IoT to Enable RTLS for Higher Productivity
January 11, 2021
Blog
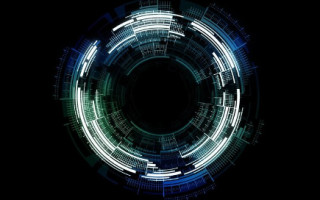
Real-Time Locating Systems (RTLS) are used to identify and track the location of objects or people in real time, usually within a building or other contained area.
How many of you spent lots of time searching for items, assets, parcels, tools, and fixtures around your facility, simply because they were not where they were supposed to be? Especially if you have worked for complex organizations, I am sure it has happened several times. It happened to me as well when I was manufacturing engineer for aerospace organizations, and it doesn’t matter how organized your company is. Logistic complexity is simply difficult to manage.
Manufacturing environments are becoming more difficult to manage than ever for several reasons:
- Pull Systems are more efficient, but imply a high turnover of assets
- Reconfigurable Manufacturing Systems enable higher competitiveness. However, production lines must be reconfigured more often, with a lot items coming in and out
- Parts Traceability is becoming a fundamental aspect in improving logistics efficiency
In this sense, RTLS are becoming an essential tool for all manufacturing organizations. With RTLS, the more complex the system, the better.
What is a RTLS?
Real-Time Locating Systems (RTLS) are used to identify and track the location of objects or people in real time, usually within a building or other contained area. Wireless RTLS tags are attached to objects or worn by people, and in most RTLS, fixed reference points receive wireless signals from tags to determine their location. Examples of real-time locating systems include tracking semi-finished products through an assembly line or locating pallets in a warehouse.
How does it work?
The principle on which a RTLS is based is not dissimilar from the GPS. Instead of satellites, fixed detectors (or reference points) are located indoors, whereas tags (or asset beacons) are attached to mobile items or whatever is to be tracked. For example, a pallet in the warehouse, a fixture in the maintenance and repair shop, or a semi-finished part in the assembly line. Position is estimated using one or more locating algorithms, such as trilateration, multilateration, or triangulation.
The more RTLS reference points are installed, the better the location accuracy until the technology limitations are reached. As a rule of thumb, the accuracy range is between 10 - 20cm – 1 - 2m.
In most cases the reference points are stand-alone and are powered by lithium batteries, therefore there are no constraints with the infrastructure.
Once the RTLS is implemented, how can we find the asset? Simply by using your smart device (i.e. smartphone, tablet, laptop). It will display your position and the target position on a map. Wearable devices, such as smart glasses, can be also used. In this case the main benefit is the implementation of a hands-free solution.
The communication technology plays a fundamental role as well. Different solutions can be used, the most common of which are probably the followings:
- Ultra-wideband (UWB)
- Bluetooth-Low-Energy (BLE)
Some companies offer the possibility of integrating the GPS into the beacon, therefore making it possible to track your items indoors AND outdoors. This can be particularly useful in case of a complex supply chain in which the process involves several steps among different suppliers. However, a less expensive option would be to embed a detector at your supplier location.
To summarize, there are three main factors to be considered in the implementation of a RTLS:
- Capillarity
- Communication Technology
- Locating Algorithm
Main benefits
As you may already know, there are several reasons to implement a RTLS in your facilities:
- Higher efficiency due to time waste reduction caused by searching for items, and owing to better production flow, as it is easy to visualize.
- It’s cost effective: The price to pay is very little compared to the benefits you get
- Safety: RTLS solutions can be used to trace proximity between people, which is now an essential requirement for Covid-19 prevention
- Security, such as an alert if an item leaves the facility unplanned
Where to start?
Technology is evolving at a very fast pace and the market is offering several solutions to make our facilities smarter. If you are dealing with high complexity in your shop, RTLS are definitely a smart solution to be adopted.
Once the need for such a solution has been acknowledge, the next step is to evaluate the accuracy required: 30 cm or 1m? Then, the capillarity and the communication technology can be defined. Software integration is also an important element: how the solution can be embedded in your IT infrastructure? Finally, the system can be sized and the budget estimated.
Author
Nicola Accialini is an aerospace engineer, senior consultant and digital entrepreneur.
He started his career as a Manufacturing Engineer in the aerospace business for Avio Aero, a GE Aviation Company, then moved to Rolls-Royce Deutschland in Berlin and to Aerospace Transmission Technologies, based in the Lake Constance region.
In Germany Nicola had the opportunity to support the Capability Acquisition team in developing methods of production and assembly of critical transmission modules, including managing the implementation of a new assembly facility. Here, he also had the opportunity to expand my knowledge and areas of expertise by scouting suppliers and attending worldwide fairs and by collaborating with Research Centers in the UK.
Currently based in Spain, he supports international organizations in developing Smart Factories by means of a cultural and technological step-change.
Contact Nicola at nicola@accialiniconsulting.com.