Choosing a Relay: Go Newer Solid State or Older Electromechanical?
May 06, 2019
Story
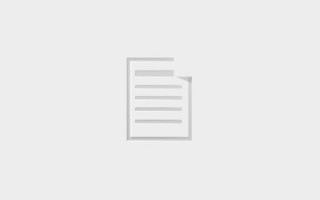
When embedded systems need to contact the outside world to sense strong signals, they often need electrical dilation on the I/O. The question is: Should I use a SSR to do this, or an EMR?
Sooner or later – and it is usually sooner – your embedded system will need to connect its I/O to the outside world. The most common external I/O involves sensing and control of on/off circuits, which can range from “dry circuits” (no or almost zero current flow), to 5-V or 12-V DC signals, to 24 VAC, to 120/240 VAC power lines, and more. Further, due to basic signal incompatibility (your 3-V I/O versus AC line voltage) and user and system safety, you don’t want high voltages in your box or PC board, so you’ll want galvanic isolation, meaning there is no ohmic path between your system and that outside world, Figure 1.
That’s where isolation modules come into the story. For most embedded system applications, these are stand-alone socketed relays that can be easily swapped, changed, or upgraded as needed. The word “relay” actually refers to two distinctly different implementations: the electromechanical relay (EMR) developed in the 1860s (yes, that long ago)! and the solid-state relay (SSR) first introduced in the 1960s. (Note that we are talking here about relays for power or low-frequency signals; there are also relays for RF but those are very different creatures and the criteria by which they are assessed and selected are very different.)
EMRs vs SSRs
The operating principles of both the SSR and EMR are simple yet quite different. In brief, the SSR uses an LED/phototransistor for its isolated coupling, while allowing the signal representing a sensed switch closure or current flow to a load on or off to pass, Figure 2.
The much-older EMR uses the current driven into an electromagnet as its input signal; as the electromagnet is energized, it pulls on an armature, which physically closes a nearby contact or contacts, Figure 3. (For this reason, the EMR is sometimes called a contact or coil relay.)
The obvious question is this: “which one to use in your embedded system’s design?” As with most engineering decisions, the answer is simple: “it depends.” In general, most EEs look to the SSR as a first choice, because SSRs are somewhat easier to interface with low-level electronic signals, have a fast switching time of microseconds (compared to milliseconds for EMRs), and are rated for tens of millions of operating cycles. Many SSRs also have a small indicator LED so the user can tell if it is activated, a handy feature.
On the proverbial “other hand,” EMRs are preferred in some applications even though they have moving parts, which most EEs worry about and which may fear. EMRs can tolerate voltage and current spikes and overloads, and a properly chosen EMR from a reputable vendor is usually rated at tens of millions of cycles. Hundreds of millions are sold every year, and while some are for replacement use, many are for new designs where their unique combination of features is needed. EMRs do not come with an indicator LED but do make a click when they open and close; some find this annoying while others feel it is reassuring.
Both SSRs and EMRs are available with a wide range of contact ratings and other specifications (AC, DC, voltage, current). The decision as to which one to choose may be fairly obvious in some cases but in many cases it is not. For example, if the relay is in an industrial or flammable environment, the SSR is usually preferred since it has no moving parts and no risky sparks, while the EMR does have contact sparking. However, if the relay needs multiple contact poles, or both a contact closure and a contact open on each pole when energized, a single EMR provides all those. Further, SSRs tend to fail in a “contact closed” mode while EMRs tend to fail “open;” this may also be a consideration.
Summary
Many websites explain the relative attributes of the SSR and EMR, and there are many vendors who offer both relay types and thus can provide a fair assessment of each type. If their site only talks about the virtues of one type without at least acknowledging its relative downside, use careful judgement when making the decision.
In some cases, the SSR/EMR choice is obvious with one type having clear advantages in performance, cost, and other attributes. In many cases, however, the decision is more difficult, as each type brings a strong paired list of relative pros and cons. That’s when the design review gets tough, as at least one of the attendees will ask, and with some validity: “why didn’t you choose the other one?”
References
- Doran Scales, “Solid State Relay VS Mechanical Relay - Which One is Best?”
- TE Connectivity, “Electromechanical vs. Solid State Relay Characteristics Comparison”
- Omron, “Difference between SSR and Contact Relay”
- Efficient Plant, “SSR or EMR? Select the Right Relay”
- Happmart, “Introduction to solid state relays and the advantages and disadvantages”
- Crydom, “Why Use Solid State Relays?”
- Iowa State University, “Solid-State Relays for Control” (from 1976 but still makes good points)
- National Control Devices, “Solid State vs Mechanical Relays”
- Automation Technologies Online, “Solid State Relays vs. Electromagnetic Relays”
- Phidgets, “Solid State Relay Primer”
- Glolab Corp., “Relays, The Electromechanical amplifier”