Building an Adjustable, High Voltage Supply for Precision Sensor Bias Applications
August 18, 2021
Blog
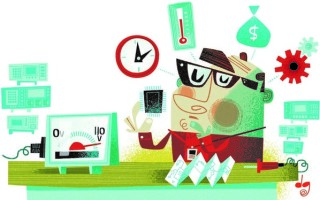
An adjustable, high voltage power supply capable of high precision output can be difficult to build. Errors often result from drift over time, temperature, and variations within the production process. The resistive networks traditionally used for feedback are common error sources.
In this article, a novel design utilizing an integrated circuit (IC) feedback path will be presented. This circuit is intended for sensor bias applications and provides higher precision, lower drift, greater flexibility, and even cost savings when compared to designs utilizing resistor networks for feedback.
Figure 1 illustrates the traditional approach to building an adjustable, high voltage bias circuit. A DAC is used to generate a control voltage, and an op amp is used to provide gain. The circuit in Figure 1 provides an output between ~0 V and 110 V from a control voltage ranging from 0 V to 5 V.
Since high voltage sensors are often quite capacitive, a resistor (R2) is normally used to isolate the op amp output from the load and avoid potential stability issues.
Figure 1. A traditional approach for a high voltage, adjustable bias circuit.
In some cases, these circuits work sufficiently well. When greater accuracy or more consistent long-term performance is needed, utilizing an IC to implement the feedback can be beneficial.
IC Feedback Implementation
The circuit shown in Figure 2 was configured with the following design goals in mind:
- Control voltage from 0 V to 5 V
- Output voltage adjustable from ~0 V to 110 V
- Output current >10 mA
- Initial accuracy of ±0.1% typical
- No external precision resistors required
The circuit in Figure 2 consists of three main sections: the control voltage, an integrator, and a feedback path. The feedback is provided by an integrated circuit instead of a resistor network as described earlier.
The control voltage input range is 0 V to 5 V. The circuit gain of 22 provides an output bias voltage ranging from ~0 V (0 V × 22) to 110 V (5 V × 22). To generate the control voltage, the AD5683R was chosen. The AD5683R is a 16-bit nanoDAC® that incorporates a 2 ppm/°C reference. Selecting the 5 V output span enables the circuit to provide a bias voltage ranging from ~0 V to 110 V in ~1.68 mV steps.
For the integrator, the LTC6090 was chosen. The LTC6090 is a high voltage op amp capable of rail-to-rail output and offering picoamp input bias current. The low input bias current is essential for achieving the high accuracy desired. Furthermore, the LTC6090 typically provides an open loop gain of >140 dB, so system errors resulting from finite loop gain are greatly minimized.
The LTC6090 compares the feedback voltage with the control voltage and integrates the difference (that is, error), thereby adjusting the output (VBIAS) to the desired setpoint. The time constant formed by R1 and C1 set the integration time and do not affect the amplifier accuracy, so precision components are not required. For testing, the load was modeled as an 11 kΩ resistor in parallel with a 2.2 μF capacitor.
Figure 2. An LTspice® schematic for ~0 V to 110 V bias.
Figure 3. A screenshot from the LT1997-2 design tool with attenuation = 22.
The LT1997-2 difference amplifier provides an attenuation of 22 (gain = 0.4545…) for the feedback loop. The connections required to achieve an attenuation of 22 can be easily determined by using the online calculator for the LTC1997-2. A screenshot from the tool is shown in Figure 3.
The LT1997-2 is very flexible and allows a wide range of gain/attenuation combinations. Examples are provided in the data sheet, and the evaluation board supports many gain combinations via jumper selectable settings.
Figure 4. The LT1997-2 eval board (gain is set via jumpers and additional wire).
