Unlocking Efficiency: How ADI Battery Management Solutions Empower Safer, Smarter Mobile Robots
August 27, 2024
Blog
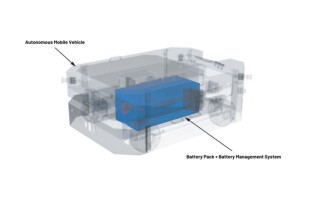
In the rapidly evolving landscape of automated warehouses and manufacturing facilities, meticulous control over each component of the process is paramount. Even the slightest downtime can result in significant repercussions. Autonomous mobile robots and automated guided vehicles play a vital role in this ecosystem, requiring the implementation of precise monitoring and fail-safe systems.
Another crucial subject is the efficient monitoring of batteries, which can optimize their performance and extend their overall lifetime, thereby minimizing unnecessary waste and preserving valuable resources. This article will provide a brief description of some of the important metrics used to improve battery efficiency and guide on key considerations when selecting battery management systems for these applications.
Introduction
Choosing an appropriate battery pack and its accompanying battery management system (BMS) is a critical decision in designing an autonomous mobile robot (AMR) as shown in Figure 1. In tightly integrated settings like factories and warehouses, where every second of operation matters, ensuring the safe and reliable functioning of all components is of utmost importance.
BMS solutions can provide accurate measurements on the charging and discharging of the batteries, which maximizes the usable capacity. Additionally, the precise measurements allow for an exact calculation of the state of charge (SoC) and depth of discharge (DoD), which are essential parameters to allow smarter workflows of mobile robots. Equally important are the safety aspects of such systems and it becomes crucial to consider BMS technologies that provide both overcharge protection and overcurrent detection while selecting systems for these applications.
Figure 1. An AMR diagram.
What Are Battery Management Systems?
A BMS is an electronic system that can be used to closely monitor various parameters of a battery pack and/or its individual cells. It is critical for achieving the maximum usable capacity of the batteries while ensuring safe and reliable operation. An efficient system can not only optimize the usable capacity of the battery in a safe manner but also provide the engineers with valuable parameters such as the cell voltage, SoC, DoD, state of health (SoH), temperature, and current, all of which can be used to get the best performance out of a system.
What Are SoC, DoD, and SoH, and Why Are They Important for Automated Guided Vehicles (AGVs) and AMRs?
SoC, DoD, and SoH are a few of the common parameters used in BMS to determine if the system is healthy, early fault detection, cell aging, and the remaining time of operation.
SoC stands for state of charge and can be defined by the level of charge of a battery in relation to its total capacity. SoC is usually expressed as a percentage where 0% = empty and 100% = full.
SoH or state of health can be defined by the maximum capacity (Cmax) of the battery that can be released relative to its rated capacity (Cmax).
DoD or depth of discharge is the opposite metric of SoC and is defined by the percentage of the battery that has been discharged (Creleased) relative to its rated capacity (Crated).
How Are Those Relevant for an AMR Solution?
The SoC of a battery varies according to the battery architecture, nonetheless, it is necessary to have a precise system to measure the state of a battery. Two main types of commonly used batteries are Li-Ion and lead acid batteries. Each has its pros and cons, with various subcategories. In general, Li-Ion batteries are considered a better choice for robots because they offer:
- More energy density, which could be in the order of 8 to 10 times the energy density of a lead acid battery.
- Li-Ion batteries are lighter than lead acid batteries of the same capacity.
- Charging a lead acid battery takes longer than charging a Li-Ion battery.
- Li-Ion batteries offer an extended life cycle, allowing for a significantly higher number of charge cycles.
However, these advantages come with a higher cost and pose certain challenges that need to be addressed to fully realize their performance benefits.
To better explain this in a real-life application, it is possible to analyze the plot in Figure 2, which compares the DoD of a lead acid battery and a Li-Ion battery. It can be observed that the pack voltage varies minimally for a Li-Ion battery while going from 0% DoD to 80% DoD. 80% DoD is usually the lower limit for Li-Ion batteries and anything below that can be considered a dangerous level.
However, because the pack voltage on a Li-Ion battery only shifts minimally for the usable range, even a minor measurement error could lead to a substantial decrease in performance.
Figure 2. Battery pack voltage level vs. DoD.
Figure 3. AMR generic battery and BMS architecture.
To illustrate this in a real-life scenario:
Imagine the following AMR is a 24 V system and uses a 27.2 V LiFePo4 battery pack where each cell has a capacity of 3.4 V when fully charged. See Figure 3.
A common profile for an SoC for such a battery can be seen in Table 1.
