Use Jigs For Time Savings and Accuracy
December 02, 2016
Blog
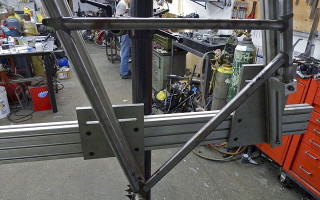
When I worked as an engineer in manufacturing, an important part of my job was designing fixtures to help others do their job better.
When people assembling parts have to do a job hundreds of times a day, having a proper method to hold the part they are working on can be quite important. Fixtures, or “jigs” as they are often called, can increase speed, accuracy, and comfort of a job. Unfortunately, this is something that I, and I’m sure many others, tend to neglect as a MakerPro. After all, I usually don’t have hundreds of similar items to make, so when I do face a situation where making a jig might be beneficial, it’s not necessarily the first thing I think of. It’s easy to just start doing something, but it could be well worth taking some time to make your job easier.
One example I ran into recently was that I needed to put a hole through the center of eight aluminum plugs. Accuracy didn’t have to be spot-on, but even a relatively small deviation would mean it wouldn’t look great, and a larger deviation could affect performance. To this end, I made a jig that fit in my milling machine’s vise, and once I drilled the first plug, further plugs could be duplicated.
Making a custom jig can be kind of a fun project in itself, since much of the time it’s something unique. In this case, this took the form of a rectangular piece of aluminum with a hole about the size of the plug and slots cut so that it could compress like a spring, as you can see in the pictures below.
[The plug fixture]
[The plug fixture in use]
[The result, drilled, tapped, and inserted into carbon fiber rods]
This is just one example, though. Jigs can be made for nearly any type of repetitive work, whether it’s welding, machining, soldering, or even placement of electrical components. Though “jig” generally refers to a simple device or fixture used to help with mechanical assembly, the concept could even be carried over into programming macros on your computer or custom software used to automate tasks that could be done by hand.
One thing to consider before making a jig is whether or not someone has already made the same sort of fixture. The best-case scenario is that you can buy something that will save you the time of making it. Even if you don’t find what you’re looking for – or don’t want to spend the money – there’s a chance you’ll see something else that inspires your final design.
Someone once told me that you should spend half your time making jigs and half your time actually making the final product. That seems a little extreme, so perhaps I’m remembering what he said incorrectly, but it’s good to at least consider what you’re doing from time to time and ask if it can be done better. It might be frustrating to take detours on the path to a final product, but sometimes the time saving and accuracy benefits are well worth it.