Top-Notch Manufacturing: A DFI Factory Tour
July 11, 2024
Sponsored Story
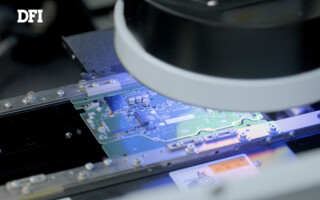
One of the best parts of my job is seeing products we write about being manufactured, whether it be semiconductors, boards, systems, tools, and so on. In many cases, we have to take the manufacturer's word. We can follow up with customers and suppliers, and we do, but seeing the manufacturing actually taking place, and watching the products roll down an assembly line is quite gratifying.
On my recent trek to Taiwan, I received a factory tour at the DFI facility, and it did not disappoint. One thing that was interesting, but probably shouldn’t have been, is that manufacturing doesn’t change much, even when you’re in a different part of the world. In the case of DFI, a producer of long-life embedded solutions, industrial motherboards, and custom products, they can crank out just as many boards and systems as any top-end producer, with the quality to match. But I’m getting ahead of myself.
Our tour was conducted on a rainy day, which I later learned is a regular occurrence at this time of year, aka the rainy season. The tour was led by Gavin Chan, DFI’s General Manager, at its Operations Management Center (OMC), who first provided some of the vitals of the company. DFI was founded in 1981 and is now part of the Qisda Group. It employs about 700 people in its Taiwan location, and about 1400 worldwide. All of the company's manufacturing takes place in Taiwan. From a geographical perspective, its business is spread nicely across the globe, with about 40% in Europe, 30% in the U.S., and 30% in the rest of the world.
Principles of the OMC
Chan walked us through the organizational culture of its Operational Management Center, which follows four principles that work toward the best culture and value: cost, quality, efficiency, and capacity. These guiding principles result in a maximum production of 200,000 boards and 70,000 systems per month, using five SMT (surface-mount technology) lines, two MI (manual insertion) lines, an X-ray component counter, and 56 test stations.
DFI differs from some of its competitors by employing an agile approach to manufacturing. This helps them adapt very quickly to changing market conditions, technology advances, and customer needs. It involves the supply chain and its own internal logistics. To that latter point, DFI makes use of advanced analytics and automation, and they form strategic partnerships with both their suppliers and their customers to leverage complementary strengths and synergies. As Chan pointed out, “Using analytics, we can turn obstacles into opportunities and respond to material shortages quickly.”
ESG principles are core to the DFI manufacturing process, with a goal of producing eco-friendly products and services. It does this by focusing on sustainable practices, such as reducing carbon emissions and waste, utilizing energy-efficient technologies, and ensuring responsible sourcing of materials. It emphasizes social responsibility through safe working conditions and community engagement. Governance is strengthened by maintaining high ethical standards, transparency, and robust compliance with regulations. This holistic approach aims to create long-term value while minimizing environmental impact and promoting social welfare.
Robots Zipping Around
DFI’s automated storage retrieval system was fun to watch. It fully automates the production and material kitting process, significantly improving efficiency and accuracy. At the same time, it maximizes the space within the factory floor. Basically, the system consisted of a series of robots, that quickly pulled things from shelves and replaced things in other places, far faster and more efficiently than would be possible by a human. And it has no downtime. When the robots need to be charged, they move themselves to the charging stations automatically (with no complaints!).
We also witnessed ultra-fast pick and place machines and a room dedicated to wide-temperature burn-in, with testing of boards in a range of -40ºC to +85ºC. In addition to efficiency and precision, the factory featured a rigorous inspection process. That has resulted in a FPYR (first pass yield rate) of 99.6%.
The bottom line is that DFI may not be the largest supplier out there, but they can design and manufacture industrial motherboards and systems with the best of them.