IoT in Manufacturing: Use Cases, Benefits, and Challenges
February 10, 2025
Blog
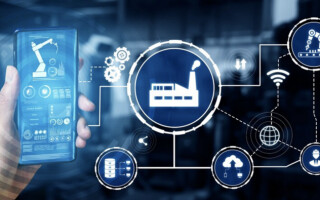
The Internet of Things (IoT), previously thought to be a futuristic idea, has evolved into a vital component of contemporary industry. IoT has redefined manufacturers' approaches to production and administration, promoting smarter and more efficient operations.
The fundamental technique for tracking machine performance, first used in 1968, has developed into a dynamic network of linked devices. By providing real-time data insights, these technologies enable automation and quick decision-making, promoting manufacturers' operational excellence.
IoT has a significant impact on manufacturing, with advantages including lowering downtime, optimizing workflows, and boosting resource efficiency. According to a GE survey, 58% of manufacturers consider IoT essential to their attempts at digital transformation.
This illustrates the growing dependence on data-driven tactics and linked technology to maintain industry competitiveness. There are countless opportunities for cost savings, innovation, and operational improvement using IoT in manufacturing. As technology develops further, it is ushering in a new production era characterized by intelligence, connectedness, and unmatched efficiency.
IoT in 2025 and Beyond
The manufacturing industry is undergoing a dramatic shift, fueled by IoT technologies that streamline operations, improve scheduling, and enable predictive maintenance all while collecting essential data. As we approach 2025 and beyond, organizations are expected to accelerate these improvements by leveraging IoT to reach better levels of efficiency, automation, and informed decision-making.
Projections for the IoT in the manufacturing market indicate that it will reach $87.9 billion by 2026. This rise demonstrates the immense potential and increasing use of IoT technologies, which rethink production workflows, improve resource allocation and boost competitiveness throughout the manufacturing landscape.
Benefits of IoT in Manufacturing
The changing complexity of the manufacturing scene necessitates highly advanced automation systems to meet consumer expectations. Manufacturing organizations can reap multiple benefits by incorporating the Industrial Internet of Things (IIoT), including increased operational efficiency, higher customer satisfaction, and more informed business decision-making.
Here are the main advantages of implementing IoT in a manufacturing setup:
1. Automated Data Collection
Manual data collection is frequently the standard in conventional settings. However, using paper-based techniques to collect and store data might result in human mistakes, which can compromise the data's accuracy and dependability.
On the other hand, automatic, real-time data collecting is made possible by combining machinery and gadgets with internet access. By guaranteeing the fast and accurate distribution of information, this strategy enables organizations to make better-informed decisions.
2. Optimum Productivity
By guaranteeing constant data flow from networked devices, IoT integration in manufacturing transforms machine use. Manufacturers can maximize operational potential during active periods by optimizing machine efficiency with the help of these insights on equipment performance. Additionally, the use of Industrial IoT (IIoT) devices increases worker productivity. Human resources can concentrate on more strategic and value-driven duties by delegating repetitive and routine chores to intelligent technologies.
3. Visibility of Production in Real Time
IoT technology provides companies the ability to keep an eye on manufacturing processes in real-time, providing a comprehensive picture of what's going on on the shop floor. To keep managers and supervisors updated on ongoing activities, they can connect directly to machines and retrieve real-time data. This constant flow of data can be examined to find important insights that can help identify problems and determine their underlying causes. A cycle of continuous optimization and development is fostered as manufacturers improve these systems over time.
4. Reduced Manufacturing Costs
IoT technology is transforming manufacturing by increasing operational efficiency and reducing expenses. To greatly streamline processes, connected devices are essential for automating tasks that previously required manual input and data collecting. Furthermore, sophisticated machine monitoring systems provide up-to-date information on the state and functioning of equipment. This makes it possible for manufacturers to implement proactive maintenance plans, which reduce downtime and save costly repairs, ultimately resulting in more effective and economical operations.
5. Minimize Quality Issues
Manufacturing processes are becoming more automated as a result of the use of Industrial IoT (IIoT). The likelihood of mistakes or flaws in items coming off the assembly line is greatly decreased by reducing the amount of human intervention in highly automated operations. Better product quality results from this, which raises consumer happiness and fortifies brand reputation, ultimately boosting the profitability of the company.
Use Cases of IoT in Manufacturing
IoT use cases and applications abound in the manufacturing industry. The potential to incorporate IoT sensors into almost any object and turn it into a smart gadget opens up a world of opportunities. The enormous number of machines, systems, and people that can be joined to form a coherent and intelligent network is astounding.
To understand where manufacturers are succeeding, let's examine some of the best instances of the Internet of Things used in the manufacturing sector.
1. Digital Twins
Digital twins provide a digital counterpart in a virtual world by representing virtual models of real-world systems, settings, or things. This idea is essential to industrial IoT because it makes sophisticated simulations and data-driven insights possible.
Digital twins allow producers to evaluate possible changes and their impacts in a virtual environment. By producing 3D replicas of assets, operational workflows, and complete facility infrastructures, they eliminate the necessity for real-world testing. This method enables safer, more effective decision-making and process optimization without interfering with ongoing operations.
2. Real-time Machine Monitoring
Think of a production system that gives operators and management a real-time indication of how well machines are performing. They would have all the data they need to address problems promptly and ensure that production schedules are met.
