FPGAs power instant-on embedded display systems
November 01, 2008
Story
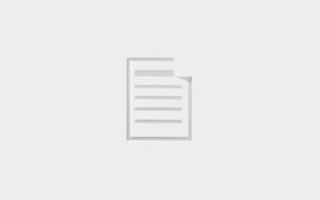
Nonvolatile FPGAs give designers the flexibility to offer quick and inexpensive support for current and future graphical display systems.
Embedded systems development teams are increasingly confronted with the challenges of designing instant-on display systems to support end-user requirements. Kerry explains how using nonvolatile FPGAs in embedded designs can help improve system startup speed, integration, security, and component end of life.
Graphics and video display system usage continues to grow, fueled by declining display prices and burgeoning user expectations. Unlike the PC and consumer markets, which are the largest users of display systems, the embedded market has several specific requirements for display systems, including:
- The ability to add intelligence to products. Users have become more sophisticated and expect advanced features.
- The flexibility to adapt to new and evolving standards, especially in regard to system interfaces and different display types and resolutions.
- Viability for 10-15 years. Component end of life requires costly product redesigns.
- Fewer devices needed per design, reducing costs and lowering power requirements.
In addition, many embedded systems must provide immediate information within microseconds of power-on. These systems require many components, which raises costs and lowers reliability. Furthermore, embedded displays based on multichip systems are relatively slow to initialize and display useful information.
While cell phone users may not mind the process of holding down the power button for two seconds and then waiting several more seconds for the system to boot, users that demand instant-on embedded display systems will not tolerate such delays. For example, consider the Ferrari 599 GTB Fiorano, which is equipped with an LCD instrument cluster. It’s doubtful that the driver of this $300,000 automobile would be willing to wait 30 seconds while the processor and graphics system initializes before the display can provide data such as speedometer values or oil pressure. In other applications such as an aircraft cockpit or nuclear power control system, startup delays can be disastrous.
Graphics system implementation overview
As shown in Figure 1, a graphics or video controller system contains several components with different inputs consisting of 7:1 LVDS, Camera Link, Channel Link, USB, RGB, video decoders, and system buses. The system also contains some external memory for storing page and video information.
Signals are processed by a general-purpose processor or sent directly to the graphics processor, which may be an Application Specific Standard Processor (ASSP), custom ASIC, or FPGA. Depending on the system, multiple displays might require additional logic to manage the signal information for each display.
Almost all ASSP systems are targeted to the PC and consumer markets and thus sometimes conflict with the needs of the embedded market. PC and consumer products typically have a short life cycle, and product developers anticipate using the latest technology. In contrast, products in the embedded market have very long production and support requirements that cannot tolerate changes forced by a graphics processor end-of-life situation.
FPGAs in embedded systems
Because FPGAs are not specific to the PC or consumer markets, they provide the necessary performance, functionality, and extended life cycle for embedded systems. Using FPGAs, designers can create modular designs that offer the flexibility to integrate different IP blocks, depending on the cost and feature requirements. FPGAs also allow designers to include custom graphics accelerators within the video controller so that graphics performance can be optimized specifically for the target system.
Standard video and graphics IP cores for FPGAs are verified designs that are easy to integrate into an embedded graphics display. IP cores also speed system development, enabling designers to concentrate on the application instead of the interface and graphics engines. Furthermore, FPGAs can include the optimal bus and interface standards, allowing designers to choose the best interfaces for the system rather than designing around a predetermined graphics processor interface or bus.
Flash and SRAM unite
Most FPGAs use SRAM technology and lose their configuration during power loss. However, these volatile SRAM FPGAs historically have had higher logic densities and operating speeds than nonvolatile FPGAs. Until recently, the advantages of SRAM FPGAs usually have outweighed the benefits of nonvolatility. That now has changed with the introduction of flash and SRAM FPGAs that provide the best of both worlds: nonvolatile devices with all the features and performance of high-end, System-on-Chip (SoC) FPGAs.
"Instant-on" in programmable devices refers to an FPGA’s ability to autonomously configure itself and activate almost immediately. This is possible only in FPGAs that include configuration startup memory inside the device. At power-up, data is transferred from the on-chip flash memory to the SRAM configuration cells that control the device. The key to the instant-on feature is a massively parallel programming data transfer from the flash configuration memory to the SRAM configuration memory.
This instant-on ability is the direct result of a single-die FPGA. The flash configuration memory and SRAM configuration memory are integrated onto the same die, so the parallel load is very quick. The time from achieving VCC to activating the outputs is less than 2 milliseconds.
A modular FPGA-based graphics and video processing IP system design includes a 2D graphics accelerator, video input module, picture-in-picture, scaling, cropping, and positioning, as shown in Figure 2. Project applications operate on the host soft processor that resides in the FPGA. This host processor generates the rendering commands and passes them to the video IP, which also resides inside the FPGA.
Various I/O interfaces are integrated into the FPGA using the built-in I/O support and commercial IP (see Figure 3), and the host CPU is integrated using a 32-bit RISC soft processor core. The graphics and video controller IP includes support for multiple displays and video standards as well as touch-screen feedback.
Additional system features support embedded applications such as remote client devices, including PCs and cell phones that can connect to the application host processor and remotely review and control the same application as on the local display.
Flexible designs advance display technology
It is possible to integrate almost the entire graphics system into a nonvolatile FPGA. With a very long life cycle, in-system field upgradeability, and adaptability to different buses, interfaces, and displays, this system meets the embedded market’s requirements for an instant-on, highly reliable, secure display.
Nonvolatile instant-on FPGAs allow quick design changes during development and throughout the product life cycle. Integrated graphics functions inside this type of FPGA provide designers with the flexibility to offer quick and inexpensive support for current and future graphical display systems. Powerful graphics/video IP coupled with easy-to-implement FPGA SoCs fulfill the market’s need for a modular, flexible, and expandable embedded display system.
Lattice Semiconductor
503-268-8000
kerry.howell@latticesemi.com
www.laticesemi.com