Edge AI Puts the “Smart” in a Smart Factory
June 07, 2023
Sponsored Blog
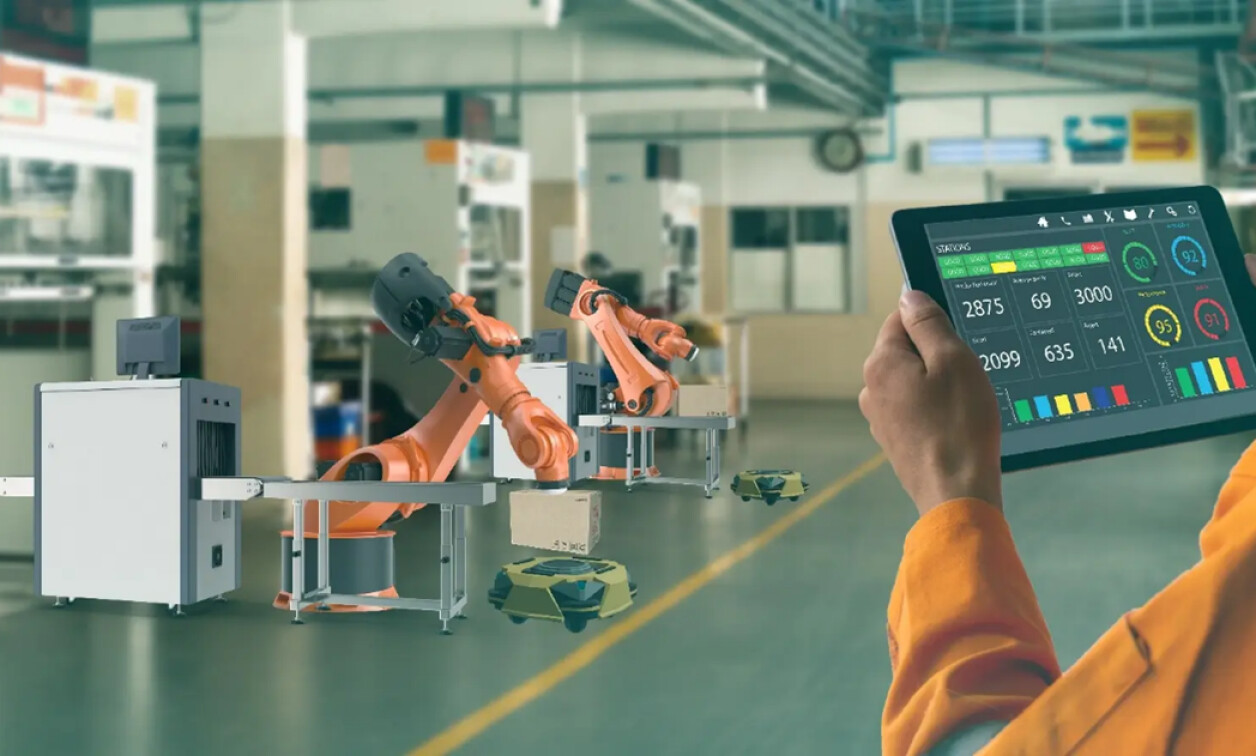
The evolution within a factory or other manufacturing facility has been occurring as long as those establishments have existed. Getting higher yields, more efficient production, etc., is a never-ending goal. To that end, the “smart factory” was born.
In most definitions, a smart factory is a highly automated manufacturing facility that utilizes advanced technologies and interconnected systems to enhance productivity, efficiency, and flexibility in the production process. It incorporates various elements of Industry 4.0, the fourth industrial revolution, which focuses on the integration of digital technologies into manufacturing.
Smart factories leverage the IoT to connect machines, sensors, and devices throughout the production line. This enables real-time data sharing and communications between different components of the manufacturing process. In some more advanced cases, smart factories make use of automation and robotics to perform repetitive and labor-intensive tasks. This might include assembly, packaging, material handling, and other production activities reducing human intervention and increasing productivity.
