Design Reliability and Efficiency into Smart HVAC Systems
July 25, 2022
Blog
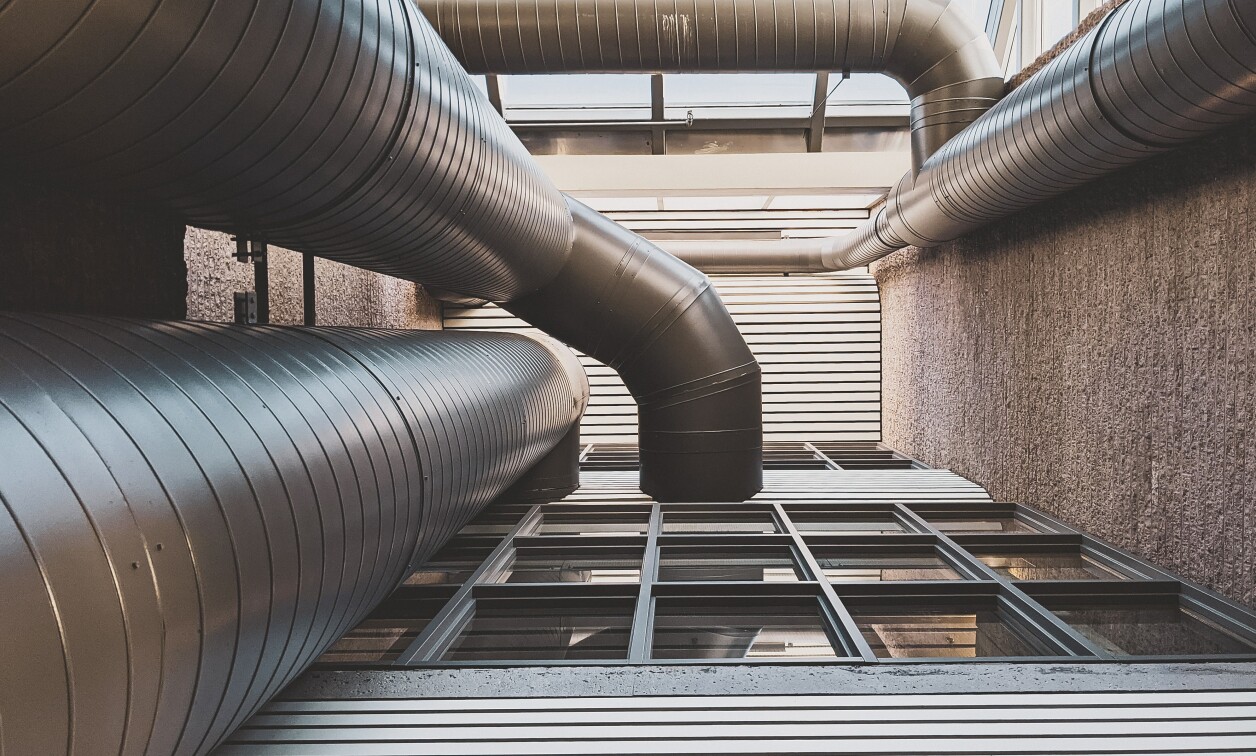
The heating, ventilating, and air conditioning (HVAC) market is growing at a 6% compound annual growth rate as annual shipments of AC systems are expected to grow from 110 million units in 2020 to 140 million units in 2024.1 Large commercial systems will have the highest growth rate resulting from the construction of new healthcare, education, warehouse, government office, and retail facilities.
The majority of the systems in these new facilities will be smart HVAC systems due to government-driven initiatives to reduce energy consumption and improve indoor air quality. Improvement in air quality contributes to a healthier environment, reduces occupant fatigue, and improves worker productivity. Thus, new smart HVAC systems must minimize energy consumption while maintaining a healthy environment, maximizing energy efficiency while ensuring system reliability.
Designers have the challenge of developing smart HVAC systems that are both energy-efficient and robust enough to overload and transient strikes such as lightning-induced surges, electrostatic discharge (ESD), and other AC-line transients. The following paragraphs will offer designers of smart HVAC systems guidance on protection, control, and sensing components for incorporation in their designs to achieve efficiency and reliability. Figure 1 shows an example of a smart HVAC system in a commercial building.
(Figure 1. Example smart HVAC system in a multi-story building)
Figure 2 pictures a commercial rooftop HVAC unit and highlights the major sub-system circuit blocks. Each block lists the recommended protection, control, and sensing components that will ensure safety and robustness to overload and transient strikes while offering energy efficacy.
(Figure 2. An example commercial HVAC system showing the recommended protection, control, and sensing components needed to ensure a reliable and efficient system)
Protecting an HVAC system and minimizing its power consumption
Figures 3 and 4 show a representative block diagram of a commercial HVAC system’s circuits. The block diagrams for the two figures are identical, but the recommended components in each figure apply to different circuit blocks. Figure 3 details components for the Control Unit, and Figure 4 lists components for the other circuits.
