Tear Down: Garmin Forerunner 230 GPS Running Watch
March 07, 2016
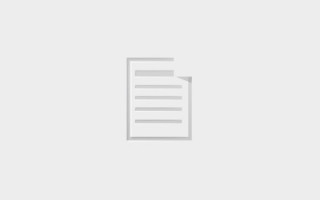
Garmin manages to get the maximum performance from the ARM M4 processor without requiring users to lug around a battery pack. Fitness trackers are amo...
Garmin manages to get the maximum performance from the ARM M4 processor without requiring users to lug around a battery pack.
Fitness trackers are among the most popular wearable devices that are also associated with the Internet of Things. At the same time, they’re among the most popular devices for yours truly, who may be one of the pickiest consumers you’ll come across. I’ve been through more than my share of fitness trackers, and the last two I’ve actually ripped apart.
The Misfit Shine 2, in my opinion, represented a really good engineering design, but not the perfect end product. Unfortunately, the subject of my current Tear Down, the Garmin Forerunner 230 running watch (Figure 1), falls into a similar category. From an engineering perspective, the designers have done a masterful job. But the end-user experience leaves a little to be desired. Thankfully, I’m not here to judge the product’s usability. I leave that to the real product reviewers.
Having performed Tear Downs for the better part of a couple of decades, I’ve seen my share of really good designs, and I’ve also seen enough kludges to wonder how some of these engineers got as far as they did.
But back to the Garmin Forerunner 230. At the core of the system is an Atmel Smart SAMG53 microprocessor (Figure 2), which is built with an ARM Cortex-M4 core and a floating-point unit (FPU). The SAMG53 has been in production for about 18 months. While that provides the compute power needed by the Garmin, the real reason they chose the Atmel part had more to do with low power consumption.
With the FPU, you can minimize the active-mode power consumption and get the core into its sleep mode faster, which is the best way to reduce power. As you know from previous Tear Down articles, running the processor at its maximum frequency for the shortest duration is the best way to minimize power. Fast wake-up, fast computation, and back to sleep, with SRAM retention, of course. It’s fully functional down to 1.7 V, including flash reads and writes and full ADC operation.
The G53 is similar to Atmel’s sister part, the G55, which is used in the next-generation Garmin platform. The G53 can keep the power down because it seems to have just the peripheral set necessary to do the job Garmin needs it to do, and nothing else. It has 16 DMA channels, which contribute to the high throughput. So it has what you need to talk to sensors and wireless and the SRAM. But because it’s not loaded with analog and other peripherals, Atmel can keep the cost down. The G55 part offers more SRAM and ups the frequency from 96 MHz to 120 MHz. If you prefer that part, it’s a fairly simple upgrade, as the two ICs are pin-compatible.
Atmel has an advantage when competing for Garmin sockets. The two companies have a fairly long history of working together. The G53’s launch coincided with the first conversations with Garmin regarding the Forerunner 230. Note that the G53 was also designed into one generation of Samsung’s Galaxy S4 phone, where it’s used for similar tasks as the Forerunner 230.
The GPS functionality on the Forerunner 230 is handled by a MediaTek MT3333 All-In-One multi-GNSS (global navigation satellite system) system-on-chip (SoC, see Figure 3). The part is generally found in mobile, automotive, personal tracker systems, and industrial applications. As you would expect, drones are also a very hot topic, and that’s a key placement area for the MT3333. It requires just eight passive external components and offers a high level of sensitivity, allowing it to operate in dense urban environments.
The Bluetooth connection is handled by a Nordic Semiconductor nRF51422 Bluetooth Smart transceiver. Also suited for ultra-low-power wireless applications like the Forerunner 230, the 2.4-GHz nRF51422 is built around a 32-bit ARM Cortex M0 CPU with up to 256 kB of flash memory and 32 kB of RAM.
The nRF51422 incorporates analog and digital peripherals that can interact without CPU intervention through its programmable peripheral interconnect (PPI) system. Its 31-pin GPIO mapping scheme allows serial interfaces, PWM, and a quadrature demodulator to be mapped to any device pin as dictated by the PC board requirements. This simplifies the placement and layout process.
Battery management falls under the purview of the Maxim MAX14676 battery-charge-management IC, which includes a linear battery charger, a fuel gauge, and several power-optimized peripherals. The integrated ultra-low-power buck regulator has a 900 nA quiescent current (typical) and has 74 percent efficiency with a 10 μA output. The MAX14676 comes with a synchronous high-efficiency step-down converter. It features a fixed-frequency PWM mode for tighter regulation and a burst mode for increased efficiency during light-load operation.
The MAX14676’s boost regulator and three programmable current sinks can be used to drive a variety of LED configurations. The boost converter is controlled independently from the current sinks, and they can be also used separately. In addition, a power switch controller allows the device to be turned on and off by a pushbutton. It also provides a delayed reset signal and voltage sequencing.
The MAX14676 also couples nicely with the MAX326 quad SPST ultra-low leakage analog switch. That helps the Forerunner 230 maintain the highest possible level of efficiency.
The relationship between IC supplier and OEM can take various forms. In some cases, the OEM wants all the help they can get. In other cases, they hold onto their IP as tightly as possible and don’t give the IC supplier even an inkling of what they’re working on. But most of the time, it falls somewhere in the middle, and that was the case between Atmel and Garmin. Looking at the design, it was clear that Atmel provided some of the low-level drivers for things like UARTs, I2C, and some other “bits and bytes level” of communications.
Looking at the main PC board, it’s also clear that best practices were followed. The radio ICs are separated from each other, and there’s nothing near the board’s edge that shouldn’t be there, thereby ensuring the highest possible production yields.