EV Battery Cells Get More Complex, Taking the BMS Along for the Ride
July 19, 2022
Story
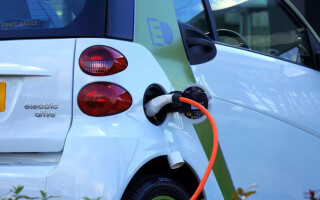
Electric vehicles (EVs) are not new. They actually pre-dated the gasoline-powered cars that Henry Ford made famous 100 years ago. However, their deficiencies were glaring, and they were doomed to (near) obsolescence until fairly recently, maybe 15 years ago, when they took on a resurgence. From a PR perspective at least, Tesla has done more for the electric vehicle than all of its predecessors combined.
Like many of the technologies we work with on a daily basis, those required for a mainstream EV needed help. Thankfully, that help is on the way, both in the batteries that power the vehicles and the ICs that manage those battery subsystems.
Both of these concepts got a jump start from the consumer electronics industry, mainly mainstream laptops and smartphones. Obviously, the scale is completely different, but the concepts are the same. For example, Lithium battery technology improved immensely during the PC/laptop boom, and that research paved the way for the batteries that are used in today’s EVs. Because of the power levels required by the EV, batteries needed to move from somewhere around 3 V up to today’s 400- and 800-V systems, and the testing required to make that leap is huge. Learn more in this video.
At the same time, the battery-management system (BMS) used in EVs had to make a similar leap. When there is a fault with your smart phone or laptop, you can reboot or in an extreme case, you lose the service of your device. The same cannot be said for a fault in an automobile. Hence, the pressure to eliminate all failures is huge.
Infineon, one of the leaders in battery-management systems, has experience at all levels of the voltage chain. In the case of the automobile, the higher voltage levels require the use of far more cells, which means a more complex BMS, with the same mantra—failure is not an option.
Increasing Complexity in BMS
Typical automobile battery cells, depending on their chemistry, have nominal voltages between 3.2 and 4.3 V. Therefore, a typical 400-V battery pack required more than 100 cells. Today, with many major auto makers moving to 800 V, the number of cells in series (and associated cell sensing ICs) must double to more than 200.
Two key parameters are being monitored in a battery at any given time, namely the battery-cell voltages, and the temperatures in multiple locations within the pack. In addition, auto makers balance the charge across all cells in a pack to ensure that the cells charge and discharge properly and evenly. This is both for safety and wear reasons. These tasks are typically performed by a battery-monitoring and balancing IC, also known as a battery-management IC.
The latest battery management ICs, including Infineon’s TLE9012 DQU, can handle multiple cells in series, up to twelve in the case of the Infineon part. The dedicated ADC for each cell and the high system integration enable significant cost reductions for the automakers. Each of the TLE9012DQU parts also has five inputs for temperature monitoring and offers robustness against hot-plugging with no external components.
Accuracy Is Key
The accuracy of the BMS devices is of the utmost importance, and that has a lot to do with the battery chemistry that’s being deployed in the vehicle. The two main chemistries used today are Nickel Manganese Cobalt (NMC) and Lithium Iron Phosphate (LFP). NMC cells tend to be higher performance and higher density, so they weigh less for a given battery capacity. Conversely, LFP cells tend to be cheaper but heavier for a given capacity. They are commonly used in many of the lower end EVs, but time will tell whether even those vehicles will move toward NMC use.
The LFP cells also require a higher accuracy BMS because of their unique charging profile, which is flatter than other chemistries like NMC. This characteristic also changes over the life of the cells. Having the BMS “understand” how the batteries change over time is critical. For example, a brand-new battery will charge differently and have a higher capacity at full charge than one that has gone through thousands of cycles. If this is not recognized by the BMS, problems could arise. Batteries also wear and degrade differently based on a number of factors, including temperature and use. This applies to both LFP and NMC battery cells.
The Wireless BMS
The next evolution of the battery management system is to handle communications wirelessly. As you might expect, thorough testing had to take place before such a configuration was even considered. GM announced about a year ago that it would deploy the first wireless BMS in its Hummer electric vehicle, supplied by Visteon. By removing some of the wiring and the associated wiring harness, auto makers can save on cost and weight. Another advantage to the wireless BMS is a savings in production automation by removing several connectors, which generally require manual labor on the assembly line. Having the wireless signal inside what’s typically a metal box helps keep those signals intact and robust.
Stay tuned, as Infineon will soon offer a wireless BMS solution based on Bluetooth Low Energy, which permits the use of a proprietary high-performance mesh network running on top of the Bluetooth protocol. This hybrid between a star network and mesh network configuration allows signals to communicate most efficiently and to be rerouted through other nodes if there is ever a loss of connection. More information is available on Infineon’s AIROC Automotive Wireless page.
The EV is coming, as most of the major auto makers have pledged that a high percentage of their vehicles will be battery-powered over the next few years. The BMS must keep pace.
Marco Castellanos is the Senior Product Marketing Manager for Automotive Battery Management and Onboard Charging at Infineon Technologies. In this role, he is responsible for developing system solutions utilizing Infineon's intelligent power devices, microcontrollers, power supplies, sensors, and networking with CAN and Ethernet devices for battery management and onboard charging. Castellanos has 7+ years of automotive experience.