Test Setup
The circuit was modeled in LTspice and met the design goals. Hardware testing was facilitated via the use of the following evaluation boards:
- EVAL-AD5683R: AD5683R DAC evaluation board
- DC1979A: demo board for the LTC6090 140 V rail-to-rail output op amp (modified for testing)
- DC2551A-B: demo board for the LT1997 configurable precision amplifier (modified for testing)
- DC2275A: demo board for the LT8331 boost, 10 V ≤ VIN ≤ 48 V, 120 VOUT at up to 80 mA
- DC2354A: demo board for the LTC7149 buck configured as negative VOUT; 3.5 V ≤ VIN ≤ 55 V; VOUT = –3.3 V/–5 V/adjustable to –56 V at up to 4 A
Generation of Control Voltage
The control voltage for the circuit was set using the AD5683R eval board. This board was connected via a USB port to a laptop running the Analog Devices ACE (Analysis, Control, Evaluation) software. ACE provides a simple GUI to configure the AD5683R and set the DAC output voltage. The output voltage provides the setpoint for the high voltage bias output.
Figure 5. Block diagram of test configuration.
Figure 6. A screenshot of the ACE interface for the AD5683R eval board.
DC Accuracy
The measurements in Table 1 and Figure 7 were made using a Keysight 34460A DMM at 24°C ambient. The output of the AD5683R eval board was calibrated to four decimal places and controlled via ADI’s ACE software. These results were from a single set of boards and do not represent min/max specifications.
Table 1. Measured Output Voltage vs. Expected Output Voltage
Control Voltage (V) |
Desired Bias Voltage (V) |
Measured Bias Voltage (V) |
Error (%) |
0.0000 |
0 |
0.0121 |
— |
0.5000 |
11 |
11.004 |
0.036% |
1.0000 |
22 |
22.005 |
0.023% |
1.5000 |
33 |
33.005 |
0.015% |
2.0000 |
44 |
44.005 |
0.011% |
2.5000 |
55 |
55.007 |
0.013% |
3.0000 |
66 |
66.007 |
0.011% |
3.5000 |
77 |
77.008 |
0.010% |
4.0000 |
88 |
88.008 |
0.009% |
4.5000 |
99 |
99.010 |
0.010% |
5.0000 |
110 |
110.009 |
0.008% |
Figure 7. Output voltage error vs. bias voltage.
Notice that below ~40 V output, the error is dominated by amplifier offsets within the circuit. At low bias voltages, the offsets are of greater magnitude than the gain errors. At higher bias voltages, the offsets contribute less as a percentage and the gain errors dominate. An error analysis is presented later in this article and provides more detail.
AC Response
A step function was applied to the control input for various voltages. The output and feedback voltages were measured (see Figure 8 through Figure 10). Notice that the bias voltage ramps smoothly to the desired value.
Figure 8. Step response (0 V to 1 V control input).
Figure 9. Step response (0 V to 2.5 V control input).
Figure 10. Step response (0 V to 5 V control input).
Start-Up Waveforms
The start-up waveforms for the power supplies and signals were observed. This was done to ensure that high voltage was not inadvertently applied to the bias output. The AD5683R provides a control voltage that starts at 0 V. As the power supplies ramp up, a small glitch of ~3 V was observed on the bias output. Given the high voltage nature of the bias output, this was deemed acceptable for test purposes.
If this circuit were to be used in a production system, it would be advisable to sequence the power supplies such that the control voltages were applied first with the high voltage power supply starting subsequently. This sequence would avoid the potential of high voltage spikes on the bias voltage output during the start-up process. A simple analog sequencer such as the ADM1186 would likely be sufficient to implement this function.
Figure 11. Start-up waveforms—power supplies.
Figure 12. Start-up waveforms—signals.
Photos of Test Setup
The LTC6090 eval board was mounted to the bottom of the LT1997-2 eval board. These were the only boards that required modification for the test setup. The DAC and power eval boards were used in their stock configuration and are not shown for simplicity.
Figure 13. The LT1997-2 eval board with the LTC6090 eval board mounted on the bottom.
Error Analysis
An error analysis was performed. The predominant error sources within the circuit are shown in Table 2 along with typical and maximum values.
The maximum error at 110 V bias output was calculated to be 0.0382% or 42 mV. This includes all errors from part variation as well as variations over the full temperature range (–40°C to +125°C). The typical error at 110 V bias output was calculated to be 0.00839%, which agrees well with the measured results (0.008% or 9 mV).
