Stop doing paper-based PCB layout reviews
March 07, 2017
Blog
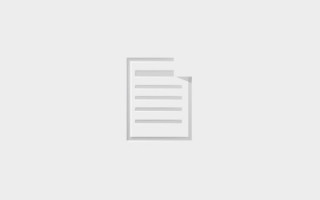
Are your electronics designers still depending on circuit-diagram print-outs when working together internally? Or are they all moaning about how tedio...
Are your electronics designers still depending on circuit-diagram print-outs when working together internally? Or are they all moaning about how tedious it is to have to zoom in and out and search for details in PDFs? Highly complex systems are developed from miniaturized electronics, yet when experts from different departments collaborate during the development process, they still rely on paper-based plans and diagrams. That’s completely outdated in the digital age.
The premise is clear: throughout the development life-cycle, from the initial circuit diagram to the final product, data is edited, exported and imported by various specialists using different systems. Transfers, imports and exports are exposed to possible errors. The potentially disruptive media clashes within the tool chain are an industry-wide weakness. Development, layout design, board manufacturing and assembly, quality assurance, purchasing, and distribution will all be working on the same product, but will be using various systems that focus on different aspects in non-uniform data formats.
From network lists to 3D CAD data for the housing into which a PCB will be installed; everything related to an electronic product is available in a digital format. The challenge is to find a way to filter only the relevant information and to prepare it so that it can be discussed and used in decision-making.
There’s a proven way to summarize everything you need to know about a development project in a single file—the data format ODB++. It was developed as a standard to provide and transfer circuit-board-design information from design to manufacturing, as well as across design tools from various CAD and CAM vendors. With ODB++, all PCB production-data can be stored in one data record. This isn’t just for layout, but also for component metadata, placement positions, etc. So, the data exists, it just needs to be utilized.
As a member of the ODB++ Solutions Alliance and the IPC-2581 Consortium, EasyLogix has been developing a tool called PCB-Investigator, which can visualize any aspect of the product data. As a standalone CAD system for the review process, for some the idea isn’t always immediately intuitive. My recommended approach requires only a small but highly effective process change: the universally valid data record needs to be maintained in ODB++.
Each expert continues working in his or her respective ECAD and MCAD systems, but the binding and latest version of the project is stored in ODB++. And there’s more: the entire product-lifecycle can be tracked via the data and, at the push of a button, versions and variants are ready for comparison, visually presented in 2D and 3D by PCB-Investigator.
By working with one set of data across every development stage, the paperless review process offers even more process advantages. What used to be a strictly sequential process, whereby a project would be passed from one department to the next, can now be accelerated through a synchronous work flow.
Mistakes are more costly the longer it takes to discover them. If, for example, specialists for solder paste printing or pick & place can identify potentially critical constellations from the layout data at an early stage, it can potentially save on prototyping and accelerate speed to market.
Future developments for the use of ODB++ with the PCB-Investigator focus on simulation. For example, leakage current analysis or high-precision thermal simulations can be simply carried out at any time at the push of a button. Many quality control aspects previously had to be undertaken by specialists and only when a board was completed. Now they’re just as easily available as any other 2D or 3D view of the design data.