The Semiconductor Supply Chain Slowdown & the Need for Smarter Data Sharing
December 28, 2021
Story
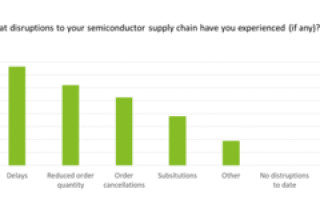
By now everyone’s aware we are in the midst of a global semiconductor shortage. Some experts predict it will come to an end before 2022 is up. Others say it will last well into 2023. But the electronics industry needs supply chain solutions, not predictions. And hopefully those solutions can also help prevent such shortages in the future.
Currently, most organizations plan on solving the crisis now and in the future by moving away from just-in-time (JIT) manufacturing. JIT is the practice of producing materials or components just before they are needed to cut costs associated with building and storing surplus inventory. It makes total sense unless you need to fall back on stockpiles – like in a global pandemic.
The JIT model was pioneered by Toyota, and it’s no surprise (and no secret) that the company was one of the first to experience major setbacks when COVID-19 first hit. But while we won’t soon forget the negative consequences of low inventory, the power of profit is very real.
When market forces return to some semblance of equilibrium, there will undoubtedly be a desire to reduce expenses so quarterly earnings statements show higher profitability. At the same time, industry is moving to process nodes so advanced that predicting how materials and manufacturing methods will interact is becoming increasingly difficult, which itself can result in lower wafer yields, fantastically expensive waste, and seriously impede time to market.
But with all the intelligence enabled by the IoT and Big Data, there has to be a smarter way that rides the line between cost and speed, doesn’t there?
Big Data Breaks Bottlenecks, Ups Insights
Earlier this month, Merck KGaA, Darmstadt, Germany and Palantir announced that they have been integrating their expertise in device manufacturing processes and secure data platforms, respectively, to create a smart data ecosystem that lets semiconductor manufacturers and materials suppliers collaborate in a secure environment. The joint effort resulted in a joint venture, Athinia.
Athinia, the name of both the startup and the platform, works by aggregating material, in-process, and manufacturing data from companies across the semiconductor supply chain. It then performs multivariate analysis against supply chain bottlenecks, quality or performance excursions using big data and AI.
Especially as we move to increasingly advanced process nodes beset by manufacturing complexity, Athinia will provide semiconductor fabs better insight into the quality of inbound materials. In turn, they can make better manufacturing predictions, reduce deviation, and make more intelligent material selections in the future.
Conversely, the platform allows materials suppliers to play a more active role in the manufacturing process by focusing on the parameters that are most important to fabs and improve how they manage sub-suppliers.
In short, it provides greater transparency across the semiconductor industry so that stakeholders can focus on the parameters that matter the most.
Data Sharing: How Supply Chains Show They Care
It seems like at least some level of data sharing and transparency should have existed before now. And, in truth, it has.
However, the big difference between Athinia and the past lies in what and how much of that data was shared with whom. Laura Matz, Chief Science Officer at Merck KGaA, Darmstadt, Germany, and newly appointed CEO of Athinia explains why that makes
“One of the challenges is there are many database that have been developed over time,” she says. “All suppliers will have a couple of databases like SAP for ERP, an in-process database on manufacturing processes, and then a quality assessment database for raw materials supply and finished goods. That then goes to the device manufacturer.
“Since most companies have these databases, the question is how to bring them together,” Matz continues. “The aggregation of data in a logical and systematic way is complex to do in practice.”
And that’s why the combination of Palantir’s data ontology and hierarchy knowledge with Merck KGaA, Darmstadt, Germany’s materials expertise is so critical. The Athinia platform is built on top of Palantir Foundry, a platform in its own right that helps users structure and analyze data from disparate sources. When combined with AI-enabled multivariate analysis, the Foundry foundation allows Athinia to identify and link significant process, materials, and product parameters.
This information can be shared securely between organizations on the Athinia platform to create one-to-one, one-to-many, or many-to-many data ecosystems that break silos and support “first-time-right” semiconductor manufacturing.
Semiconductor Security and the Need for Speed
For many organizations, the prospect of revealing internal data may seem like an invitation for IP theft or contamination. To eliminate these security vectors while facilitating normalized, structured data sharing, Athinia uses industry standard security primitives, purpose-based access control, data obfuscation, and codification techniques. It also operates independently of the electronics business unit at Merck KGaA, Darmstadt, Germany.
Of course, there is also an alternative to the Athinia approach: creating a data foundation in isolation. Athinia leadership estimates this would take the average semiconductor company 5-10 years, and the outcome would likely still not have the flexibility to support every player and component in the supply chain.
“This is a pattern we see across many organizations with data deployed across multiple sectors for foundries. It’s compounded by the fact that you’re bringing data from two organizations together,” explains Alec McShane, Executive Vice President of Athinia and Palantir’s Business Development Lead, explains.
“The speed is really the key point,” he continues. “We’ve done some comparisons of uploading multiple products for a manufacturing plant. Isolated, it would take a 12 to 18 months. But the Athinia approach can do this in 2 to 3 months. We have a global supplier who has integrated 30 ERPs in less than a month.
“Especially when the industry is trying to move quickly, this can open up a lot of opportunity and supply chain bandwidth,” McShane adds.
The electronics industry has long been driven by a balance of cost and time to market pressures, and while Athinia may be unconventional, it also represents a way forward in unconventional times.
It may not have come in time to prevent the initial fallout of the pandemic, but at this point who knows how long COVID-19-related supply chain disruptions will last. And whether they end in 2022, 2023, or beyond, shouldn’t we, as an industry, be prepared for the next disaster?
For more information on semiconductor supply chain data sharing and intelligence, visit https://athinia.com.