Developing embedded systems with discrete high-performance graphics processors
June 01, 2014
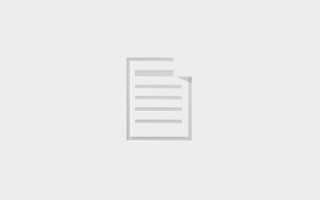
Designing a discrete graphics-processor-based system for embedded applications presents very different types of challenges when compared to more mains...
Designing a discrete graphics-processor-based system for embedded applications presents very different types of challenges when compared to more mainstream discrete graphics, especially as the systems are often used in domains like industrial automation, in-the-field digital signage, medical imaging, and casino gaming. Embedded systems such as these often must withstand extreme temperatures, and meet additional shock and vibration, cooling, and lifecycle requirements.
The three standard embedded graphics board formats – Multi-Chip Module (MCM) mounted directly on a motherboard, Mobile PCI Express Modules (MXM) connected to motherboards, and Peripheral Component Interconnect Express (PCIe) graphics cards – each present their own unique design considerations, and many applications have their own unique requirements and challenges.
High-performance 3D graphics and compute performance
Today's embedded applications feature high-performance 3D graphics and compute capabilities not found in older solutions. For example, operators in an industrial manufacturing facility are constantly monitoring processes on systems that have changed from static, text-based displays to more elaborate and intuitive 3D graphic representations. Casino gaming solutions now require more processing power and immersive 3D graphics to capture players' attention. Advanced discrete graphics processors now support multiple displays with improved 3D and video performance, which is essential for many industrial shop floor monitoring applications and casino gaming machines.
The medical imaging industry is also moving quickly to embrace 3D visualization at the point of care. For example, where dentists previously provided diagnoses and treatment recommendations made on the basis of static renderings on conventional 2D X-ray film and light-box illuminators, dentists and their patients can now have a much clearer view of teeth and gums with a new generation of video- and graphics-optimized 3D touchscreen panels attached to dental chairs.
Graphics processor options
Developers who want to deliver high-definition visual experiences such as these in compact, power-efficient embedded systems can leverage the parallel processing performance of GPUs. Some GPUs integrate on-chip memory, eliminating the need for external graphics memory, which further reduces the complexity of PCB design and layout, memory tuning, and memory procurement logistics. GPUs can support 3D Application Programming Interfaces (APIs), such as OpenGL ES, and hardware-based video compression and decode. Developers can also have more flexibility if the graphics processor supports a wide variety of industry-standard operating systems, including VxWorks, Green Hills, and Linux.
The AMD Embedded Radeon E8860 GPU, introduced in February 2014, is an example of a GPU that offers these features to help developers deliver desktop-caliber graphics from small, embedded systems.
Design implementations
How a developer decides to implement discrete embedded graphics solutions will often depend on how much shock and vibration the application will receive, as well as upgrade requirements.
The most ruggedized and perhaps smallest of all the design options is the MCM. An MCM is comprised of a discrete graphics semiconductor die and memory packaged on a single substrate, which is mounted directly on the motherboard. MCMs take up less real estate on a PCB (33 mm x 33 mm), allowing for an optimal, low power, compact design. MCM solutions are usually the best choice for ruggedized environments because the graphics chip is mounted on the motherboard and is therefore very secure for applications that must deal with shock and vibration.
From a design perspective, using an MXM solution offers developers added design flexibility over the MCM solution. MXM was originally designed to create an industry-standard socket for laptops to ensure that users could upgrade their graphics processors easily, without having to buy a new system. MXMs connect to the motherboard via a specialized MXM interface, and are smaller than typical PCIe cards. However, from a design perspective, the interface and module take up more space on the motherboard when compared to an MCM. The advantage of this solution is that it is interchangeable. Developers can replace it with a higher-performing model at a later time or create customized versions.
MXM solutions are not as ruggedized as MCM solutions; there are degrees of movement possible, but because the MXM is contained in a fairly small package, it is less likely to shift. However, the MXM module can be physically secured to the motherboard to accommodate shock and vibration.
Developers typically choose a PCIe solution as an option when they want high-end graphics like higher-resolution 3D rendering or video playback, and additional display outputs (six or eight displays up from two or three). The card connects to a PCIe slot on the motherboard and is physically the largest of the three options at 6.5" to 13" long. It is also heavy, typically twice the weight of an MXM or MCM and up to five times heavier at several pounds, and therefore may have problems with shock and vibration. Designers developing a system that has the potential to be deployed in stressful environments should ensure a solid fit to minimize excessive vibration and should work to identify stress points.
Extreme temperatures, cooling, and lifecycle requirements
After shock and vibration, the remaining variables span all three design architectures: extreme temperatures, cooling, and lifecycle requirements.
Extreme temperature standards for systems operating in harsh environments are -40 °C to +120 °C. Designers should ensure that their GPU vendors' processors meet those standards, which implies an additional level of testing and qualification beyond the standard 0 °C to +105 °C.
Designers can cool GPUs by attaching an active fan or by using a passive heatsink to dissipate heat. Either solution can require specialized versions that must take into account the system's environment. If it disrupts the airflow design, an active solution may not be possible. A passive solution that requires a specific airflow at a specific temperature may not cool a graphics device enough. Sometimes a custom solution will be necessary, such as when a passive heatsink needs to connect physically to the metal case of the system to use the greater metal surface of the system as a cooling medium.
While standard consumer graphics systems may last a few years, many embedded projects have lifecycles of 7-10 years. That means parts must also be available for an extended period of time. Some GPU vendors – such as AMD – offer extended longevity for embedded parts. Without such support, designers need to take inventory of their parts and maintain them in special storage to ensure long-term viability (and they must also plan for potential yield loss).
It's a graphical world
Embedded discrete graphics solutions have advanced tremendously, based on technology that originated from mainstream commercial graphics solutions. For some applications – such as digital signage, medical imaging, and casino gaming – they must perform in some fairly challenging environments. With the right design choices, developers can create a new breed of embedded systems that provide the next generation of amazing 3D graphics.
AMD www.amd.com
@AMDRadeon
www.linkedin.com/company/amd
plus.google.com/+AMD
youtube.com/user/amd
community.amd.com