COM-HPC Provides Server-Level Compute Power for Edge Computing Applications
February 01, 2021
Blog
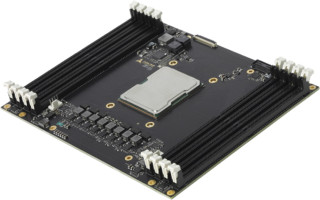
New Computer-On-Module (COM) High-Performance Computing (HPC) specification targets the increasing server-level requirements of high-end computing applications on the edge.
The term Industry 4.0, also known as the Fourth Industrial Revolution, refers to the ongoing automation of traditional manufacturing and industrial practices using modern smart technologies. The rapid growth of Industry 4.0 and the Industrial Internet of Things (IIoT) has resulted in an exponential growth of data from sensors and actuators.
The computational requirements of Industry 4.0 and the IIoT are starting to experience even steeper growth due to additional technology drivers, including artificial intelligence (AI), machine learning (ML), and 5G applications. As a result, embedded systems on the edge, where the internet meets the real world, are seeing an exponential growth regarding their requirements for computational power and performance. Due to latency considerations and communication costs, this data needs to be processed at the source to provide actionable information in close to real-time. Performing this processing at the edge is known as “edge computing.”
In addition to the desire for increased computational capability, system designers and end users also wish to “future-proof” their systems. There are many aspects to this, such as the availability of second-source vendors in case an existing supplier exits the market, along with the ability to upgrade systems with enhanced capabilities over time to satisfy the demands of future applications.
Computer-on-Module (COM)
The terms "Computer-on-Module" and "COM" were coined by market researcher Venture Development Corp (VDC) in 2001. COMs are complete embedded computers implemented on a relatively small printed circuit boards (PCBs). These designs are centered on a processor (possibly containing multiple cores). memory, input/output (I/O) controllers, and any other features required to implement a fully functional computer.
However, unlike traditional single board computers (SBCs), COMs lack the standard connectors that would allow input/output peripherals to be connected directly to the board. Instead, the COM is plugged into a carrier board (or “baseboard”), which contains any additional components and subsystems. This allows the COM to focus on providing the core compute capabilities, while the carrier boards support the “secret sauce” that allows system designers to differentiate their products from competitor offerings.
Some systems also include field-programmable gate array (FPGA) devices, which may be mounted on the COM itself or on the carrier board. These devices may be used to provide hardware accelerator functionality and/or enhanced interface functionality. Using FPGAs adds to the modularity of the COM concept because I/O functions can be adapted to special needs, evolving standards, and -- potentially -- completely new protocols without the need to modify the PCB.
Introducing COM-HPC
As was noted earlier, system designers and end users wish to “future-proof” their systems. The best way to do this in the case of COM-based systems is to use an industry standard that is supported by many COM vendors.
The preeminent COM standards body is PICMG, which is a nonprofit consortium of companies and organizations that collaboratively develop open standards for high performance telecommunications, industrial, test-and-measurement, medical, edge, and general-purpose embedded computing applications.
Founded in 1994, the PICMG membership boasts over 140 member companies that specialize in a wide range of technical disciplines, including mechanical and thermal design, very high-speed signaling design and analysis, networking expertise, backplane and packaging design, power management, high-availability software, and comprehensive system management, all of which come together in the design of SBCs and COMs.
PICMG is now entering the final stages in the development of its new COM-HPC computer-on-module specification, where HPC stands for “High-Performance Computing.” COM-HPC will address the needs of the very high end of the industrial edge computing market.
As was previously discussed, edge computing is an exponentially growing market segment requiring ever higher performance. As a result, the high-end embedded processors used in edge systems can have 20 cores or more. The system memory requirements of such systems have also grown steeply. The combination of multiple processing cores and virtualization means that some systems require 256 gigabytes (GB) of memory, or more. Another consideration is that 10 gigabits per second (Gbps) Ethernet is no longer sufficient for many applications, many of which demand higher bandwidths of 25, 40, and even 100 Gbps. All of these high-end requirements are addressed by COM-HPC.
COM-HPC Applications
Target markets for COM-HPC modules span a wide range of application areas -- including autonomous vehicles, robotics, unmanned aerial vehicles, 5G (small cells, base stations, and infrastructure) -- that require different combinations of high-performance and/or high memory and/or high-speed interfaces.
(COM-HPC modules address a wide range of target markets and applications (Image source: ADLINK))
One big driver for COM-HPC is going to be AI. In the not-too-distant future, everything that can drive, fly, or float is going to either have an AI co-pilot or be fully autonomous. Similarly, every robotic device, including stationary robots, mobile robots, and collaborative robots (cobots) will be equipped with sophisticated AI/ML capabilities, where cobots are intended to interact collaboratively and in close proximity with their human colleagues. Furthermore, even hard-to-come-by skills (surgery, for example) will be augmented by AI.