(Figure 3. HVAC block diagram showing the recommended protection, control, and sensing components for the Control Unit)
Control Unit protection and safety components
The Control Unit draws power from the AC mains and provides the power to control motors and all circuit blocks. The AC mains, which can be either single-phase or 3-phase, provide the power to the Control Unit. As a result, the Control Unit is subject to overloads and transients originating on the AC mains.
Start with a fuse to protect the Control Unit from current overloads. Since the HVAC system is powering motors, the fuse must withstand inrush currents drawn by the motors. A time-delay fuse, preferably a two-element fuse, will avoid nuisance failures due to motor inrush current. A two-element fuse allows safe sizing for overload circuit protection while supporting the momentary high inrush current. If a circuit breaker is under consideration, realize that fuses operate faster than circuit breakers; fuses do not require maintenance testing or calibration. Ensure that the selected fuse has a voltage rating higher than the maximum operating voltage of the Control Unit circuit. With 600 V ratings, nominal fuse current ratings can be as high as 1200 A to meet the requirements of large HVAC systems. Select a fuse with a high interrupting rating so that the fuse will open and interrupt the worst-case overloads. Fuses for this application have interrupting ratings of 200 kA. Finally, if circuit board or panel space is a concern, look for a fuse that will meet the electrical requirements and have the smallest possible package size.
High voltage transients can induce a wide range of high voltage disturbances on AC lines. Consider a surge protector to guard against lightning strikes which are fast high voltage and high current transients. A surge protector is comprised of a metal oxide varistor (MOV) with a series thermal detector in each AC mains line. A surge protector can safely absorb a transient as large as 40 kA and respond to the overload under 25 ns.
The sensitive electronic circuitry in the control panel needs protection requiring that transients be clamped to a safe voltage level. Investigate using a bidirectional protection thyristor in series with an MOV. The MOV can absorb peak surge currents as high as 10 kA or with energies as high as 400 J. The thyristor has a crowbar-type response and can handle large surge currents while maintaining a low clamping voltage.2 Adding an MOV with the thyristor allows the use of an MOV with a low clamping voltage. The combination offers enhanced safety for downstream electronic circuits. The thyristor-MOV combination has a lower leakage current than an MOV by itself and contributes to reduced energy consumption.
Note: For more information on the surge protection provided by a thyristor-MOV combination, see the application note, High Power Semiconductor Crowbar Protector for AC Power Line Applications, courtesy of Littelfuse, Inc.
Fast transients can still propagate into the transformer's secondary—a transient voltage suppressor (TVS) diode on the secondary side of the transformer clamps these transients. TVS diodes also provide electrostatic discharge (ESD) protection by safely absorbing 15 kV strikes through the air or 8 kV strikes from direct contact. In addition, TVS diodes have extremely fast response times of under 1 ps.
HVAC motor protection
Protect the high-cost HVAC motors by monitoring voltage, current, and motor cycling intervals.
- Monitoring motor voltage: Use a three-phase voltage monitor that shuts off power to the motors if the monitor detects voltage unbalance, high voltage, or phase faults.
- Monitor motor current: Use a current monitoring relay with a magnetic sensor and outputs to feedback motor current draw to the control electronics. The magnetic current sensor is not in the power delivery circuit and avoids power loss in that circuit.
- Prevent short cycling of the motor: Use a time delay relay to guard against the motor re-starting too quickly (short cycling) after being de-energized. Time delay relays also can allow sequencing when multiple motors must be powered in a fixed order. Choose a solid-state time delay relay for long operating life. An encapsulated package maximizes operating life by avoiding shock, vibration, and humidity degradation.
Noise and transients generated by motors can interfere with the electronic control circuitry. Consider isolation switches to energize motors. An optically isolated switch with zero-crossing activation minimizes the generation of transients during motor turn-on.
With all the circuitry and the high power in the Control Unit, ensuring the system cannot operate without a closed control panel door is essential. A reed proximity switch senses the position of the door and prevents personnel from accidental contact with high voltages. Choose a reed sensor model with appropriate sensitivity. Maximize sensor life by using a hermetically sealed model which avoids contact contamination.
Use contactors to switch power to the Control Unit's circuit blocks and the motors. Ensure contactors are appropriately sized to support the motor horsepower load. Look for contactors whose contacts have high electrical conductivity and resistance to contact oxidation, which degrades the life of the contactor.
Add capacitors to the motor drive lines for power factor correction. This also reduces system power consumption. Ensure that the capacitors conform to UL standard 810 and EIA standard RS-456. Look for long operating life for maximum system reliability.
Step down and isolate AC line voltages with transformers to generate control voltages. Select UL and CUL standard 5085-recognized components.
(Figure 4. HVAC block diagram showing the recommended protection, control, and sensing components for the other circuits)
Rectifier protection and high-efficiency components
The rectifier circuit converts the AC mains voltage to DC voltages which power the inverter and the communication and control circuits. Use rectifiers with low forward voltage and low reverse leakage current to minimize energy lost in the rectifier. Low power-consuming rectifiers generate less heat and require smaller heat sinks, saving cost and circuit board space. Power rectifiers are available in a single package to save even more space. Figure 5 shows an example of a 3-phase rectifier package.
