5G, Edge Computing Fueling a New Factory Floor
November 05, 2021
Story
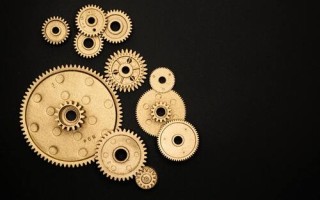
There has been a groundswell of activity around factory automation and enhancing factory efficiency, maintenance, and safety. IBM has been a flagbearer in utilizing 5G, edge computing, and emerging software architectures to make the smart factory a reality. I talked with Rob High, Vice President, IBM Fellow, CTO IBM Edge Computing about the challenges and opportunities 5G is bringing to the factory floor.
Factory Floor Challenges
The majority of factory floors remain heavily manual. The equipment on the floor varies from analog gauges to smart control systems with significant compute, storage, and connection capability. The major challenge comes in how to effectively automate and integrate these systems to automate the work that human workers do, analyze and identify opportunities for improvement, and increase operational safety on the floor.
Rob High believes the combination of smart sensors, 5G, AI, and edge computing offer the solution. “Factory floors need innovation to unlock production quality, increase safety, and enable predictive maintenance. IT and OT have transitioned from competitive to collaborative. From the equipment side, compute is becoming increasingly available in sensors which enables analytics on the floor. For example, using visual sensors locally for detecting safety & quality issues can be done right on the sensor”.
Why 5G?
Connectivity is critical for factory floor automation. Wiring all this together would be prohibitively expensive to deploy and maintain. Wifi has historically interfered with a variety of production equipment – causing disruption, reducing quality and even causing outages. 5G has a good combination of high bandwidth and high capacity that are important drivers for factory automation due to the density of components and the amount of data being generated & analyzed.
A secondary driver is 5G low latency for real-time applications where light processing is happening at the edge with real-time interaction needed end-to-end.
5G Drives Deployment of Important Middleware
5G also make workload migration technologies possible within the factory floor edge environment.
“Linux, Docker [containerization], and even Kubernetes are software technologies that power flexible edge computing applications” High said. “If you have adequate compute capacity in an intelligent camera mounted on an assembly machine, intelligent robot, or conveyer system, these technologies enable the ability to move workloads between cloud, edge, and device to provide flexibility and cost optimization”.
Factory Floor Reference Architecture
Rob mentioned that there is a generalized architecture for factory floor edge computing that involves connecting various “levels” of devices from machine to cloud.
- Level 0 are devices that don’t have compute and simply gather data (positional or vibration sensor).
- Level 1 are traditional OT floor components that execute the manufacturing process. These vary from 8-bit legacy components to feature-rich 64-bit devices with large memory, storage, and connectivity capabilities. They often run traditional embedded software using SCADA and other industrial-specific middleware.
- Level 2 are communications gateways that coordinate communications among the components.
- Level 3 are servers used to house control logic, administration, and perform the high-order computing required for the application.
These varying levels of components deployed on the factory floor are meshed to form the deployment architecture.
Above the deployment architecture lies the software architecture.
- Linux tends to be the primary operating system due to the wide availability of the needed software/middleware components.
- Docker uses OS-level virtualization to deliver SW packages called containers. These self-sufficient containers are portable and can run on cloud or on-premises components.
- Kubernetes (K8s) is an open-source automated deployment, scaling, and management system for containerized applications. Kubernetes enables containers that make up an application to be grouped into logical units and run concurrently with other containerized applications, managing competing demands for shared resources to ensure operational efficiency and elastic scaling.
This provides a powerful architecture with general purpose components where application specific logical architectures can be defined with the ability to distribute workloads across the deployed components in a flexible manner.
Legacy Not Left Out
This is not simply a greenfield effort. Rob sees a strong blend of Level 0/1 legacy systems being migrated into this new edge architecture. However, the transformation is happening at different rates. Level 0 components have seen dramatic transformation due to consumer IoT initiatives. Level 3 components are usually existing IT systems that have evolved to share OT workloads.
The advancement of mobile robots can make analog integration easier. These robots can be used to recognize/interpret analog gauges and programmed with AI from human operator experts to make decisions and deliver data. They are also ideal for workplaces that are unfriendly or even hostile for people.
Factory Equipment Manufacturers are Critical
Factory equipment vendors are critical to the advancement of the factory floor. There is a natural evolution of artificial intelligence (AI) and machine learning into these factory components. IT companies likewise are incorporating heavy doses of OT features.
One good example of this collaboration involves a recent announcement between IBM and Samsung [Samsung and IBM continue to build upon long-standing strategic partnership with challenge for developers using Samsung and IBM technology]. They announced a prototype where the goal is to enable the Docker run-time on Android, and managed by IBM Edge Application Manager (IEAM). This kind of integration implies that all equipment Samsung makes can be designed and certified for industrial settings with full Docker workload interoperability. Android devices bring a myriad of gravity, motion, visual, and audio sensors with 5G connectivity standard and workload processing capability - all at consumer prices.
Key Takeaways
I asked Rob for key takeaways that contributors need to understand about 5G and edge computing for the factory floor.
“First, managing the deployment at the edge is critical. You must run the right workloads at the right place at the right time. This is a problem that we’ve made much easier to solve with IEAM”.
Solving the problem requires a unique mix of 5G & edge computing understanding, industry knowledge, and IT/OT capabilities understanding.
Rob also mentioned security as a key takeaway.
“Second, getting these workloads where they need to be securely. We need the DevOps process to include creation of secure software by making containers scannable for viruses and signed for authentication and tamper-detection. In general, we need to enable the lifecycle itself for security and scalability”.
Rob said network operators often ask him what the killer app for 5G is. He tells them he’s convinced it’s the commercial sector and applications like advancing the factory floor. Consumer application have driven down the price of sensors. But commercial entities know that applying edge computing for AI using 5G as the network fabric is a critical investment in order to remain competitive and differentiate themselves.
What are you doing to contribute to the 5G edge computing ecosystem? Are you involved with factory floor automation? Comment below or email curt.schwaderer@opensysmedia.com. I’d love to hear about it!