PCB laminate considerations for 4G-based M2M designs
August 10, 2015
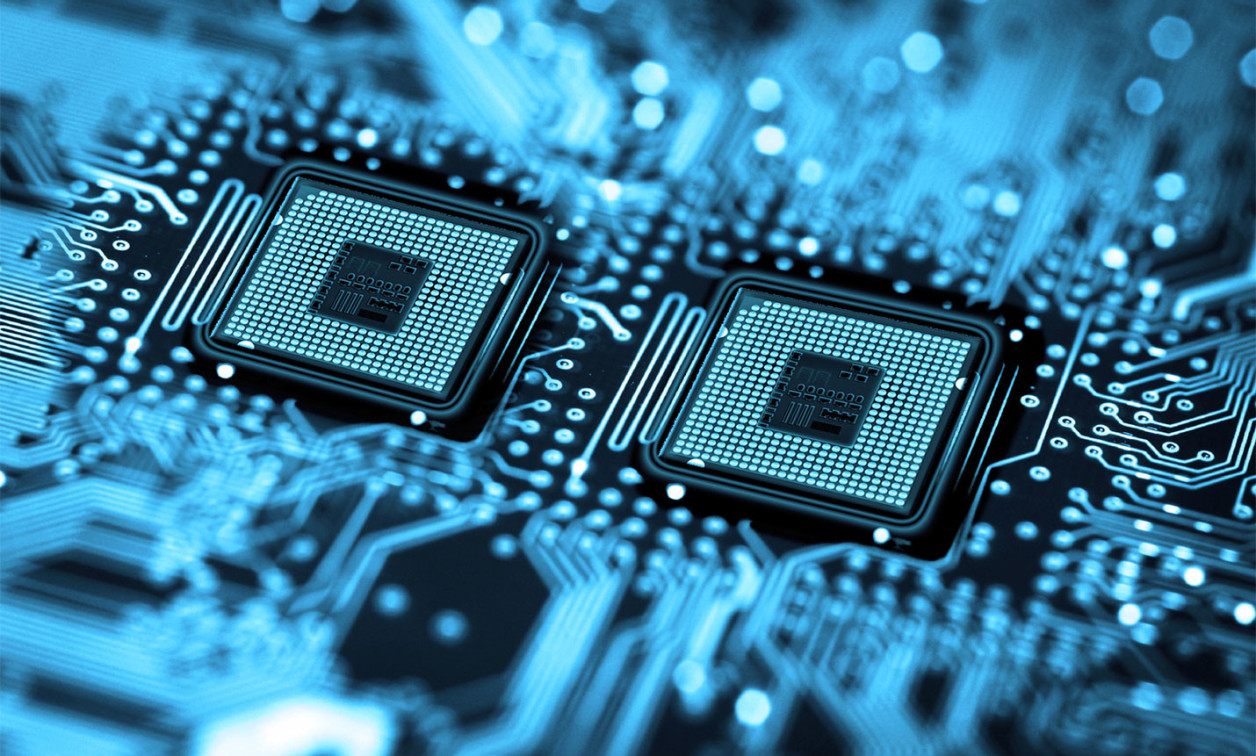
Machine-to-machine communication (M2M) took off a few years ago when major cellular operators embraced the trend and began offering low-cost data plan...
Machine-to-machine communication (M2M) took off a few years ago when major cellular operators embraced the trend and began offering low-cost data plans for connected devices in automation, real-time monitoring and home security segments. Mobile phone carriers used the GPRS links in second-generation (2G) wireless networks like GSM for this form for communications that serve machines rather than people.
Now the M2M bandwagon is ready for the next big turning point: a shift from 2G to LTE-based 4G networks. That’s partly because mobile phone companies around the world have started planning for shutting down their CDMA and GSM networks in the coming years, and LTE is inevitable the next frontier. The LTE-centric 4G systems are based on IP network architecture and are inherently more suitable for device-to-device communications.
Moreover, the LTE establishment is readying the 4G networks for M2M and other Internet of Things (IoT) applications with Cat 0 and machine type communication (MTC) solutions optimized for low-power and low-bandwidth requirements.
When it comes to issues like board design and PCB material selection for M2M applications, there are a few things that won’t change with the shift from 2G to 4G networks. For instance, M2M applications, mostly exposed to outdoor or industrial environments, will continue to operate across a wide temperature range. Likewise, form factor, thermal requirements, and exposure to moisture and humidity will largely remain unchanged.
However, the LTE-based M2M designs bring a new set of unique challenges that will make the choice of PCB material a prudent first step for a robust product design. First and foremost, LTE is synonymous with a sophisticated RF infrastructure, where the use of complex transmission technologies like OFDM and small cell networks make the selection of PCB material a key consideration.
In RF designs, for instance, the PCB material counts a lot when it comes to system parameters such as bandwidth and frequency of operation. Then, there are loss and uniformity requirements; a PCB contributes to system loss through conductor loss, dielectric loss and impedance mismatch. A high-frequency signal on the PCB is severely affected by the dielectric loss.
Next, the use of technologies such as MIMO brings a heavy signal processing workload for M2M applications. Moreover, there are multiple wireless standards and handling the complexities of this multitude of wireless technologies can be a daunting task for an M2M board that is sometimes of the size of a credit card. The demand for faster processing and more efficient designs inevitably calls for thinner and more powerful PCBs.
The M2M and other IoT applications are still evolving and so is the PCB market of these applications. Isola Group is one such outfit that has kept an eye on the evolving needs of PCB fabricators for M2M and other emerging IoT devices. The company recently made available the IS350MD laminate material that has been engineered specifically for ultrathin dielectric applications.
The IS350MD laminate boasts low-dielectric constant (Dk) of 3.35 to meet the impedance requirements of the IoT designs. Earlier, in 2014, Isola unveiled the ultra-low Dk material, IS300MD, which has a Dk of 3.06. Both IS350MD and IS300MD laminates are halogen free and display greater thermal stability than standard FR-4 material.
Isola – a supplier of copper-clad laminates and dielectric prepreg materials for multilayer PCBs – has also demonstrated its Astra MT laminate for RF front-end PCBs with Freescale’s ICs for 77 GHz ADAS radar applications. Astra MT materials are considered highly suitable for patch antenna designs and offer a higher yield and lower production costs in RF-hybrid PCB designs.