products and components. This cutting edge new printing technology has the potential to disrupt complex and wasteful manufacturing of existing products and accelerate the ongoing transition towards additive manufacturing. The availability of multi-nozzle printheads which can digitally print the impossible with sub-micrometer precision, on any material and at scale, improving and speeding manufacturing for today and tomorrow’s products.