Next Level Electric: Connecting Electric Vehicles to the Cloud
March 08, 2022
Story
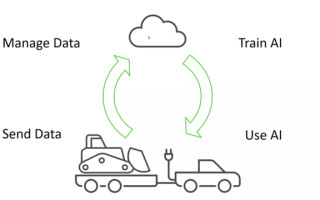
2022 might just be the year of EVs. And, of all things, cloud connectivity could be to thank.
Before the COVID-19 pandemic, Elektrobit began connecting EVs to the cloud as a means of capturing data that could inform the development of new automotive features. The solution enables OEMs to create applications leveraging vehicle data, and the EV-cloud scenario is just one example use case. As one real world example, the solution was built on sensors that collect vehicle data and AI models hosted on a hybrid cloud that predicted their performance in the field.
It consisted of a couple components, including:
- EB Assist Test Lab: A cloud-based data management tool that integrates with existing development environments to optimize data and storage resources, streamline workflows and interactions, and simplify data access.
- EB Assist Automotive Data and Time-Triggered Framework (ADTF): Both a development framework and interactive environment, EB Assist ADTF facilitates the vehicle data lifecycle, from logging to visualization, which even includes replaying data in cloud-based Hardware-in-the-Loop (HiL) simulations.
When the company started, they were passively collecting and processing automotive data from vehicles in the US, Germany, and Japan. However, the work evolved into a global collaboration between Elektrobit, Continental, and AWS to help automotive engineers gain deeper insights into the performance of equipment in the field.
Automotive Virtualized Reality
The solution gained a lot from the partnership, most notably access to Continental Automotive Edge (CAEdge) hardware, which helps aggregate vehicle information such as weight, number of axels, and tire specifications, along with any relevant sensor data.
CAEdge is a modular hardware/software automotive technology stack that combines a vehicle endpoint capable of running AI models with a cloud-based virtual workbench that can be used to develop, deploy, and maintain automotive software. Elektrobit operating systems (OSs), such as EB tresos for AUTOSAR Classic or EB corbos for Adaptive AUTOSAR, the Linux OS for Automotive, and others run on top of CAEdge to enable the capture, aggregation, and transmission of EV sensor data.
The cloud portion of CAEdge exists in an AWS EC2 instance, which is where the EB Assist Test Lab is hosted. The advantages here can’t be overstated, as the AWS infrastructure provides the parallel processing performance of entire server farms to accelerate the training of AI models or conducting advanced HiL tests. But outside of essentially limitless computing performance, the ability to pair with Amazon’s infrastructure also provides a hardware-less path forward for EV developers.
Not surprisingly, early adopters of the technology are OEMs and suppliers of electric commercial fleet vehicles with a vested interest in more accurately estimating range and battery life. As you can see in the video below, Elektrobit’s Head of Technology Research, Jérémy Dahan, demonstrates a completely virtual option in which the entire stack described above is ran on an Amazon EC2 server instance. The stack simulates an EV cargo truck’s approximate range, battery life, power consumption, and other details of a long-haul trip.
In the demo, Jeremy launched a Windows VM on a specialized baremetal EC2 instance that allows hardware acceleration to run an emulated version of CAEdge created with QEMU. He further "virtualized" that emulated hardware so that it could support both EB Classic AUTOSAR and a virtualized Adaptive AUTOSAR OSs, as well as a VM that contained Elektrobit’s Linux OS for Automotive.
At the emulated platform level, all of this was partitioned and managed by an EB hypervisor. And thanks to the emulation, this nested stack can be used to deliver simulation results close to what you’d find in a traditional test setting.
The Adaptive AUTOSAR instance aggregates trip data and earmarks it for transmission to “the cloud” where it is stored as a json file on an AWSS3 server. Once there, the data can be used to train an AutoML model that accurately predicts the EV truck’s performance, then it is optimized and redeployed at “the edge.”
At the edge, the inferencing algorithm captures all relevant trip characteristics and accounts for them in range predictions. The algorithm and its predictive outcomes are also managed by the Adaptive AUTOSAR OS, which displays the outputs as information on the vehicle cluster.
In the end, every single bit of trip data collected during this process can be stored and re-played for future reference.
How Far Can Your EV Go?
For the established OEM, this solution provides insight into how commercialized EVs will operate the real world. With the help of virtualized hardware and a flexible, AUTOSAR-compliant OS from Elektrobit, engineers can monitor vehicle diagnostics to advise operators of optimum operating conditions (speed, gear, route planning, etc.) and even help inform the design of next generation vehicles if, say, they find that batteries perform poorly under certain conditions.
All of this with the goal of increasing range and efficiency, which in turn, of course, helps lower costs.
By combining these software and hardware solutions, Elektrobit is able to bridge the gap between cloud connectivity and EVs – whether they’re virtual or the real thing.