Asset Monitoring is a Key Step in the Digital Transformation Journey
September 23, 2020
Story
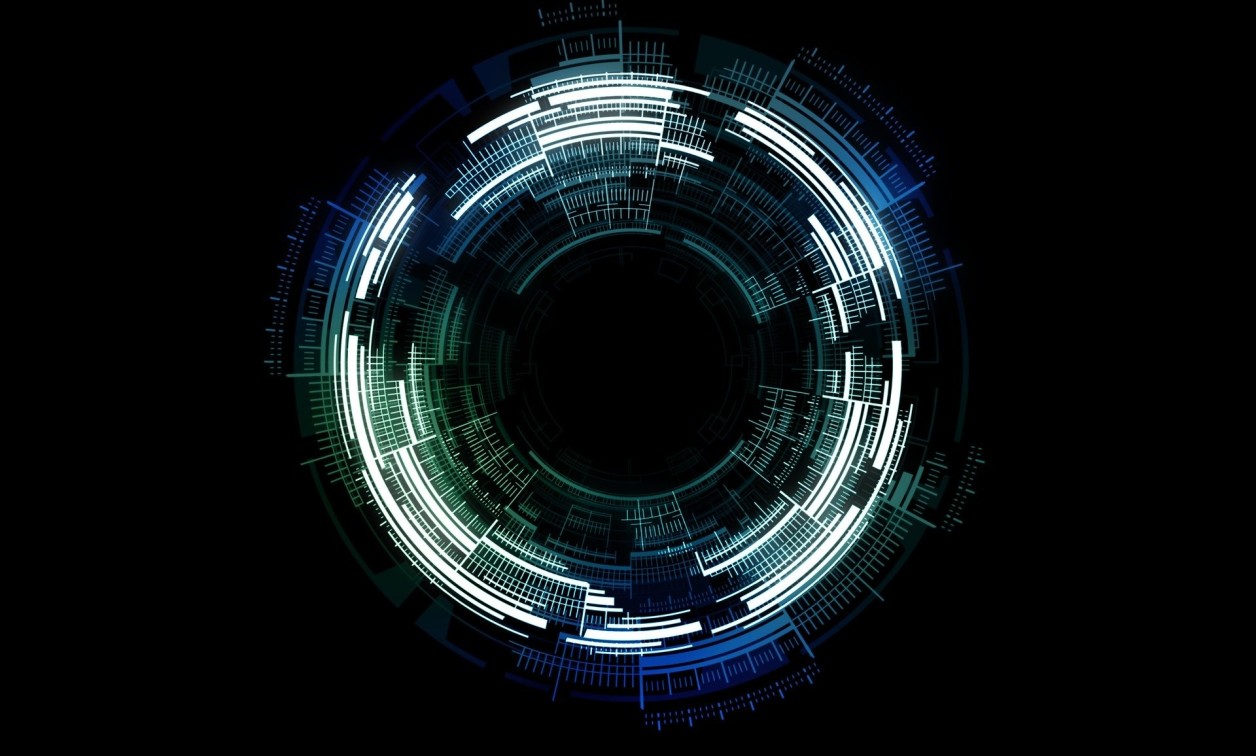
The widespread adoption of advanced machinery has fueled unprecedented levels of speed and efficiency in factories around the world.
The widespread adoption of advanced machinery has fueled unprecedented levels of speed and efficiency in factories around the world. Even in complex operations involving hundreds of machines, several minutes of downtime for just one machine can significantly impact profit margins. To minimize unplanned downtime and reactive repairs, manufacturers need to be able to anticipate production issues before they happen.
Many manufacturers are overcoming these issues with real-time monitoring capabilities, enabling them to more accurately monitor their machines and unlock richer insights. What once required time-consuming, manual observation can now be done in real-time with extreme accuracy. Ultimately, this empowers manufacturers to reduce downtime, enable predictive maintenance, improve asset efficiency, and more. The ability to identify and understand issues faster is the difference between falling behind or staying a step ahead of competitors.
