Storage Requirements for Reliable 5G Gateways in Industrial Systems
January 14, 2022
Story
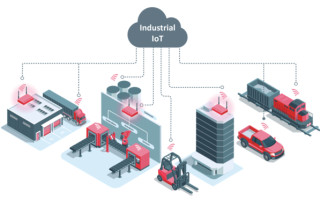
Manufacturing and production are being revolutionized by the increasing use of digital technologies for automation and communication between systems. Access to real-time data enables more efficient use of resources and pre-emptive maintenance to minimize downtime and maximize the operating life of equipment.
After the introduction of steam engines, electrification, and computing, the application of connectivity, big data analytics, and the Industrial Internet of Things (IIoT) is often referred to as the fourth industrial revolution, or Industry 4.0.
This growth in the number of connected devices in industrial applications requires highly reliable communication products to integrate public and private networks. This, in turn, results in increasing demands for industrial storage, in particularly as it is applied to industrial IoT gateways.
Connected systems in Industry 4.0
Growth in the 5G Market
By 2023, there are likely to be over 4 billion machine-to-machine (M2M) connections across a growing range of applications. This includes navigations systems in vehicles, asset tracking in logistics, wearable medical components that monitor a patient’s vital signs in real-time, and industrial manufacturing.
It is expected that an increasing proportion of the communications infrastructure will move to “standalone” 5G networks; that is, they will not rely on the existing 4G/LTE infrastructure. Therefore, future investment is likely to be focused on 5G New Radio (NR) infrastructure rather than legacy systems.
This will make the enhanced capabilities and new features of 5G more widely available: higher data rates, very low latency, improved synchronicity, and greater reliability. Developers of industrial systems will want to exploit these features to enable innovative new applications.
Using 5G Connectivity in Industry 4.0
The Gateway to 5G
In order to get the benefits of 5G within an industrial environment, it is necessary to have an interface between the many different internal devices making up the industrial IoT and the 5G network. This gateway must carry the 5G performance through to the industrial IoT network.
In the industrial setting, a 5G gateway aggregates the various protocols used by the many different connected devices in the factory such as sensors, actuators, and automated machinery. It encapsulates the data into a format that is suitable for transmission over a 5G radio interface and performs the reverse process for data received from the 5G network.
Use of 5G gateways in Industry 4.0 systems
Gateway Software Requirements
5G gateways need to run large, complex software. The codebase will consist of an operating system, network layers, and the protocols needed to interface to legacy devices. This means millions of lines of code and tens of gigabytes of persistent storage. This storage requirement can only be met using NAND flash, which comes with system-level requirements of its own.
To provide the performance levels demanded by these industrial applications, the gateways need to meet the same service level specification (SLS) as the 5G network itself. This means the gateway must match or exceed the cellular network’s capabilities, while also meeting the requirements of the connected industrial systems. They must also operate in demanding environmental conditions, possibly outdoors, and often with extremes of temperature.
Therefore, every component in the system must be chosen or designed to meet the reliability and operating lifetime requirements. This includes electro-mechanical components, power supplies, semiconductor components, and, especially, the non-volatile storage for mission-critical code and data.
Specifying secure and reliable storage that uses a flash controller optimized for a system’s mission profile is extremely important in achieving a specified performance and operating life. The storage system must enable the gateway to meet the same standards for performance as the 5G network itself.
Operating Lifetime Requirements
The rate of replacement of systems in many industries is counted in decades. The costs of unplanned downtime can be significant and so the gateways installed now must continue to operate and provide the same quality of service and reliability, for many years.
Semiconductor manufacturers use design rules, power analysis, simulation, and accelerated lifetime testing, to quantify the behavior of a device and how environmental factors will affect it. This allows the manufacturer to accurately specify the operating lifetime under given conditions.
Some devices are designed and characterized for consumer use. They are only expected to be active for a few hours per day, with a lifetime of, say, 5 years operating at normal room temperatures. This is very different from an industrial component specified to operate 24 hours a day, seven days a week for a minimum of ten years in a wider range of environmental conditions: industrial semiconductors are typically qualified with an operating temperature range of -40 to 85°C.
The Importance of Thermal Management
Temperature is one of the key design issues that have to be considered. It affects many operating parameters of the transistors in chips, including leakage current. The leakage current of an NMOS transistor typically increases tenfold as the ambient temperature increases from 50°C to 100°C. This is important because as leakage current increases the power dissipation also increases. Effective thermal management is therefore essential.
High temperatures also have a significant negative impact on the operating lifetime of a device. In the case of NAND flash, both high temperature and temperature variation will stress the cells, causing higher error rates which reduce the overall lifetime of the storage system.
The ability of flash cells to retain data falls rapidly with increasing temperature. An increase of 20ºC can reduce data retention time by a factor of 10. On the other hand, low temperatures make it harder to accurately program a specific level of charge on a cell. Raw error rates and the time needed for the program and erase cycles vary with temperature in complex ways.
All of this is worse for multi-level cell (MLC) flash devices that store more than one bit in each memory cell because the charge levels that need to be accurately programmed and reads are much closer together. As a result, industrial systems tend to rely on single-level cell (SLC) or pseudo-SLC (pSLC) memories because of their greater reliability and longer lifetime.
The flash controller can use a variety of mechanisms to manage the effects caused by environmental stresses and maximize the operating life. For example, wear leveling ensures that data is written evenly to every block in the flash memory so that no blocks become unusable prematurely. Sophisticated error correction codes can be used to detect and correct errors in the memory cells. By tracking the number of errors that need to be corrected, the controller can determine when a memory block needs to be rewritten to avoid any potential loss of data. Ultimately, this can also provide an early warning for a device reaching the end of its useful life.
Using a flash controller that is optimized for the performance and environmental requirements of the application is essential to create a high-quality storage system that will achieve the specified operating lifetime.
Conclusion
When designing an Industrial IoT 5G gateway, the performance, storage, and security profiles need to be as close as possible to the 5G network. This ensures that the system as a whole can meet its end-to-end service level specification and meet the requirements of the new and emerging applications.
To meet all the requirements of an industrial-grade application, it is essential to choose the right storage technology, vendor, and supply chain. In particular, you need to confirm that the selected storage system (including the NAND flash devices used) meets these requirements.
Selecting the right NAND flash controller and firmware will ensure that the intrinsic physical properties of the memory technology and its inherent weaknesses are properly managed. This allows the storage to meet its mission profile reliably.
With extensive experience in delivering high-performance, secure, and reliable storage solutions, Hyperstone is ready to discuss any aspects of non-volatile storage as they relate to creating an industrial gateway.
Axel Mehnert is responsible for marketing, product strategy, and business development across product lines and market segments at Hyperstone. He has been involved with the Flash industry for over 15 years. Before joining Hyperstone, he held various positions at technology and semiconductor companies in product marketing, sales, and strategic planning with Siemens, Evergreen Technologies, and Texas Instruments. He holds a BS in economics from Kiel-University, Germany and an MBA from Oregon State University.