Connecting people, processes, and IoT silicon with a digital thread
July 14, 2016
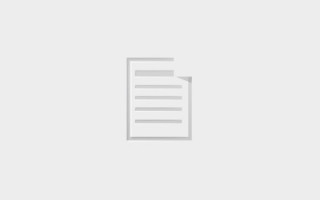
Chipmakers aren't selling simple chips anymore; they are selling complete ecosystems that encompass software, development tools, design libraries, and...
Chipmakers aren’t selling simple chips anymore; they are selling complete ecosystems that encompass software, development tools, design libraries, and strategic partnerships. Chip consumers aren’t buying fixed-function parts anymore; they are buying the potential to adapt their products to changing market demands.
Today, semiconductor manufacturers are considered silicon suppliers for the Internet of Things (IoT), the hyper-connected world comprised of intelligent devices at one end and cloud computing infrastructure at the other. Chip vendors have historically delivered microcontroller, sensor, and connectivity solutions into the volume markets now referred to as the “edge” and “gateway” tiers of the IoT (Figure 1), which traditionally involved supplying static, application-specific standard products (ASSPs) to fit the requirements of as many use cases as possible. SKUs were developed in silos with specifications, technical requirements, and other information largely isolated from the bigger picture of larger, more complex designs and other development teams within the organization. However, in the context of a connected world that now demands near-real-time design flexibility and rapid innovation in products and services, those conventional approaches to development must change.
[Figure 1 | Silicon vendors typically deliver solutions to the edge and gateway levels of the Internet of Things (IoT) that have higher volumes, but also increasing requirements for diversity and longevity. Image courtesy Atmel.]
Silicon’s new status quo and the digital thread of requirements management
The IoT is about speed and flexibility, even when it comes to hardware. As such, silicon vendors are developing complex system-on-chips (SoCs) with two to three times more memory and performance than what is required by today’s solutions, anticipating that application and system requirements will evolve and grow over time. For both chipmakers and their customers, this extra headroom implies that new features can be delivered using remote software/firmware updates, but it also means that static product lifecycle management processes are a thing of the past. Especially for silicon shipping into embedded systems expected to last 10-plus years in many cases, the IoT movement and Agile techniques have made version control truly a living endeavor, again for both the parts being supplied by semiconductor vendors as well as the end products of the customers they support.
Not surprisingly, therefore, producers of IoT silicon now increasingly demand requirements management (RM) platforms that can help engineers and product managers ensure traceability, increase efficiency, and eliminate rework across multiple SKUs, development teams, and technology areas. In other words, semiconductor suppliers need a digital thread capable of linking technical revisions, stakeholder requirements, and verification and validation efforts across geographies and over time. These solutions must provide a transparent repository that promotes collaboration without burdening participants with extraneous information, and should be accessible across departments, organizations, and, in some cases, even supply chains.
For example, chipmakers who supply MCUs and other chips for the IoT market are using Jama Software to manage a multifaceted design process that links various IoT building blocks such as sensors and actuators into their IoT chip design cycle (Figure 2). The following takes a look at how concise, specific, and parametric RM systems assist semis in adding value for themselves and their customers.
[Figure 2 | A structured collaboration process allows design engineers, verification engineers and test engineers to work in a shared space, even across organizations and supply chains.]
1. Expanding chip ecosystems
Chipmakers, as mentioned above, are now selling complete solutions, including evaluation boards, software libraries, software development kits (SDKs), protocol stacks, and more. So chipmakers, their OEM customers, and software partners have to keep track of an extensive amalgam of technical details, specifications, requirements, tasks, and goals.
Now add the fragmented IoT world to this mix and what chipmakers have at hand is a vast array of hardware and software solutions that increasingly demand a centralized requirements repository. It will keep track of each subsection and act as a hub of processor development efforts across multiple teams, particularly as system-on-chip (SoCs) continue to package more heterogeneous IP blocks and components onto a single die.
2. Multiple facets of SoC design
SoC designs entail the development of hardware, firmware, and software that is usually carried out at multiple locations, often scattered around the globe. A chipmaker may have its IP database in Silicon Valley while the memory design work is being carried out in Bangalore, India.
This globalization adds cultural and language barriers to an already complex design workflow that includes tight schedules and deadlines. Moreover, there are performance issues when engineers at multiple locations attempt to check in and out at the same time.
It’s imperative that everyone is working on the most recent version, and that a robust change management process is in place to eliminate the duplicity of work and wastage of man-hours. A requirements and specifications management system offers a clear picture of the impact of change and an easy traceability of that change (Figure 3).
[Figure 3 | Jama’s RM software enables different workflows and development teams to operate in a single common space.]
3. IP and design reuse
Chip designers are increasingly using IP blocks from internal and external sources, and in order to effectively handle IP reuse and system partitioning, chip designers need to keep track of all the design blocks at all times. Moreover, they must keep track of various versions of the IP content such as schematics, layout, simulation, and technology kits.
The intertwined world of IPs, cores, and design methodologies makes it hard for traditional document-based product development workflows to handle increasingly complex chip design cycles. Here, features like workflow mapping available from RM systems like Jama allow design teams to work in their particular space while simultaneously collaborating with other teams in real-time to quickly responding to changes in design workflows.
4. Foundry liaison
After tape-out, the next big thing is the liaison with the foundry, and here, new technology nodes, tight delivery schedules, and unique customer functional requirements demand a dynamic system that can track changes happening on multiple axes. These changes are dynamic because multiple designers are operating on the same data.
It’s crucial for chipmakers coordinating cross-functional deliverables related to design, manufacturing, IP, and software development to use a robust RM system that keeps all stakeholders tied to a system of action like Jama. This allows engineers to efficiently handle end-to-end product development with a traceability that shows the impact not just on technical or specification requirements, but also on the people.
The thread that ties it all together
A digital thread driving requirements management within a product development cycle is highly relevant for semiconductor firms developing for the extreme diversity of the Internet of Things, especially as they take on more elements of a complete solution to better serve their customers. Today’s RM platforms can facilitate these intricacies while advancing technology reuse and speeding time to market, as well as provide an apparatus for collaboration for all stakeholders involved.