(Figure 5. 3-phase package of rectifier diodes)
Inverter sensing, protection, and high efficiency components
The Inverter converts DC voltage to the AC voltage required to drive the motors. This power circuit needs to be both efficient to minimize power consumption and robust to current overloads and transients. Consider using insulated gate bipolar transistors (IGBTs), which have fast switching times to reduce power loss during transitions between the on and off states. Select IGBT transistors with VCE(Sat) under 2 V and gate leakage current under 1 µA for maximum efficiency. Three-phase IGBT modules in half-bridge configurations are available in a single, space-saving package. The three outputs have near-identical characteristics, which simplifies control requirements. See Figure 6. Consider using gate driver chipsets to control the IGBT modules. Gate drivers provide rise times under 20 ns to facilitate efficient, fast switching of the IGBTs.
(Figure 6. 3-phase half-bridge IGBT power transistor module with built-in temperature sensor)
The high-speed switching of an IGBT reduces power consumption; however, its turn-off transient voltage can exceed the transistor’s ratings and damage the IGBT. Using a TVS diode between collector and gate can clamp the transient and raise the gate voltage relative to the collector voltage. This slows the rate of rise of the transient voltage. Insertion of a TVS diode between collector and gate of an IGBT is a protection technique known as active clamping. See the referenced application note for more details on the benefits of active clamping for IGBT protection.3
Employ a negative temperature coefficient (NTC) thermistor if the selected IGBT chipsets do not have an internal thermistor for monitoring temperature. Power semiconductors can be subject to thermal runaway if their junction temperatures exceed their rating. Ensure that the external thermistor has sufficient range to monitor the highest temperature that the IGBT could attain. When using individual IGBTs in TO-style semiconductor packages, thermistors are available with lugs that mount directly on the package.
Protect the Inverter circuit from short circuit conditions with a fast-acting fuse. Appropriate, high-speed fuses will open in response to a 400% overload in under a second to protect the semiconductors. High-speed fuse models for protecting power circuits have current ratings up to 800 A with voltage ratings of 750 V.
Communication Interface ESD protection components
The Communication Interface links wirelessly to the thermostats. Since the Communication Interface is exposed to the external environment, provide protection from ESD with a bi-directional TVS diode which will absorb an ESD strike of either polarity. Select a diode rated to withstand as much as ± 15 kV through the air and ± 10 kV from human contact. For minimal impact on the wireless transmission and reception integrity, use a TVS diode with capacitance under 1 pF.
User Interface ESD protection components
If operators’ interface with the system through a touch screen interface, consider a polymeric ESD suppressor to protect the Wi-Fi chipset from ESD. A polymeric ESD suppressor responds to a transient in under 1 ns. Look for models with leakage current under 1 nA to minimize power draw. Also, select ESD suppressors with low capacitance, under 0.15 pF, so that signal communication is not distorted. Ensure choice of a model rated for high levels of air and direct contact ESD protection.
Analog Front End protection components
The Analog Front End communicates with the power utility over the AC mains via power-line communication protocol. This circuit needs protection from voltage transients induced on the power line. Consider a high power TVS diode that can absorb up to 15 kW of peak pulse power.
Applicable Standards
Table 1 provides a list of important safety standards for industrial control panels, HVAC systems, and ESD protection. Plan for compliance to these standards in the early stages of development projects. Revising a design following a failure uncovered by a certified testing lab adds to project costs and delays product introduction.
(Table 1. Applicable standards for HVAC systems, industrial control panels, and robustness to ESD)
Value of a robust and power-efficient design
Designers can cost-effectively develop a robust and reliable HVAC system by including protection and sensing components as a design objective and incorporating standards compliance early in the project. Using efficient control components can facilitate development of a low power consumption product. Save precious development time by taking advantage of component manufacturers’ engineering expertise when selecting protection, control, and sensing components. A manufacturer’s application engineers can assist with selecting components that comply with applicable standards. Some manufacturers can assist with pre-compliance testing to help designers reduce compliance testing costs. Reliability and efficiency enhance the reputation of an HVAC system leading to growth in market share and revenue.
References
1 HVAC System Market - Global Forecast to 2023. MarketsandMarkets. April 2018.
2 High Power Semiconductor Crowbar Protector for AC Power Line Applications. 2020 Littelfuse, Inc.
3 Application Note: Using High Voltage TVS Diodes in IGBT Active Clamp Applications. 2020 Littelfuse, Inc.
Additional References
- Circuit Protection Selection Guide, 2020 Littelfuse, Inc.
- Sensing Products Selection Guide, 2019 Littelfuse, Inc.
- HVAC Selection Guide: Protect and Control the Critical Components in Your HVAC Systems, 2021 Littelfuse, Inc.
- Building & Home Automation Application Guide, 2020 Littelfuse, Inc.