Modern Robots are Coming, Both for Consumer and Industrial Applications
May 26, 2022
Sponsored Story
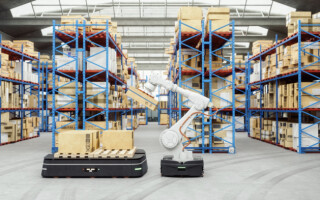
Service robots are becoming more prevalent in today’s society. They serve many functions, and in a perfect world, they would automatically support humans in their everyday life. On the industrial side, they would assist in duty fulfillment, among lots of other potentially tedious duties.
Such robots have spawned a new term—cobots, which is derived from collaborative robots. The definition of a cobot is a robot that can operate safely and securely in the same environment in relatively close proximity with humans. This is due to the simple fact that cobots have much higher standards for safety and the security, with far more sophisticated sensing electronics.
Note that some in the embedded industry offer a slightly different definition of the cobot, claiming that a cobot represents the smaller sibling of the industrial robot, such as those big arms that we often see in an industrial setting.
Speaking of the industrial side, typical duties of those robots include transporting materials within a building, handling “unergonomic tasks” like moving heavy items, feeding machines within a proximity that would be unsafe for humans, and assembly operations. Today’s robots often work inside some sort of cage or fenced in area to protect the people from, the robots and vice-versa.
Even for tasks that are easily handled by humans, there are reasons for using the cobots. For example, cobots don’t need days off (except for scheduled maintenance), and they don’t get tired or sick, and they never complain.
Good examples of consumer robots are the now-popular iRobot Roomba or Ecovacs Deebot vacuum cleaners. Lawn mower robots are also gaining in popularity. Such devices are expected to bump into objects and learn from that experience. But that “bump and sense” operation would not work for all applications.
Moving forward, we can expect to see a lot of growth in indoor robotics that will support elderly people, for example, in hospitals or residential settings, where they could either set off an alarm or assist an individual. More advanced mobile robots could deliver meals or packages to people.
Delivering the Right Solutions
Infineon plays in this space in various ways, particularly with the moving parts of the robot. The company doesn’t produce the motors themselves, but rather most of the electronics that enable and control that motor, as well as the devices that enable the sensing functions, including the advanced radar time-of-light sensors, the connectivity, the security and the HMI functional blocks. Some of the sensors, including the time-of-light sensors, are still a bit of pricey, especially for consumer products where margins tend to be slimmer. Note that Infineon is being careful to stop at the firmware level, to avoid competing with its customers.
A word of caution—do not underestimate the importance or difficulty of designing the power subsystem. At the end of the day, the robots need to move around, preferably untethered. So the power consumption and efficiency specifications are vital, as well as the efficiency of the motors themselves. At the same time, fast charge times are a desirable feature.
For applications that deal with motor control, Infineon has added a pair of three-phase smart motor drivers to its popular MOTIX family of low-voltage motor control solutions, namely the MOTIX 6EDL7141 and the MOTIX IMD701A, which have been developed for BLDC motor drives operating from battery voltages in the 12- to 48-V range.
More Collaboration
Looking into the future, you can expect to see more collaboration and coexistence between the humans and robots. It’s one thing to ensure that they stay separated. It’s something totally different to have them working cohesively, and that’s the next step. And of course the key is to have this harmonization occur safely. That’s where the far more sophisticated sensors are required, and that’s exactly what’s needed for adoption to occur at a higher rate.
Most of the current consumer products communicate over WiFi, with some use of Bluetooth mixed in. In the more industrial service robotics space, it’s WiFi as well. But there are many examples of cobots that are wired, particularly on the industrial side, where the movement is more limited and well known.
As 5G starts to permeate the industrial sector, cobot functionality (and their design) could change drastically. The speed of 5G would help guarantee more real-time actions from the cobots. It would also simplify the process of over-the-air updates, directly from the manufacturer.
AI Must Play a Key Role
While artificial intelligence (AI) is one of the hottest industry buzzwords right now, it certainly has a play here when you’re designing cobots. However, the beauty of a setup that employs a 5G connection is that the AI algorithms needn’t be handled in the cobot itself. As long as the sensors are designed in properly, and the communications can occur fast enough, that AI engine could be anywhere, including at some centralized location and/or in the Cloud. In this scenario, the decisions can take the inputs from lots of cobots rather than just one.
When it comes down to it, we all have this mental picture of what the cobots should look and act like. And that’s not necessarily to far from reality—eventually.