Sophisticated Automation and Quality Assurance in the THT Process
May 30, 2023
News
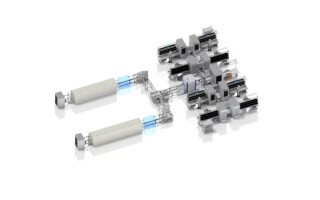
Optimizing a complete wave soldering system, including assembly workstations and inline automatic optical inspection (AOI) from the ground up, implementing a smart factory implementation, and increasing the quality of the products, can be quite the challenge for system builders and testing specialists. However, this feat was accomplished by Pacha Automation and GÖPEL electronic.
Increased Demands on THT Production
With increasing demand and higher throughput, there was a need for optimization in the area of through-hole technology (THT) production. Individual transport systems, time-consuming manual work, and manual selection of up to 150 soldering programs were highly prone to errors. The desired end result was a more intelligent transport system and a higher quality assurance of the assemblies.
Production line with wave soldering furnaces (shown in front)
A Smart Transport System
The system networking was implemented on both horizontal and vertical planes. RFID identifiers on the carrier medium held all relevant information about the product. From each fully automated station, the assemblies are routed to both interlinked wave soldering systems. An antenna system records the RFID data, whereupon the system itself decides which oven to route the assembly to. Selecting the appropriate test program also occurs automatically.
The basis for this flexible production management is Pacha's PaVis software tool. The central control system (CCS) is not only used for large plants, but also for smaller automation systems for control, monitoring, or visualization, as well as analyzing data for tracing and optimizing the production process using a ZLS.
Shown are the line concept with placement stations (right) and wave soldering systems (left).
Providing more quality assurance for the THT assemblies can only be achieved in the long term with an AOI system. In this instance, the assembly was fed through an upper transport module towards the soldering oven and only inspected in the lower return transport from the lower soldering side without turning. The 3D camera module on the chosen line inspects the soldered pins of the assembly, determines solder flow and solder volume, and reliably detects bridges and solder beads. Thanks to the MES plug-in, integration into the process control system or MES system was easy to implement.
Pictured is the THT Line, which used a 3D camera for AOI testing.
Looking back on the extensive changes, from planning to commissioning took about a year, with the direct implementation of the plant taking half a year. The production standstill during installation was only a few days. Today, the capacity utilization is about 95%.
More information is available at https://www.goepel.com/.