A step-by-step guide to planning and designing a PCB assembly for an embedded system
February 13, 2018
Story
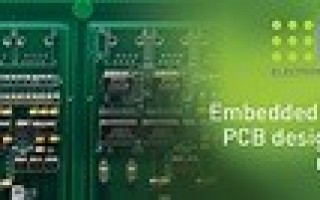
PCB assemblies are a vital part of embedded systems, which vary in their function, size and complexity so dramatically that careful planning and design is required to meet the exact requirements.
![]() |
The advance of technology means that embedded systems are now part of a multitude of applications. Encapsulated by the devices they control, these special purpose computer systems can be found in DVD and MP3 players, fridges and microwaves, car and spacecraft, as will be apparent at embedded world 2018 in Nuremberg, Germany.
Printed circuit board (PCB) assemblies are a vital part of embedded systems, which vary in their function, size and complexity so dramatically that careful planning and design is required to meet the exact requirements. These requirements are becoming ever more complex, as embedded systems are used to serve increasingly complex roles as internet connectivity becomes a prerequisite and the demand for smaller devices grows.
Here is a step-by-step guide to what goes into planning and designing a PCB assembly for an embedded system:
Defining the requirements
Every design project begins with a set of requirements. The most obvious place to start is prescribing what it is that the PCB assembly will be required to do but that isn’t all. Size matters, as does how it connects to other parts of the embedded system, where it needs to be placed and what kind of environmental conditions it will be subjected to. All of these factors will affect the complexity of the printed circuit board assembly and, thus, how many layers it will need, the type and number of components and connections.
Creating a schematic
Once the designers have established all the requirements and developed a concept to meet them all, they draw up a detailed schematic – a diagram showing which components are required, where they need to be placed and how they need to be connected. They will also draw up a bill of materials to establish exactly which parts they’re going to need based on what the operating voltages and current levels are of each component as well as their size, price and availability.
Electronic design automation software
Having created the schematic, these details are then entered into an electronic design automation software package, which creates and collates a set of documents, called a Gerber or CAD file, that can then be used as, essentially, a set of instructions to fabricate the PCB assembly.
Selecting the fabrication method
The fabrication method chosen for any PCB assembly will depend on the original requirements, the resources available, the timeframe and the budget. MPE Electronics often trains its staff, buys in resources and creates processes to meet its customers’ requirements, giving the company flexibility when it comes to design.
Testing
The final phase is to prescribe which tests the PCB assemblies will undergo to ensure the design fulfils the requirements. MPE employs a number of different testing techniques and recently extended its capabilities by investing in a new environmental testing machine to ensure its PCB assemblies can withstand the environmental conditions they will be required to operate in.
MPE's designers are experienced in creating PCB assemblies for embedded systems of various types so can advise electronics manufacturers on exactly what they will need and come up with a design that fulfills all their requirements within the specified timeframe and budget.
Find out maore about MPE Electronics by calling 01825 764822 or emailing [email protected].