Structured Data for Analysis and Transparency in Supply Chain Resilience
January 17, 2025
Blog
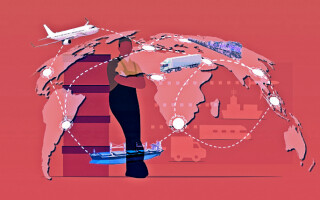
Semiconductor shortages exacerbated by the COVID-19 pandemic and geopolitical tensions served as a wake-up call for the entire industry regarding the high complexity, increasing interconnectedness, and growing vulnerability of the electronics value chain. In 2024, new opportunities and challenges have emerged for the semiconductor industry amidst economic and political turbulence.
According to the industry outlook report by Deloitte, the industry revenue is expected to double from the last decade by 2030 despite ongoing geopolitical tensions, economic downturns, inflation, and the rising cost of capital. However, according to the 2023 WTW Semiconductor Supply Chain Risk Report, in the upcoming two years, persisting raw material shortages are anticipated to have the most significant impact on businesses, accounting for 43 percent of the top supply chain factors. Having data to manage this impact is critical. However, 81 percent of companies considered the lack of data, knowledge and understanding as one of the factors posing the biggest challenge. Creating a robust, secure data-sharing ecosystem that includes protections, mapping, and traceability across the value chain is key to remaining agile and futureproofing the electronics supply chain.
The Status Quo of the Electronics Value Chain
The burden of manual inventory management
Inventory management and procurement in the electronics value chain, especially as they relate to the upstream raw material suppliers, have stagnated and remained manual for decades. Raw material suppliers upstream and their respective fab buyers deploy the repetitive workflow of sending endless spreadsheets and emails to exchange warehouse inventory information. This creates a highly manual, burdensome loop for fab buyers’ day-to-day operations. They are left with no alternatives other than sifting through spreadsheets to understand inventory levels at multiple nodes in the network, which are obtained manually through emails. Such manual workflow turns into a full-blown nightmare in cases of inventory shortages, customer or regulatory demands where fab buyers have to yet again manually contact material suppliers one by one to figure out if there’s enough inventory in transit, and if not, begin expediting to avoid shortages.
Significant lag time in demand update
Comprehensive information along the electronics value chain detailing consumer demand becomes available a quarter behind: Only at the end of each quarter are demand changes accounted for and communicated upstream, tiers N+1, to key raw material suppliers, who had been producing materials and managing inventory based on the forecasts generated at least three months ago. Consequently, material suppliers are often left in merely reactive positions to either ramp up production in the event of insufficient inventory or allocate additional storage costs for unexpected inventory surplus. The absence of a valuable data asset and a systematic solution to understand it and ensure real-time visibility through multiple tiers perpetuates the cycle of frantic, last-minute adjustments, leaving the underlying structural issue unquestioned.
Limited industry-wide real-time data understanding and sharing
As we enter the new era of technological advancement, the degree of internal digitization within companies is steadily progressing. However, companies need a secure way to connect and access data repositories and share it externally. According to a recent PwC report, although 62% of companies have achieved internal integration of data, only 36% have achieved external integration or end-to-end orchestration externally. An industry-wide data-sharing solution that enables a networked ecosystem will proactively anticipate and provide supply chain resilience in the event of unexpected disruptive events.
Breaking Down Barriers: Tackling Data Security, IP Concerns, and Building a Common Digital Infrastructure
Overcoming data security challenges
The ownership and protection of confidential data are key in preserving competitive advantages and informing company-wide strategies. Raw material suppliers may be highly reluctant to share critical information that could jeopardize their competitive advantage, such as capacity and control limits, as this information reveals their ability to produce and manage inventory, as well as to maintain quality standards and lead time performance. New product and technology information is also crucial during the development and innovation stages to protect intellectual property and maintain competitiveness, as companies that incorporate the most functionality and performance into their products fastest are the most likely to gain competitive advantages. For industry-wide adoption, a data ecosystem solution must address these data confidentiality concerns.
Building a shared digital backbone
Many players of the semiconductor supply chain still operate without an industry-wide data collaboration platform, despite a higher level of internal digitalization. Significant upfront investment is required by individual organizations before reaping the benefits of collaborative data analytics. Further, data interoperability - the ability of different systems, applications, or components to communicate and exchange data effectively - remains a significant challenge in establishing such a shared digital backbone. Currently, disparate systems and applications are used to store and manage increasing amounts of data – an average fab generates over 10 petabytes of data yearly. Considering the growing amounts of available data, different data formats used, and limited inter-corporation data collaboration, the data structure and interoperability must be ensured for companies to generate meaningful insights from the data asset.
Robust Data Security and Interoperability
Robust data security measures must be in place as a key reassurance for all data ecosystem participants. Athinia’s digital infrastructure based on Palantir Foundry has a proven track record working with government and commercial customers in the most secure and highly regulated environments and building software for their most sensitive data.
These security and interoperability measures include:
- Data protection: Data preprocessing techniques can mask, obfuscate, and normalize data so that raw data remains disclosed and aggregated data is interoperable. Preprocessed data remains useful for the generation of statistical and AI-based correlations and insights while ensuring confidentiality.
- Data governance
- Granular data access: Limiting shared data to non-controversial and non-technical information and specifying exclusive data access to key partners enables material suppliers to expedite decision-making on production schedule and inventory reallocation without compromising confidentiality. It is also an option to focus on the most critical and frequently constrained components in the Bill of Materials without wasting resources and inventory capacity on the components that rarely or never run out.
- Auditing capabilities and end-to-end transparency: Detailed audit logs ensure visibility into user actions, including records of imports, reads, writes, searches, exports & deletions, and are available for import into a Security Information and Event Management (SIEM).
- Technical Security
- Encryption at rest and in transit.
- Single Sign On (SSO) that ties to Active Directory.
- Multifactor authentication.
- Bulk export blocking.
These robust security and interoperability measures ensure a secure environment for industry-wide collaboration and proactively protect confidential information and intellectual property.
By leveraging structured data, backed by a secure framework, companies can better anticipate challenges, optimize operations, and adapt to rapidly changing market conditions. This approach enables more informed decision-making, improves efficiency, and fosters collaboration, ultimately ensuring a more resilient and flexible global supply chain.