Add AI To the Mix
Introducing artificial intelligence (AI) and machine learning into the smart factory potentially increases productivity and efficiency to levels that could not otherwise be obtained. These technologies allow for advanced analytics to process and analyze the vast amounts of data that’s collected from various sources within the factory. This helps in making data-driven decisions, optimizing processes, predicting maintenance needs, and improving overall efficiency. In some cases, the factory can be completely autonomous.
Data is maintained and analyzed at the Edge of the IoT. Deploying an Edge computer with the appropriate horsepower will allow for even more features, including virtualization, predictive maintenance, and cybersecurity.
Virtualization permits many of the physical manufacturing processes to be simulated and represented digitally in a smart factory, which leads to virtual testing, optimization, and visualization of production systems, leading to faster prototyping, reduced downtime, and improved quality control.
Predictive maintenance is a proactive approach to maintenance that uses that same data analytics and analysis to predict when equipment or machinery is likely to fail and/or require regular care. By monitoring the condition of equipment in real-time, administrators can identify potential issues before they cause a breakdown or disruption in operations. And, depending on the facility, shutting down a production line even for a short interval can be very costly.
With predictive maintenance, activities can be scheduled around times that make more sense, such as during slower periods. The result is long-term cost savings, higher and better yields, improved equipment reliability, and an extended equipment lifespan. It also makes for a safer facility by reducing the risk of accidents caused by equipment failure.
Stay Local To Keep Your Factory Safe and Secure
With increased connectivity and digitalization, smart factories unfortunately become a target for hackers. Protecting sensitive data, intellectual property (IP), and ensuring the integrity of systems is crucial in maintaining a secure and reliable manufacturing environment. Today’s Edge computers are designed with the security features needed for “today” and should be upgradable to stay ahead of the curve.
By maintaining the compute functions of your smart factory at the Edge of the IoT, you reduce, or potentially eliminate, having to go to the Cloud for tasks. That immediately reduces costs and increases security. Improvements are being made in 5G and other wireless technologies, but it’s clearly not as good as having the data remain local.
Edge AI also enables intelligent decision-making and autonomy in robotic systems that are deployed in smart factories. Decisions are based on sensor inputs adapting to changing environments. It also permits the robots to safely collaborate with human workers while being more effective.
Edge-based AI also works well for real-time monitoring and control, where decisions can be made and procedures implemented on the fly. And when data does need to go to the Cloud, it can be pre-processed and compressed, so less data is transmitted, and the results are generally better and more cost effective.
It is also inherently better at anomaly detection in machinery and equipment. Using sensor data collected at the Edge, AI models can detect patterns indicative of faults or performance degradation. Such data can come from a variety of sources, including sensors located on the factory floor or vision systems. Smart factories are now typically equipped with cameras and image processing capabilities.
The AI functionality takes those images and interprets it into usable and actionable information. Machine vision can be used to automate processes, perform quality control, and enhance efficiency. This can be done through inspection and defect detection, object classification, quality and compliance, and product tracking/tracing. This is all done in real time, thanks to Edge AI.
The MiTAC Advantage
One platform that offers the compute power to perform Edge AI in smart factory applications is the MiTAC MiAi-H8 real-time and AI inference acceleration card. The PCIe expansion card is powered by four or eight power-efficient Hailo AI processors for a maximum performance level of 208 TOPS.
It offers an industrial grade design with all solid capacitors and wide temperature support with passive and active cooling alternatives available. System design can be expedited using the Hailo-8 software development kit.
A second system that exhibits the qualities needed for AI in the factory is the MiTAC MZ1-10ADP rugged GPU computing system. It is designed with an Intel 12th Gen Alder Lake-S Xeon Core i processor, up to 125 W. The platform supports dual DDR5 SO-DIMMs (up to 64 Gbytes), and adds a host of interfaces, including HDMI, DisplayPort, VGA, and dual 2.5-Gbit/s LAN.
Also offered are extra slots for OEMs to plug in two high-performance graphics cards, each up to 600W, further increasing overall system performance. Such a level is needed when deploying inference or machine learning capabilities.
The reasons to deploy an Edge AI smart factory should be clear, whether you are building from scratch or upgrading an existing factory. You can expect higher efficiency and higher yields, with lower costs to your capital equipment, and potentially less people required to operate and manage the factory.