This is made feasible by real-time machine monitoring, which provides a stream of data directly from the machine, providing precise data suitable for in-depth analysis or on-the-spot decision-making.
3. Predictive Maintenance
Manufacturers can employ various maintenance techniques at their facilities, and as they become more sophisticated, they can apply increasingly sophisticated data-driven predictive maintenance techniques. IoT technologies that have been upgraded with machine learning algorithms may evaluate device data in digital manufacturing environments, learning from it to produce insights that can be put to use. Maintenance staff can more accurately determine when equipment may need maintenance thanks to this information, which provides important facts about the state and functionality of machinery.
Manufacturers can switch from conventional, time-based maintenance regimens to condition-based methods with IoT-enabled devices. They can continuously monitor particular characteristics and set thresholds that anticipate possible machine breakdowns before they happen by compiling thorough data on the health and functioning of the equipment.
4. System Integration
Almost anything can be connected in the context of the IoT, including systems, people, and equipment. The ability of various systems to use the useful data generated by others to improve their operations and efficiency is what makes system integration so potent.
Consider the Industrial Data Platform MachineMetrics. We can easily collect machine data using this platform, and since it is versatile, there are countless possible uses for the data. For example, the finance team can use production data to provide more accurate customer quotes while making sure a suitable volume of work is scheduled for the production process, the ERP can more accurately schedule jobs based on the machine's updated cycle times, and the CMMS can use this data to initiate automated maintenance when a machine malfunctions.
5. Automation
For Industry 4.0 to reach its full potential, especially in the area of industrial automation, the Industrial Internet is essential. Businesses can reduce downtime, enable predictive maintenance, and improve decision-making skills by incorporating automation technologies into industrial operations.
Automation has far-reaching effects, even though it frequently conjures up visions of manufacturing floors populated by robots. For example, manually keeping track of downtime and part counts can be time-consuming and prone to mistakes. The Internet of Things (IoT), on the other hand, allows manufacturers to automate data gathering and analysis by connecting machines and systems throughout the shop floor. Automation is expanded by this connectivity, which increases its effectiveness and influence.
Challenges of Implementing IoT in Manufacturing
There are several benefits to using IoT in smart manufacturing, including increased operational effectiveness, lower costs, and higher-quality products. However, it's important to recognize the difficulties in incorporating IoT into manufacturing settings. Manufacturers should be aware of several typical roadblocks before implementing IoT technologies. Before implementing IoT in your industrial operations, take into account the following important issues.
1. Data Privacy & Security
As the amount of private information gathered by networked devices keeps increasing, IoT security is still a major worry. IoT devices are becoming more and more connected, making them attractive targets for cybercriminals. These systems have flaws that are simple to take advantage of, giving illegal parties access to important data.
Beyond only stealing data, a breach can cause operations and activities in the industrial sector to be disrupted. Manufacturers must make sure that data gathering procedures adhere to privacy laws and safe storage techniques to reduce these dangers. Strong end-to-end encryption, thoughtful network segmentation, and regular security audits to find and fix possible flaws are all effective ways to protect sensitive data.
2. Return on Investment
This statement's veracity mostly depends on a company's approach. Relying on DIY or disjointed industrial IoT systems and factory monitoring sometimes results in increased expenses and necessitates a significant financial commitment. Along with other considerations, this strategy can also entail costly infrastructure improvements, including substantial cable connections, to guarantee device compatibility across generations and OEMs.
The return on investment (ROI) is questionable when companies choose these disjointed approaches. Many businesses embrace this strategy because they believe it leverages their internal knowledge. Assuming it's the best use of the resources at hand, they think it's advantageous to construct the system by utilizing the current IT and maintenance teams.
3. Analytics and Data Management
The massive volume of data collected by IoT devices presents another difficulty. It might be challenging to manage and analyze. To gain useful insights, firms must employ data analytics technologies. But this raises another problem. To apply IoT in manufacturing, one needs specific abilities.
You must be knowledgeable with machine learning, cybersecurity, data analytics, and other emerging technologies. A reputable IoT development company may collaborate closely with manufacturers to create and manage efficient IoT systems.
4. Integrating with Older Systems
Interoperability has always been a problem for many manufacturers, which makes them reluctant to embrace new technology. An efficient platform design is essential to getting beyond this challenge. IT departments may inadvertently make interoperability problems worse while developing IoT solutions internally.
Customization and flexibility are hampered by these do-it-yourself solutions' frequent limits, including proprietary and intellectual property restrictions. This inability to adapt makes integrating new technology into current procedures much more difficult.
5. Skill Shortage
For IoT to be implemented successfully in the manufacturing sector, an employee with the necessary skills and knowledge of IoT technologies and industrial operations is required. However, there is a recurring shortage of such talent. To overcome this obstacle, firms might have to put more money into training and education programs so that their staff can fully utilize IoT solutions in manufacturing settings.
Conclusion
IoT integration in manufacturing operations opens up many benefits, such as improved uptime, cost savings, and resource optimization, all of which lead to higher productivity. Developing a customized IoT implementation plan that fits your company's particular requirements, obstacles, and goals is crucial to ensuring a seamless and successful adoption process inside your company.
Pritesh is a blogger and tech enthusiast. He likes sharing his knowledge in a wide range of domains ranging from AI, data science, emerging technologies, and much more. His work is featured in several authoritative tech publications.