A Note About Power Supplies
The hardware used during testing was powered with supplies of ±5 V, 24 V, and 120 V. Here are some additional notes on how these supply rails were chosen:
- 5 V was required for the AD5683R DAC.
- In order to achieve 5 V output from the DAC, the power supply voltage may have to be set slightly above 5 V. Even small loads can limit the maximum output value. See Figure 38 on page 15 of the AD5683R data sheet for additional information.
- –5 V was used to allow the LTC6090 and LT1997-2 to operate with a control voltage input approaching 0 V.
- The input common-mode range for the LTC6090 is limited to 3 V above V–.
- The LTC7149 demo board was used for convenience to generate the –5 V rail.
- The LTC7149 eval board is capable of up to 4 A output.
- The circuit requires <25 mA at –5 V. A simple charge pump inverter would be sufficient. Consider the ADP5600 as an example.
- 120 V was used for V+ for the LTC6090.
- While the LTC6090 provides rail-to-rail output, heavy loads require additional headroom for V+.
- 24 V was used as the positive supply for the LT1997-2.
- This voltage was chosen to avoid Over-The-Top® operation. Certain performance characteristics of the LT1997-2 are degraded in the Over-The-Top region. See page 14 of the LT1997-2 data sheet for additional information.
Table 2. Output Voltage Error Analysis
|
Maximum Error from Data Sheet* |
|
|
|
||||
|
Error (%) |
Error (µV) |
Error (nA) |
Error at Feedback Node (µV) |
Error at Bias Node (mV) |
|
Error When Control Voltage = 1 V; Output = 22 V (%) |
Error When Control |
LT1997-2 Gain |
0.008 |
|
|
|
|
|
0.0080 |
0.0080 |
LT1997-2 Voltage Offset |
|
200 |
|
282 |
6.204 |
|
0.0282 |
0.0056 |
LT1997 IB Offset |
|
|
10 |
227 |
4.994 |
|
0.0227 |
0.0045 |
LTC6090 Offset |
|
1000 |
|
1000 |
22 |
|
0.1000 |
0.0200 |
|
Total Error (%): |
0.1589 |
0.0382 |
|||||
|
Typical Error from Data Sheet** |
|
|
|
||||
|
Error (%) |
Error (µV) |
Error (nA) |
Error at Feedback Node (µV) |
Error at Bias Node (mV) |
|
Error When Control Voltage = 1 V; Output = 22 V (%) |
Error When Control |
LT1997-2 Gain |
0.001 |
|
|
|
|
|
0.00100 |
0.00100 |
LT1997-2 Voltage Offset |
|
20 |
|
28.2 |
0.6204 |
|
0.00282 |
0.00056 |
LT1997 IB Offset |
|
|
0.5 |
11.35 |
0.2497 |
|
0.00114 |
0.00023 |
LTC6090 Offset |
|
330 |
|
330 |
7.26 |
|
0.03300 |
0.00660 |
|
Total Error (%): |
0.03796 |
0.00839 |
*Includes part variation and full temperature range
**At 25°C
Comparison of IC Feedback to Traditional Resistor Network Feedback
Let’s compare a few design metrics of the traditional approach shown in Figure 1 to the IC feedback approach shown in Figure 2. For this comparison, the LT1997-2 (see Figure 14) was chosen as the IC for the feedback network. Notice that highly matched precision resistors are embedded within the LT1997-2.
Figure 14. Block diagram of the LT1997-2.
