More functions means less protection
December 04, 2015
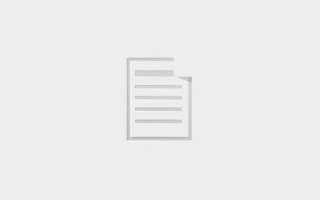
ICs are getting denser. Yes, I know you know that. But did you know that as they get smaller and denser, they get harder (in some cases significantly...
ICs are getting denser. Yes, I know you know that. But did you know that as they get smaller and denser, they get harder (in some cases significantly harder) to protect against over-voltage transients, electrostatic discharge (ESD), a perturbation on the power line, or something else?
Back in the good old days, circuit protection was actually built into the ICs. But as they got more dense and contained many more features, the circuit protection got squeezed out and needed to be handled off-chip. In addition, the older, less-dense devices could handle some of the surges a little better than today’s components, regardless of the protection. So the ICs are getting hit from both sides.
According to Chad Marak, the director of semiconductor business development at Littelfuse, “As time went on, two things happened. First, designers were getting squeezed for space, so they couldn’t include any of these ESD structures on the chip. And two, even if they did, it wouldn’t do them much good because the state-of-the-art geometries and line widths can handle less energy from the over-voltage transients.”
As the designers were pushed to add more features, they had no choice but to remove the circuit protection. And for companies like Littelfuse that specialize in circuit-protection devices, it was a huge win. It’s actually a win all around, because it lets the circuit-protection vendors do what they do vest, and it lets the processor vendors focused on the core value of the processor.
Here’s something else you may not have been aware of: There are groups like the ESD Association (ESDA) who monitor these types of progressions in technology. The ESDA started out specifying the over-voltages that IC designers should incorporate into their devices just so they could go through the manufacturing process unaffected. For example, a worker who touches the manufacturing equipment is putting the parts at risk.
As time went on, it became clear that the ESDA had a bigger issue on its hands, namely dealing with the now non-existent on-chip protection. So the focus migrated to placing the over-voltage circuit protection elsewhere on the PCB. And this was tackled with full confidence that the protection was never going back on-chip.
As Marak points out, there’s a clear connection between the need for circuit protection and the Internet of Things (IoT).
“The IoT gives you more devices and all of these devices are being handled or touched by a human or they are connected to a network via cabling,” Marak says. “That gives the possibility of an over-voltage event due to lightning strikes or surges within your house thanks to the power company. And that translates into a need for more protection. The transients themselves are going to do the damage and as you add more devices, you have more touch points that are susceptible to damage.”
It became clear to me as I delved more deeply into the circuit-protection realm that there’s a real need for more education on the subject. It’s not really addressed properly at the college level, so engineers are often left to fend for themselves.
Typical design tools don’t always have a library for ESD components and there isn’t an easy way for people to simulate the effects. What’s really needed is a suite of tools that engineers can use to better predict which kind of protection they need for their application.
While there’s no timetable for such a product today, at least people are starting to talk about it. That’s a good first step.