The Future Vehicle is Optical
September 25, 2023
Blog
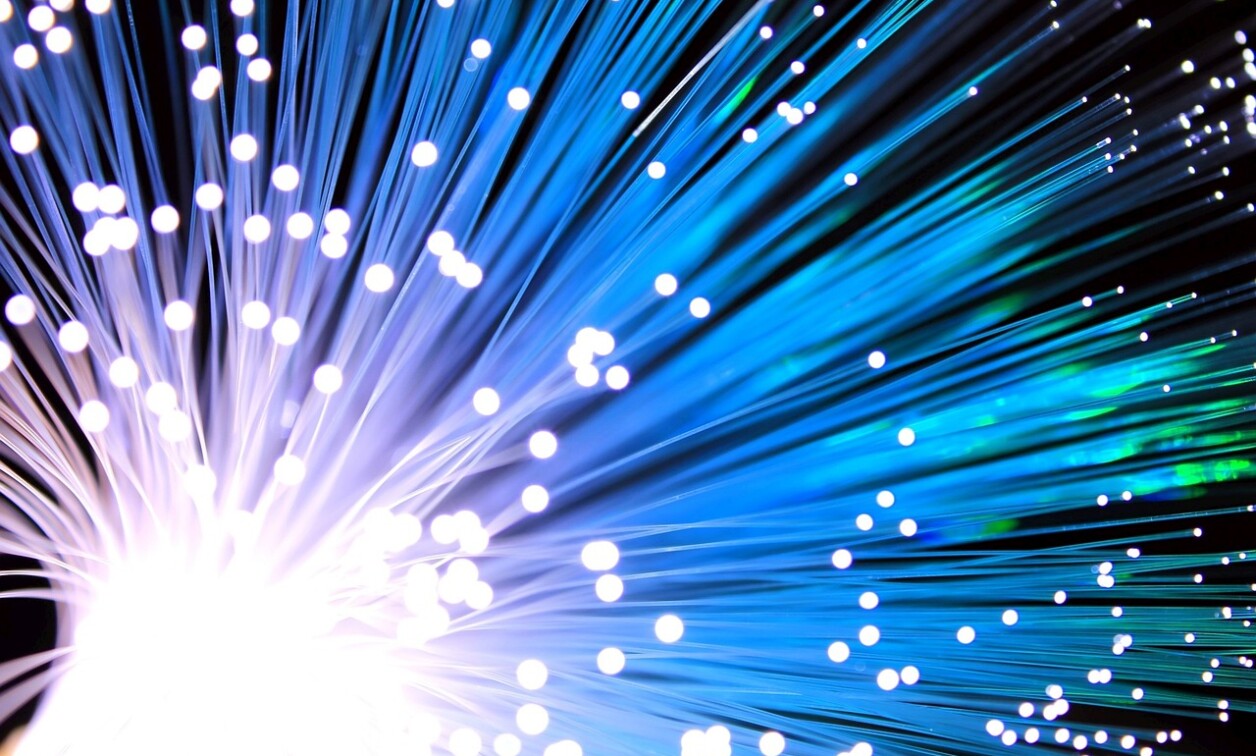
As the challenges of multi-gigabit increase, costs should not increase at the same scale. Optical provides a low-cost, robust, and reliable solution for the in-vehicle wiring system. Optical’s EMC superior performance prevents the need for heavy, bulky, expensive cables with rigid and age-prone shielding. The inherent galvanic isolation of optical fiber solves the ground loop issues and the return currents through cable shielding.
Optical performance allows 50 Gb/s over 40 meters with enough margin for in-line connectors, which enable long-link applications, such as for buses and trucks. Optical transceivers will support asymmetric links as well, for camera, radar, and sensor applications with MIPI+ return channel interface. The optical harness will be the same for all the multi-gigabit rates: 2.5/5/10/25/50 Gb/s, which makes optical a scalable solution. Finally, optical connectivity allows multi-port and waterproof connectors, and optical cables can be installed in the same assembly process as the rest of the copper cables.
Automotive Network Demands
With technological leaps such as electrical vehicles, automated driving, and V2X interconnection rushing through, automotive applications, utilization, and safety requirements are boosting the necessary network speed. In-vehicle networks are on the brink of speeds from one to multiple gigabits per second. As the auto industry targets the 100 Gb/s*m speed-length threshold, issues such as electromagnetic interference, electromagnetic susceptibility, cost, and weight reduction are becoming more and more serious.
For data transmission rates above 100 Mb/s, commonly used copper links need heavy and expensive modifications to comply with the stringent OEM’s EMC specs, resulting in high cost and very difficult engineering. Moreover, the weight of the ever-growing diameter of the required cables plays against the race for increased range in electrical powertrains.
The need to move from copper to optical physical transmission media is becoming evident. The key advantages of the optical solution, among others, are superior Electromagnetic Compatibility (EMC) thanks to the inherent galvanic isolation, low weight, and low cost.
The optical cables are absolutely reliable, and much more flexible than shielded copper cables. They allow fast, dynamic, and tight bending as well as immersion in dark liquids. Additionally, optical Ethernet generates very low noise and can operate in noisy environments, such as in RF electronic boards.
With optical and copper in parallel, the optical network provides ASIL-D safety architecture (ASIL-D = ASIL-B + ASIL-B). It guarantees easy engineering for seamless implementation. Overall, optical is the engineering-wise path for higher data rates.
Complete Communications System
Several industry leaders are working on an optical automotive multi-gigabit system that will fulfill the needs of future connected and automated vehicles. Instead of various port components, the upcoming solution provides a single, complete package. The new connector systems are very small, lightweight, and extremely inexpensive compared to the previous ones.