Table 3. LT1997-2 vs. Two 1206 Discrete Precision Resistors (Note: 1206 Was Chosen for Working Voltage of 200 V)
|
Discrete Resistors |
LT1997-2 |
Comments* |
Size |
✔ |
|
2× (3.1 mm × 1.6 mm) vs. (4 mm × 4 mm) |
Cost |
✔ ✔ ✔ |
|
2 × ($0.11) vs. $3.39 (~1k price) |
Resistor Precision |
|
✔ ✔ |
0.1% vs. 0.008% |
Temp Drift |
|
✔ ✔ |
25 ppm/°C vs. 1 ppm/°C |
Max Sensor Voltage |
|
✔ |
200 V vs. 270 V |
*RT1206BRD07150KL, 1k pricing from Digi-Key as of December 2020
LT1997-2IDF#PBF, 1k pricing from ADI website as of December 2020
Table 4. LT1997-2 vs. Metal Film Resistor Network
|
Metal Film Resistor Network |
LT1997-2 |
Comments* |
Size |
|
✔ ✔ |
(8.9 mm × 3.5 mm × 10.5 mm) vs. (4 mm × 4 mm × 0.75 mm) Resistor is through hole and 10.5 mm tall |
Cost |
|
✔ ✔ ✔ |
$22.33 vs. $3.76 (~500-piece price) |
Resistor Precision |
Tie |
Tie |
0.005% vs. 0.008% |
Temp Drift |
Tie |
Tie |
1.5 ppm/°C vs. 1 ppm/°C |
Max Sensor Voltage |
✔ |
|
350 V vs. 270 V |
*Y0114V0525BV0L, 500-piece price from Digi-Key as of December 2020
LT1997-2IDF#PBF, 500-piece price from ADI website as of December 2020
Table 5. LT1997-2 vs. Silicon-Based Precision Resistor
|
Silicon-Based Resistor Network |
LT1997-2 |
Comments* |
Size |
✔ |
|
(3.04 mm × 2.64 mm) vs. (4 mm × 4 mm) |
Cost |
✔ |
|
$1.90 vs. $3.39 (~1k price) |
Resistor Precision |
|
✔ |
0.035% vs. 0.008% |
Temp Drift |
Tie |
Tie |
1 ppm/°C vs. 1 ppm/°C |
Max Sensor Voltage |
|
✔ ✔ |
80 V vs. 270 V |
*MAX5490VA10000+, 1k pricing from Maxim website as of December 2020
LT1997-2IDF#PBF, 1k pricing from ADI website as of December 2020
While the LT1997-2 is much more expensive than two chip resistors, it provides much better performance. When compared to a metal film resistor network, the LT1997-2 provides both size and cost advantages. When compared to a silicon-based resistor network, the LT1997-2 provides advantages in precision and working voltage. Furthermore, the integration of different resistor values within the LT1997-2 is an advantage over all the competing solutions providing gain flexibility via external jumpers if desired.
Using an IC that integrates precision resistors has another advantage that may not be obvious at first. The summing junctions of the amplifier are buried within the device and are not exposed to the PCB. This protects these sensitive nodes from unwanted inputs. Also, in many gain configurations, the internal resistors are connected externally to either ground or the output. This avoids leakage paths that could affect the circuit accuracy. Leakage paths are common error sources in higher voltage circuits. See page 14 of the LTC6090 data sheet for more information on this topic.
Conclusion
Adjustable, high voltage, bias circuits have traditionally utilized op amps with resistor networks for feedback to create a precision output. While this approach is simple to understand, achieving precise, repeatable performance can be difficult. Utilizing an IC to provide feedback instead of a resistor network can provide more accurate and consistent results.
Lionel Wallace joined Analog Devices in 2009. During his time at ADI he has held several positions across engineering and sales. Lionel currently serves as a field applications engineer based in Alabama. Lionel received his B.S.E.E. from Auburn University and M.S.E.E. from the University of Alabama Huntsville. He can be reached at [email protected].
Jason Fischer is an applications engineer with Analog Devices assisting the Americas East sales team. He supports multiple products with a focus on prototyping and evaluating switch-mode power supplies for industrial, telecommunications, medical, and military applications. His previous work experience includes production management, circuit design, test system development, and RF regulatory testing. Jason received his bachelor’s degree in electronics engineering from Bloomsburg University of Pennsylvania in 2014. He can be reached at [email protected].
Ben Douts is a field applications engineer with Analog Devices in South Carolina. He has worked in several roles including test engineering and integrated circuit design, focusing on precision analog circuits and power management. Ben received his S.B.E.E. from MIT in 1998. He can be reached at [email protected].