A lack of visibility across assets can lead to significant challenges
Rockwell Automation leverages a large number of molding machines, which are massive industrial presses that weigh anywhere between 30-300 tons. Due to their complexity, each press is made up of more than 2,000 tools and differing ages. These machines can be particularly difficult to monitor. This made it nearly impossible for Rockwell Automation to have a unified view across the entire factory, even regarding information as simple as which machines were running when.
Operators and supervisors had to walk through the plant and manually check the lights on each press to determine their status. Not only was this time-consuming for employees, but it also meant machines could go down and it would take minutes or even hours for operators to discover the outage. The impacts were significant—during outages, the machine’s plastic degrades, decreasing machine health as well as product quality.
In addition to visibility issues, the company noticed their fixtures were being damaged when they ran too many products. If fixtures required maintenance, it could take thousands of dollars to fix each issue, on top of costs associated with the resulting downtime and blocked orders. Without a way to determine the root cause of issues, it was difficult and time-consuming to conduct troubleshooting and analysis.
To shift from reactionary to proactive machine management, Rockwell Automation needed to understand all the various factors that caused a press to go idle or fixtures to become damaged. In collaboration with PTC, the company was able to make automated, real-time monitoring a reality. The collaboration created a unified dashboard which gave Rockwell Automation automated and enhanced visibility across the factory floor.
Factory-wide visibility with real-time status monitoring
FactoryTalk InnovationSuite unified data streams coming from various software and hardware sources into a consolidated view. But first, they needed to connect legacy machines. During this phase, they added PLC capabilities to legacy presses that varied in size and age. Leveraging the flexibility of ThingWorx, they were able to easily connect each press and begin collecting data.
To see an overview of each production area, Rockwell created a digital twin for their Molding and Safety Mat Machines. The digital twin provided a 2D visual rendering of machines and their parameters. In collaboration with PTC, Rockwell developed connectors to simplify aggregation of OT data related to assets, process and production into FactoryTalk InnovationSuite. These tools help ensure data connectivity, context and modeling. This integration enabled Operations to set and see alert conditions visualized in a single screen—for example, if the press and heat were turned on, but the press wasn’t cycling.
The project resulted in a single dashboard that monitors its molding presses. On one screen, manufacturing associates can see which presses are running, which are idle, and when the tooling will require maintenance. The simplified dashboard consists of icons representing each of the 35 presses, with color coding to show status. While the dashboard is intended for supervisor or operator use, manufacturing associates can also use it to quickly understand machine status.
The dashboard displays machine alerts, notifying operators and supervisors when factors like temperature, humidity, water flow, or water pressure move outside of their optimal range. It also enables operators to track critical data, such as throughput or product quality, so they know when presses are behaving abnormally. This information serves as the foundation the powerful predictive capabilities Rockwell Automation plans to build in the future.
Enabling a future-state of predictive and prescriptive maintenance
Since implementing the solution, real-time, objective data has empowered Rockwell to improve machine efficiency and capacity. Outages that caused plastic breakdown and affected machine health are a thing of the past, improving the overall quality of products produced. The visibility enabled by data allows operators to see and understand machine status, process parameters, maintenance requirements based on utilization rates, and scheduled maintenance compliance. Armed with greater visibility into all 35 of their machine presses, the company created a more efficient factory and significantly improved machine uptime. This will continue to be an important tool in overall continuous improvement.
The solution is also a boon for worker productivity and morale. For plant workers, the dashboard has helped level the playing field. It takes all ambiguity off the table.
Rockwell Automation sees this use case for real-time visibility as another step of their larger digital transformation journey. By establishing a baseline for many machine performance parameters, there is now a new use case to analyze trends in data to make predictions about downtime or possible errors and to prescribe adjustments or maintenance before an outage. Now we have the data sources merged, and we can constantly create new models to further improve our processes.