Use Mesh Sensor Networks to Overcome Fidelity Issues in Condition Monitoring
October 25, 2021
Blog
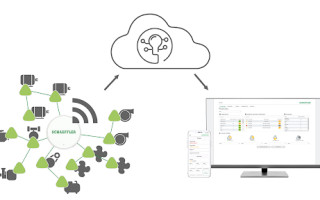
Despite the precision in sensor technology, there is always a shortcoming associated with the performance of monitoring systems.
Despite the precision in modern sensor technology, they could always be better. But, taken cumulatively, as in all the sensors on a sensor network, you can overpower phenomenon like sensor drift by leveraging the fidelity of an entire deployment.
Of course, like all engineering endeavors, overcoming one obstacle introduces another. And in this case, the challenge introduced by turning to a network of sensors is the need for stable, reliable, and interoperable communications between sensors.
That starts with having a wireless sensor network that's cost-effective, robust, and accurate enough to warrant switching from existing single-point condition monitoring solutions.
For example, the Schaeffler Group’s OPTIME solution is a condition-monitoring platform that demonstrates how efficient condition monitoring does not have to be complicated or expensive.
Credits: Schaeffler
The OPTIME platform is based on a Plug-Play-Predict strategy for condition monitoring, and is easy to integrate with complex machinery and systems. It consists of battery-powered sensors that monitor machine temperature and vibration, and can be easily mounted to equipment using regular screws or adhesives. As a result, it’s easy to install, replace, and add additional condition monitoring sensors for a more comprehensive view of machine condition and health.
These sensors communicate wirelessly with a simple gateway that is capable of relaying data from multiple sensors to the cloud. There automatic and continuous diagnostic tests are performed on the data, which are based on Schaeffler’s more than 100 years of experience designing rolling bearings coupled with condition monitoring know-how and integrated machine learning algorithms. This analysis can detect potential damage, misalignments, or imbalances even weeks in advance to help avoid unplanned operational downtime.
Source: Schaeffler
The system also offers an interactive and user-friendly web app, the OPTIME app, that reflects analyzed and raw data available to operators on desktop or mobile devices.
Effortless, Efficient, and Inexpensive Condition Monitoring
According to Schaeffler, the OPTIME condition monitoring system is up to 50% cheaper than manual measurements as it can monitor hundreds of rotating machines at a cost of just a few cents each per day.
At that price point, it’s now possible to install multiple sensors per machine and hundreds or thousands per facility. Then you can finally bring the total power of data to bear on your condition monitoring use cases.