5 Key Ways To Successfully Adopt Industry 4.0 In Your Manufacturing Business
August 04, 2022
Blog
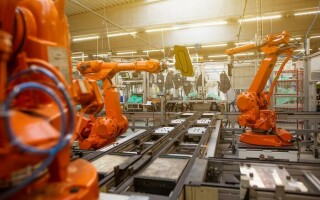
The industrial revolution that kicked off with the invention of the steam engine has come a long way over the past couple of centuries. There have been many radical evolutions that have happened during this timeframe which have leaped the productivity and output of industrial production.
Now we are at the cusp of the next evolutionary leap in manufacturing, popularly dubbed industry 4.0.
The industry 4.0 paradigm is possible due to the coming together of four key technologies.
- Industrial Internet of Things (IIoT)
- Cloud computing
- High-speed, low latency networks (5G and WiFi 6E)
- Big data analytics (Artificial intelligence and machine learning)
The huge volume of data generated by IIoT-enabled sensors and actuators is delivered over low latency networks to cloud servers. Cloud infrastructure is used to analyze this data and generate insights with the help of big data analytics. These insights can be used to improve production efficiency and bring down costs of operations. The data also helps in asset tracking, predictive maintenance, and various other facets of manufacturing.
Keys to successful Industry 4.0 implementation
Though industry 4.0 is quite beneficial for manufacturers, implementing the technology is a challenging task. The major challenge is the economic challenge of implementing Industry 4.0 since there is a need for a huge capital outlay. Another one is cybersecurity. The introduction of IIoT devices in factories also raises concerns about cyberattacks and data security. The global cybersecurity market has been growing in double digits to reach $ 240 billion, with strong demand from manufacturers adopting industry 4.0.
The following sections give you an idea of the five major considerations businesses should make to successfully implement industry 4.0.
Strategic planning
Implementation of industry 4.0 technology should not be based on a fad. Manufacturers need a crystal clear vision of the goals they want to accomplish with Industry 4.0. They also should have a roadmap for this journey. Such strategic thought on industry 4.0 will lead to fruitful implementation rather than implementation to participate in the next hot thing. With careful planning in place, businesses will also have the strategy to integrate legacy technologies with industry 4.0.
MidWest Materials is a producer of sheet-finished steel products based out of Perry, Ohio. The company was losing nearly $1 million every year due to unscheduled downtimes. They needed an industry 4.0 solution to bring down the downtime and reduce the losses. The company spent a year assessing requirements, strategizing the implementation, and analyzing various products. With this solid planning and research, they zeroed in on a CMMS for a wide range of reasons. Implementing the solution saved $454,000 in a single year while generating an annual ROI of 452%. The solution also helped to achieve an 80% reduction in overtime costs and dropped purchase turnaround from 45 days to 9.7 days.
Employee participation
Employees are always apprehensive of the introduction of new technologies in manufacturing facilities. One factor that contributes to that is changing the way they work. Another concern is a potential job loss with the introduction of more automation on the factory floor.
Manufacturers need to address the concerns of employees and clear their doubts by explaining how industry 4.0 will help them to be more productive. Employees will also appreciate the facets of improved safety with industry 4.0 technologies.
Consult with experts
There are not many examples of successful industry 4.0 in every field since it’s fairly new. A well-defined roadmap for implementation is also lacking for many manufacturing verticals as the technology is in its nascent stages. Businesses should take the effort and initiative to consult with industry 4.0 experts for their specific implementation - experienced consultants will be able to provide better directives and pitfalls to look out for. This will save huge time and cost for implementation.
Renault embarked on a journey to adopt industry 4.0 in its manufacturing processes. The scale and size of their operations are difficult to comprehend and tackle for a single implementation partner. To this end, they dissected the initiative into functional components that could be addressed by vendors with differing sets of expertise. Choosing the best partner for each component helped Renault build a world-class manufacturing process among its automotive peers.
Cost considerations
Economic aspects of industry 4.0 adoption have to be thought through. As mentioned previously, there is a need for significant capital outlay for the implementation. Manufacturers have to calculate the breakeven period for such investments and also think through the expected return on investment. It is ideal to overhaul the manufacturing process completely in one go, but many businesses may not be able to bear the initial costs. Manufacturers can consider rolling out industry 4.0 technology in a staggered manner to minimize the pain of large capital expenditures.
Continuous improvement
Manufacturers should embrace the philosophy of Kaizen, which stands for continuous improvement. They need to always be looking for avenues of improvement for industry 4.0 implementation and this could be improving the cybersecurity aspects of the implementation as well. Another avenue for improvement is in the analytics department. Similarly, there are many such possibilities for improvement and all such paths should be explored.
Wrapping up
Successful implementation of industry 4.0 technologies in manufacturing facilities is essential to stay relevant in the competitive market environment. As with most things more than technical know-how, common sense is the determinant of success. Technical knowledge can be obtained by learning or acquisition, but doing sensible things is much rarer, and manufacturers should focus on getting that right.
Bryan Christiansen is the founder and CEO of Limble CMMS. Limble is a modern, easy-to-use mobile CMMS software that takes the stress and chaos out of maintenance by helping managers organize, automate, and streamline their maintenance operations.