Another big driver will be task consolidation. For example, today’s trains have many IT-based services -- reservation management, on-board Wi-Fi, video surveillance -- all of which are provided by different companies in different “boxes” scattered around the train. Consolidating all of these tasks into a single COM-HPC “box” -- with each task running on its own virtual machine on its own processing core with access to tens of gigabytes of memory -- will dramatically reduce deployment and maintenance costs and resources.
In the case of rugged and/or special purpose communications devices, such as 5G base stations, packet inspection systems, and front running trading systems -- all applications that cannot use off-the-shelf solutions and are oftentimes deployed in harsh environments.
COM-HPC Dimensions and High-Speed Connector
Five COM-HPC sizes are defined -- two server modules and three client modules -- with the largest server module offering eight on-board DIMM sockets supporting up to 512 GB of memory (these are the vertically orientated sockets in the images below).
(New COM-HPC module sizes (Image source: ADLINK))
Along with their new formfactor, COM-HPC modules are equipped with new high-speed, high-density 400-pin connectors. Since COM-HPC modules each have two of these connectors (the horizontally orientated connectors in the image above), this means 800 pins per module.
(COM-HPC employs a new kind of connector (Image source: Samtec))
COM-HPC Server Pinout
With regard to the 800 pins provided by the new high-speed, high-density COM-HPC connectors discussed above, there are several points that stand out. First, the power input is a single 12-volt supply that can deliver up to 358 watts of power, which is more than sufficient to drive high-end CPUs with 20 or more cores, 512 GB of memory, and any other components.
(COM-HPC server pinout (Image source: ADLINK))
In the case of the PCIe (GEN5) interfaces, there are 3x16 = 48x lanes on the J2 connector and 1x16 = 16 lanes on the J1 connector, resulting in a total of 64 lanes in all. Also, there is an additional 1x PCIe lane for board management control (more on this below) and there are 8x USB 2.0, 2x USB 3.X, and 2x USB 4.0; along with 1x 1GbE and 8x 10GbE.
Also of interest for many high-performance systems is the fact that COM-HPC server modules support the Intelligent Platform Management Bus (IPMB) and the Intelligent Platform Management Interface (IPMI), which is set of computer interface specifications for an autonomous computer subsystem that provides management and monitoring capabilities independently of the host system's CPU, firmware, and operating system.
The Cost of Memory
One major consideration for embedded systems architects and developers is the cost of memory, especially in the case of the memory-hungry markets for which COM-HPC is targeted.
The reason the COM-HPC server type employs DIMM memories is not only to enlarge the total possible memory capacity, but also to facilitate the best price per GB. At the time of this writing, the sweet spot for price-capacity is 32 GB, which means users can enjoy 8x32 GB = 256 GB at the best price-capacity on the market.
For those users requiring more memory, they can achieve this 8x64 GB = 512 GB. Although this currently comes at a 5% price disadvantage, it is expected that the sweet spot for price-capacity will be 64 GB in the not-so-distant future.
Out-of-Band Management Control
Many earlier COM modules supported a limited form of management control by means of an application programming interface (API) called EAPI, which typically focused on lower-level embedded management functions that are not abstracted through drivers, such as watchdogs, display brightness and backlight controls, logistics, EEPROM storage, and I2C/SMBus control.
While COM-HPC will still support EAPI on both client and server modules, the COM-HPC server type will also support full IPMI or its open source variant, Open BMC, because of its network centric nature.
(Typical out-of-band management control scenario Image source: ADLINK))
This diagram above shows a typical implementation of IPMI in combination with a modular formfactor. This illustration reflects only a single COM-HPC module, but multiple modules can be controlled by a single BMC on the carrier.
The Future is Now
As a leading member of the PICMG consortium, ADLINK plays a large part in defining the COM-HPC standard and is at the forefront of COM-HPC development.
For example, ADLINK’s proof-of-concept COM-HPC module has a Server Type feature set, is Size E (160mm x 200mm), and provides up to 16 computing cores in a 110W platform with 8 DIMMs. A heat-spreader is mounted on top of the module to extract heat to an external cooling device.
(A proof-of-concept COM-HPC Server module (Image source: ADLINK))
ADLINK can provide both COM-HPC module and carrier board design verification or design services, as required. ADLINK can also provide software, firmware, and BIOS adaptation services to suit customers’ specific requirements, and ADLINK’s customers can take advantage of local and global networks of ADLINK support centers located in all major geographic regions.
With top-class production and manufacturing logistics coupled with lifetime product stability, ADLINK’s COM-HPC solutions provide long-term availability; with extended temperature operation, mechanical ruggedness, and highly accelerated life testing (HALT), ADLINK’s COM-HPC solutions provide high reliability; and with the ability to provide hardware and firmware customizable services regarding specific customer applications, ADLINK’s COM-HPC solutions provide a high degree of flexibility.
In the next few years, COM-HPC modules will be deployed in myriad diverse locations and environments to perform a vast array of applications—all designed to make our lives better—and ADLINK will continue to be at the forefront of this exciting technology.