With cost-down and consistency in focus, optics, fibers, connectors, and electronics already developed for nGBASE-SR will be reused. Further specifications include 980 nm VCSEL (Vertical-Cavity Surface-Emitting Laser), multimode OM3 fiber, PAM2 receivers, and connectors.
Standardization work focuses on the automotive requirements: VCSEL reliability for the operation temperature range, connector development with quality grades, and an adaptive DSP to cope with the large parametric deviation of the VCSEL. Eventually, increasing the yield percentage results in cost reduction.
Complexity stays low with simple modulation. For fiber, the OM3 class is chosen since it is already extensively used by data centers and avionics. Only massive economy-scale light sources will be selected. Two connector grades are defined in order to allow cost-effective implementations.
Regarding topology, asymmetric up and down links have been considered from the beginning. The use of the Energy-Efficient-Ethernet (EEE) specification is an appropriate candidate to implement this feature. Cameras, displays, sensors and further asymmetrical use cases have been included as test cases for standardization. An OAM side-channel will be available for dependability and link management. The absence of retransmissions means controlled latency for video distribution. Symmetric links will be added for backbone communications.
The proposed multi-gigabit system wakes up in less than 100 ms. The target BER is better than 10-12 with ambient operating temperature ranging from -40 ºC to 105 ºC (AEC-Q100 grade 2) in harsh automotive environments. Meeting OEM reliability requirements, high reliability (15 years operation) and outstanding EMC compliance are also fulfilled. The technology in development is based on advanced digital signal processing, using high-speed DAC and ADC to implement all needed algorithms such as equalization or pre-coding.
VCSEL Operation
A key component for this communication system is the light source. The Vertical-Cavity Surface-Emitting Laser is the device that best fits the high speed and low-cost requirements of the application. The technology of the VCSEL device is well-known, mature, and optimized, already heavily used in two killer applications, optical sensors for mobile phones and data center communications.
The VCSELs used for the latter application can be leveraged for automotive communications, seizing on its already excellent cost and speed. However, VCSELs used in data centers live a more comfortable life than they will in a car. Reliable communication must be guaranteed in extreme temperatures ranging from -40 ºC to +105 ºC ambient temperature. Successfully using the VCSEL in automotive conditions means being able to compensate for its impairments at high temperatures.
The substrate of the VCSEL will reach an even higher temperature, so to have enough margin, a substrate temperature range of -40 ºC to +125 ºC is favored. The proposed system implementation can support VCSEL operation in this scope, and also takes into account the possible technology process variations amongst the different VCSELs manufactured.
Automotive VCSELs are not only required to live in a harsh environment, but they are also required to live longer. The automotive industry sets a very demanding objective for the reliability of electronic components, which can be summarized with a figure, 10 FIT (Failures In Time). This means that the failure rate expected for a component is at most 10 failures after one billion device hours, which for example can be expressed saying that no more than 10 out of 1000 devices can fail after one million hours of operation.
Guaranteeing a reliability figure like this makes it necessary to operate the VCSEL in less stressful conditions. There is nothing to do about temperature, but the VCSEL suffers less with a lower current density.
The problem is that the optical output power from the laser is proportional to the current, so reducing the current results in less optical power at the receiving end of the communication. On top of that, reducing the current density also results in decreasing the bandwidth of the VCSEL and increasing the Relative Intensity Noise (RIN). Therefore, we need to operate the VCSEL at the right balance of the lowest feasible current.
Multi-Gigabit Automotive Ethernet
The ecosystem for the proposed optical communications system already exists by leveraging well-proven technologies, such as VCSELs, multimode fibers, and photodiodes already developed for the data centers industry. Standardization processes are ongoing with IEEE 802.3 Automotive Ethernet and ISO PWI 24581 in progress.
The new optical automotive IVN communication standard IEEE 802.3cz (IEEE Standard for Ethernet Amendment 7: Physical Layer Specifications and Management Parameters for multi-gigabit glass optical fiber automotive Ethernet) has been released by the IEEE Standards Association (IEEE SA).
This amendment to IEEE Std 802.3-2022 adds Physical Layer specifications and management parameters for 2.5 Gb/s, 5 Gb/s, 10 Gb/s, 25 Gb/s, and 50 Gb/s operation on glass optical fiber in an automotive environment. The new standard is a major milestone for optical automotive multi-gigabit Ethernet. The 802.3 Task Force includes numerous individuals affiliated with key carmakers, such as PSA, Toyota, BMW, Ford, GM, and Volvo, Tier 1 suppliers, and components suppliers.
The IEEE 802.3cz-2023 (nGBASE-AU) standard has been designed from scratch with the goal of meeting stringent automotive requirements. The use of glass optical fiber improves power consumption. In addition, it is more resilient to aging problems.
It is absolutely future-proof since ECUs can be upgraded to higher speeds while keeping the same harness. As of today, the IEEE 802.3cz standard technology provides the only existing solution for 25 Gb/s and 50 Gb/s single lane connections with 4 inline connectors and a maximum length of 40 meters in the car over OM3 multimode fiber.
The standard specifies speeds of 2.5, 5, 10, 25, and 50 Gb/s per lane. It meets automotive temperature requirements of -40 °C to +105 °C and OEM reliability requirements with a minimum of 15 years of operation with 10 FIT.
The maximum link length is 40 meters with 4 inline connectors. The solution is affordable since the higher optical power budget allows lower tolerance connectors. Additionally, the OM3 fiber is widely used, ensuring high volume production. An almost ideal communication channel allows a much simpler physical layer with a lower DSP/equalization complexity and no echo cancellation, resulting in lower power consumption, lower latency, a smaller silicon area, and overall lower-cost solution. A specially dedicated Operations, Administration, and Maintenance (OAM) side channel is available for dependability and link management.