Table 1. Example Data for LiFePo4 Battery Cell and Pack Voltage
For LiFePo4 batteries, the usable range can vary, but it is a good rule of thumb to consider that the minimum SoC is at 10% and the maximum is at 90%.
Anything below the minimum level can cause an internal short circuit on the battery and charging above 90% reduces the lifetime of these batteries.
Taking Table 1 into consideration, note that the voltage range per cell is 350 mV, and for a 27.2 V pack with 8 cells, it is 3.2 V. Having that in mind we can draw the following assumptions:
If the usable cell voltage range for a LiFePo4 battery is 350 mV, then every 1 mV of cell measurement error reduces the range by 0.28%.
If a battery pack cost is $4000, the cost of error is:
$4000 × 0.28% = $11.20/mV error, which means that the battery packs would be underused for the range.
While 0.28% of the range may appear negligible, when scaled up to multiple AMR systems, this percentage could be multiplied by hundreds or even thousands, making it a significant factor. This factor becomes even more relevant if natural battery degradation is taken into consideration.
Natural degradation also plays an important role in battery health as, with time, the maximum SoC of a battery will degrade (Figure 4), hence why a precise measurement of the cells is the best way of keeping performance at an optimal level, even after natural degradation.
Figure 4. Maximum usable range reduction due to natural degradation.
Monitoring all the parameters and precisely controlling the usage of the battery is the best way to extend the life cycle and take advantage of every single unit of charge.
Increasing Productivity
The precision of battery management significantly enhances the efficiency of batteries by precisely measuring the cells, allowing for more accurate control and estimation of the SoC across various battery chemistries. Measuring each cell individually ensures safe monitoring of battery health. This precise monitoring facilitates balanced charging, preventing cells from overcharging and discharging. Additionally, synchronous current and voltage measurements increase the accuracy of the acquired data. Extremely fast overcurrent detection allows for quick failure detection and emergency stops, ensuring safety and reliability.
Figure 5. Main degradation factors for Li-Ion batteries.
The ADBMS6948 provides all the key specs required for mobile robots, but a few critical specs with BMS design considerations for a mobile robot are:
- Small total measurement error (TME) over a lifetime, (–40°C to +125°C)
- Simultaneous and continuous measurement of cell voltages
- Built-in isoSPI™ interface
- Hot-plug tolerant without external protection
- Passive cell balancing
- Low power cell monitoring (LPCM) for cell and temperature monitoring in key-off state
- Low sleep mode supply current
Reducing Waste and Helping the Environment
According to the International Energy Agency’s 2023 report on batteries, “Batteries are an essential building block of the clean energy transition.”1 It is crucial to recognize the importance of properly managing these resources. The materials that constitute a battery are difficult to extract from the environment, underscoring the need for their optimal utilization. By efficiently managing the charging and discharging parameters, we can extend the lifespan of batteries, allowing them to be used for longer periods without needing replacements.
The low-risk factor with overcurrent protection provided by ADI’s BMS feature allows for very safe operation and cuts down on the risk of damaging both the battery and the system connected as a load.
A few examples of degradation factors in Li-Ion batteries can be seen in Figure 5, and it is important to note that they can lead to dangerous situations such as combustion and explosion, which could quickly become catastrophic.2
All the parameters that influence battery degradation can be measured, treated, and acted upon, providing the system with the most optimal conditions to operate over the required lifetime. Increasing the battery’s lifetime is an important factor in the reduction of waste as the batteries can now be used longer due to optimized management, effectively reducing the unnecessary disposal of battery cells.
Conclusion
In summary, we can conclude that BMS can not only increase the overall performance of the system by allowing every parameter to be precisely controlled but also reduce cost and waste. In an evolving manufacturing environment that is becoming more and more automated and is seeking the extra percentage of performance on its mobile robots, precisely controlling and managing assets becomes essential.
To learn more about ADI offerings for industrial mobile robots, please check our robotics solutions page.
References
1“Batteries and Secure Energy Transitions.” International Energy Agency, 2023.
2Xiaoqiang Zhang, Yue Han, and Weiping Zhang. “A Review of Factors Affecting the Lifespan of Lithium ion Battery.” Transactions on Electrical and Electronic Materials, Vol.22, July 2021.
Based in Limerick, Rafael Marengo is a system applications engineer in the Connected Motion and Robotics Business Unit at Analog Devices, supporting various technologies that range from BMS, to motion control, and others. He joined ADI in 2019 as a design evaluation engineer for the Precision Converters Technology group. Rafael holds a bachelor’s degree in control and automation engineering from the Federal University of Lavras in Brazil. Before he joined ADI, he worked as an R&D manager for a machine vision startup focused on the agritech market where he was responsible for getting many products onto the market on a global scale.